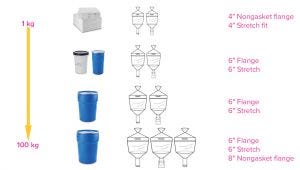
Figure 1: Media containers are available in four sizes up to 100 kg.
Although the handling and preparation of cell culture media can seem routine, a number of risks are associated with such operations. Identification and mitigation of associated risks can help ensure consistency of performance, minimize likelihood of contamination, and protect employees while enabling greater efficiencies in upstream processes. Here we describe a number of strategies for reducing risks and streamlining media-related workflows.
Simplifying Handling of Cell Culture Powders
Media preparation typically is quite labor intensive and poses risks related to containment and employee safety. In response to those challenges, we have engineered right-sized weighing to eliminate the need for our customers to weigh powder from bulk containers such as barrels and buckets. Our goal was to ensure delivery of high-quality cell culture media with precise weighing in an easy-to-use delivery system. We selected the EZ BioPac® transfer bag by ILC Dover for its high quality, fit-for-purpose pharmaceutical film and design compatibility with our company’s outer container to ensure protection of product during shipment.
With this solution, the desired amount of medium is weighed into the top side of the transfer bag, sealed at our site, and delivered to a customer in a protected container. Upon receipt, a customer opens a container, lifts the bag out, and connects that directly to the entrance port of a hydration tank (options for types of connections are available) (Figure 1). Media are easily transferred into vessels with no additional manipulation, no exposure to the environment, and no generation of dust in the hydration tank area. The qualified right-sized weighing process provides customers with documentation and confidence to use each container of powder because the net weight of that container is printed on the product label. A provided report lists the respective data for tare, gross, and net weight by container number.
Our right-sized weighing and EZ BioPac bags offer the following key features:
a film design that ensures complete product recovery and is fit for purpose for the biopharmaceutical industry
accuracy of qualified dispensing methods to eliminate the need to reweigh
the right bag design with options for standard sanitary and stretch-fit connection options for ease of use with standard stainless-steel or single-use operations
robust ergonomic solutions, with built-in lifting handles for small volumes and lifting loops for larger volumes
convenient zip ties or clamp closures for quick product release and bag closure after dispensing.
EZ BioPac bags are engineered for clean, safe, and efficient powder transfer at all scales of operation. Media can be moved from containers directly to hydration, accelerating and streamlining workflows and reducing contamination risk (Figure 2). Precise powder weights are provided, eliminating the need for repetitive activities such as scooping and weighing. To protect media further, a desiccant pouch is included between the EZ BioPac transfer bag and the liner of its outer container.
An added benefit of the EZ BioPac and right-sized weighing offer is our side sample process. Customers have options based on their needs, and the side samples eliminate a workflow step to sample a batch. In some cases, our customers have qualified that approach to the extent that the quality control (QC) results provided on our certificate of analysis (CoA) with the delivery are accepted without additional testing, further accelerating the workflows.
Because media containers are available in sizes from 1 to 100 kg, customers can receive a broad and flexible range to align with their specific volumetric needs. The ergonomic design ensures simple, safe, and secure connection to hydration vessels; several neck configurations ensure ease of use, and handles and lifting loops provide safe and easy handling. An important aspect is that the outer containers holding the media bags have been subjected to International Safe Transit Association (ISTA) shipping studies to ensure that bags are not compromised during typical transit conditions.
A critical component of these right-sized bulk powder packages is the film from which they are constructed. With permanent antistatic properties, the ArmorFlex 114 film enables full discharge of powders (99.9% product recovery) without washdown, ensuring their clean, safe, and efficient delivery into bioprocesses. The film is a linear low-density polyethylene (LLDPE), chosen for its purity, strength, and elasticity, and it meets required regulatory compliance standards:
meets European Pharmacopoeia (EP) 3.1.3 test parameters
passes USP <661> plastic packaging systems and their materials of construction
passes USP <88> biological reactivity, in vivo, class VI (seven-day implant)
passes USP <87> biological reactivity in vitro
offers permanent antistatic formulation, with no added slip or block agents
is animal-component–free and of nonanimal origin.
Improving the Convenience of Dry Powder Media
To improve the handling of dry-powder media, we apply a technology to produce compacted cell culture media. The compaction technology is completely water- and additive-free and applies compression forces to homogenous dry powder media, fixing the homogeneity in place and creating granules several millimeters in size. Compaction does not influence critical media components.
Benefits of compacted cell culture media include
higher density for accelerated dissolution
reduced bulk volume, requiring less storage space
minimized dust formation for improved handling and cleanliness
less caking for better flowability
easier handling during dosage and mixing.
