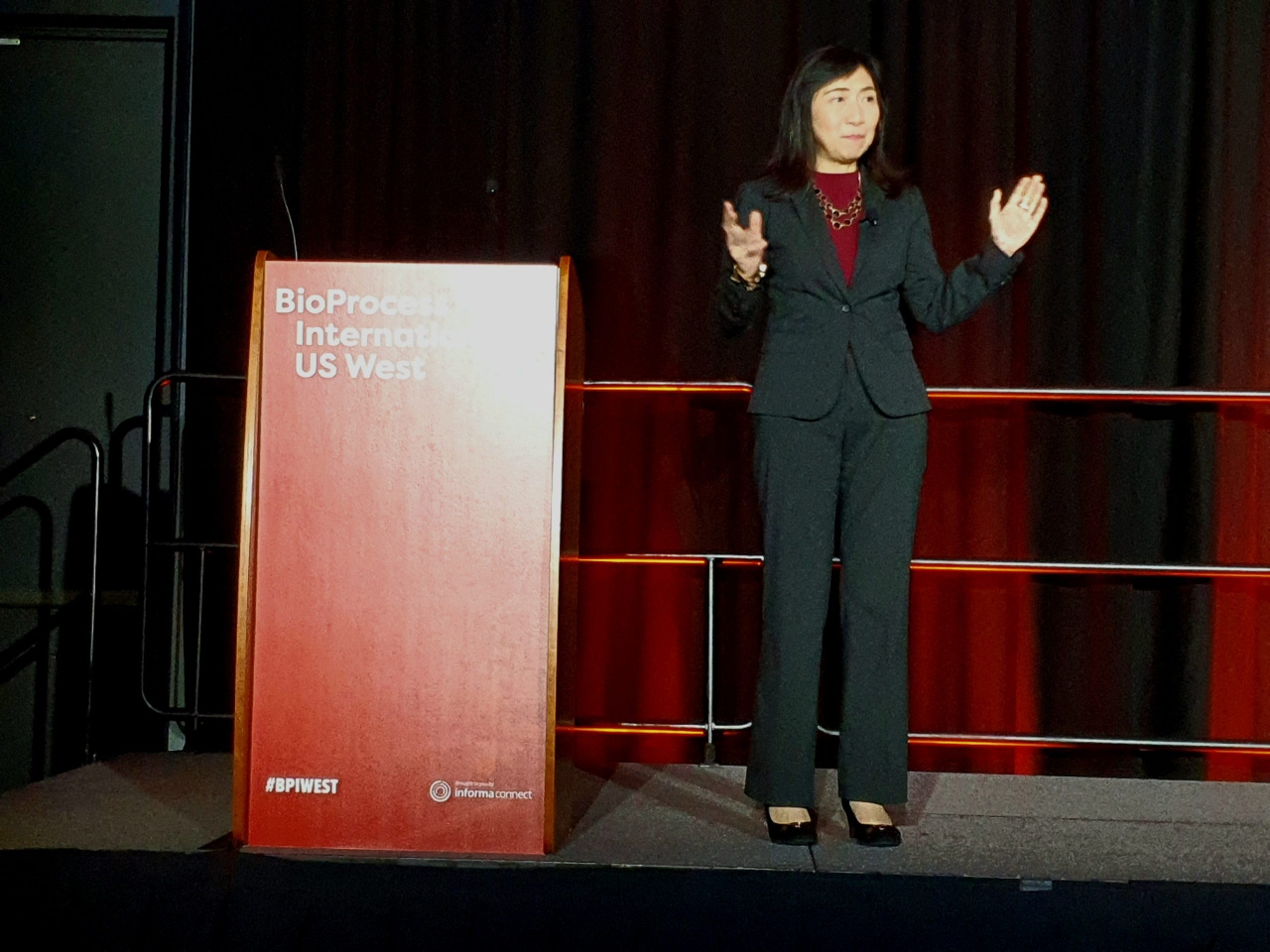
Innovation has realized the potential of advanced therapies, but bioprocess and manufacturing tech advancements are now needed to feed future demand, says AltruBio’s Judy Chou.
While the COVID-19 pandemic kept industry physically apart – making the meet in San Diego this week the first BPI West since 2019 – it brought the biotech space together, resulting in the rapid approval and rollout of the first two mRNA vaccines. Concurrently, the past few years have seen numerous cell and gene therapy successes, with J&J’s myeloma CAR-T therapy Carvykti (ciltacel) the latest example.
But with these “new modalities and high complexity of the process, we need innovation,” Judy Chou, CEO of AltruBio said during the plenary session in San Diego, California Tuesday. “Biotech are two different beautiful worlds merging together,” she continued, with the ‘tech’ world needing to catch up with the R&D advancements within the ‘Bio’ sector.
Judy Chou was speaking at the BPI West event in San Diego this week
She admitted there remains a disconnect in ‘traditional’ manufacturing supporting recombinant proteins – issues in cell line development, scalability in continuous bioprocessing, and imperfect analytical methods, etc – but the sudden advent of new modalities has revealed a much larger detachment when it comes to commercially manufacturing them cost-effectively and efficiently.
Innovation is needed for advanced therapeutics across numerous areas said Chou, highlighting industry’s numerous bottlenecks: The scalability of products, the allogeneic process, comparability formulation development, and potency assays. Simultaneously, the tech side needs to help improve efficiency and sustainability to further advance the delivery of these biotherapies to patients, with Chou looking to elements of industry 4.0 such as digitalization and automation as tools to help drive this.
If the processing space can follow the momentum in R&D, industry will be “ready for the next big thing,” she argued, adding that, whether that is another pandemic-style crisis or just a life-changing therapy for a large population, aligning the two sectors is crucial.
While she lauded the benefits of cheaper and faster production, she also noted how it will help industry forecast better – an issue that has plagued even the most successful drug developers.
Referring to her time at AbbVie (then Abbott), she revealed that the rollout of Humira (adalimumab) was “the most off forecast” imaginable. “Back then when we were developing it, we predicted that over 30 years it would get to about $500 million in sales per year.” The monoclonal antibody is the biggest selling drug of all time, pulling in $20.7 billion in 2021 alone.
“When we think of forecasting [mistakes] we tend to think about people being over-optimistic, but we had a case where we didn’t think it would be a blockbuster and then all of a sudden it hit us. That was the most off forecast we ever had.”
For Humira, more capacity was brought online but that was in a different world where stainless-steel tanks and large-scale industrial plants were the only option. Now, with the new modalities, industry has already begun to embrace agile manufacturing designs and flexible technologies, she said, listing modular plants, single-use systems, automation, and real-time quality release.
With quick tech transfer and portable on-demand biomanufacturing options, industry therefore in a far better position to meet market demand volatility as it brings advanced therapies to fruition than it was in the early days of monoclonal antibodies.
About the Author
You May Also Like