As growth profiles and titer measurement data confirm, no decrease of cell growth, viability, or antibody productivity is associated with the use of powdered media (Figure 3, top). In addition, critical quality attributes of expressed products remain stable, as is shown in the profile of the different glycoforms (Figure 3, bottom).
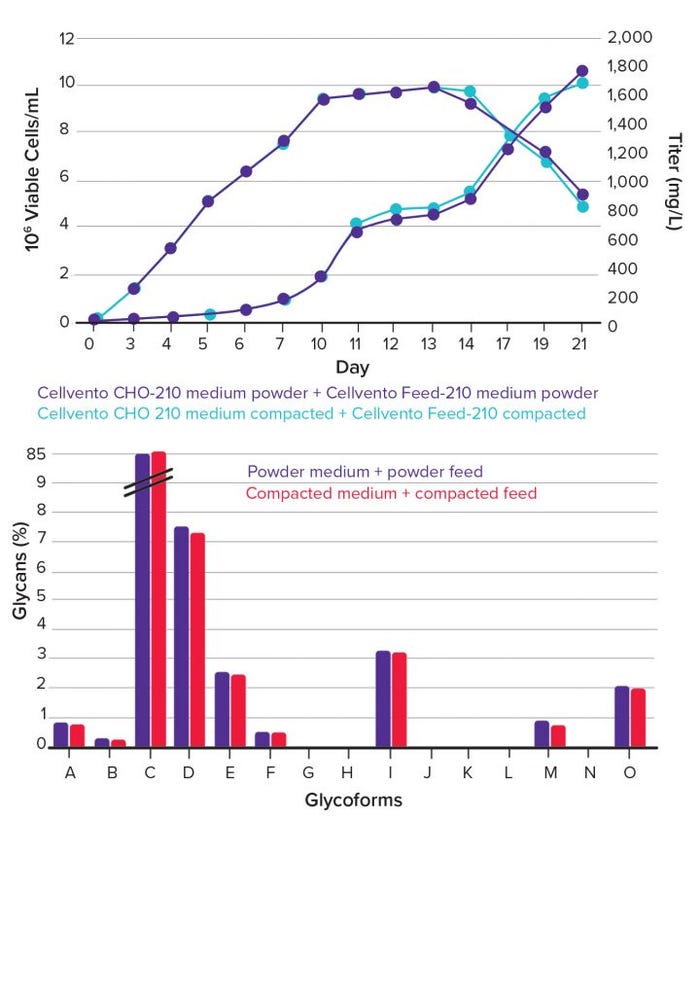
Figure 3: Growth and titer data from fed-batch experiments using compacted feed and medium in comparison to powder components; (top) experiments were conducted in 30-mL medium in 50-mL shake tubes, with feeding every second day; (bottom) customer data on product quality from scale-down fed-batch experiments using compacted feed and medium in comparison to powder components of customer recipe
Enabling Greater Mixing Efficiency
Mixing of floating and sinking powders, especially at high volumes, presents substantial challenges to achieving good dispersion and dissolution of particles.
Mobius® Power MIX single-use mixing systems, available in 100-L to 3,000-L sizes, combine high-performance mixing technologies to mix media efficiently. Axial and radial flow patterns allow for quick distribution of sinking powders, minimizing settling at the bottom of a vessel. Floating powders are drawn into a vortex for effective wetting and distribution throughout the entire vessel volume. That can reduce mixing time for even the most difficult to mix powders.
Mobius Power MIX single-use systems are designed ergonomically with operator ease and safety in mind even at large scales; the stainless-steel vessels have additional features for ease of use. One operator can safely load a bag. The doors open to one-half the carrier’s diameter, and the impeller and drain of the 1,000-, 2,000-, 2,500-, and 3,000-L sizes are positioned offset for easy bag loading. The bag can be secured to pins positioned around the top of the carrier to further help with loading.
Mitigating Risks
Risks from sourcing, preparation, and handling of cell culture media can be introduced at many points along a bioprocess workflow. Proactive identification of possible risks and implementation of strategies to mitigate them will improve consistency and reliability of a process — and ultimately help ensure product quality. Working closely with an experienced, trusted partner for all aspects of cell culture media selection, preparation, and handling can limit your exposure to risks and ensure the quality and consistency of supply for your production process.
Barbara Martinez is global senior product manager, custom cell culture media, at MilliporeSigma ([email protected]). Daniel Senter is senior project engineer ([email protected]). The life science business of Merck KGaA, Darmstadt, Germany, operates as MilliporeSigma in the United States and Canada.