November 16, 2020
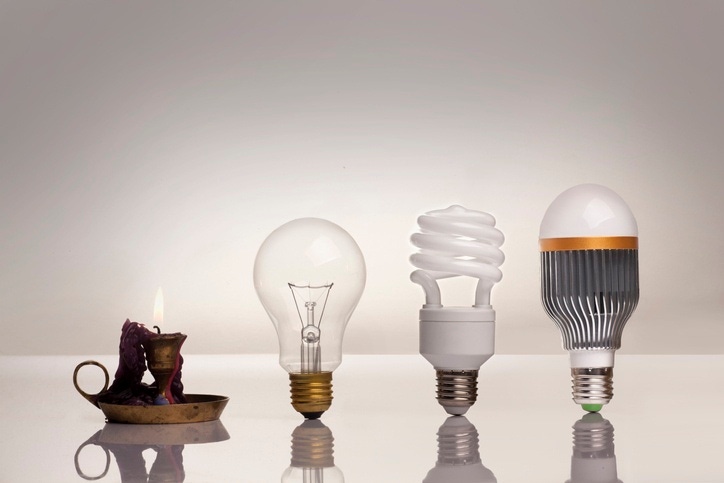
Cell and gene therapy firms should swap outdated human error prone processes for innovative, flexible technologies, says consulting group CRB.
The conclusion is based on the ‘Cell and Gene Therapy Industry Report,’ which included a survey of executives at firms developing advanced therapy medicinal products (ATMP).
The goal was to look at the technologies and manufacturing methods used in the sector and the results suggest the sector has yet to find the best way of making products at commercial scale.
Image: iStock/VladimirFLoyd
Most of the 150 respondents cited variability and uncertainty in their process among primary operations concerns with 80% suggesting process development and optimization among their top three commercial manufacturing challenges.
According to the authors, the findings highlight “an alarming dependence” on “primitive technology and manual applications” developed in the early days of the cell and gene therapy market.
“As we head into 2021, the combination of open processes with a high potential for human error, antiquated technologies, and research-facing technology ill-suited for commercially facing applications creates business risk at a time when market demand for the rapid delivery of patient therapies is rising.”
Embrace innovation
To minimize potential disruption caused by human error the authors suggest industry needs to integrate modern technologies into production processes at the facility design stage.
“Operating space design and layout considerations are vital to the evolution of cell and gene therapy, and responses across our survey reveal gaps in that growth.
“For instance, while nearly three-quarters of respondents indicate automation is impacting operations, nearly one-third report using Grade A biosafety cabinets (BSC) in a Grade B cleanroom—a clear sign of the need to embrace innovation.”
Flexibility
The CRB team also stressed the importance of using technologies that provide flexibility, both in the innovative ATMP space and the contract manufacturing sector.
“Manufacturers and contract manufacturing organizations (CMOs) face the same stark reality: Flexibility is required nimbly address shifting needs in the marketplace.
“CMOs must respond to ever-evolving client needs, and manufacturers who are bringing their ATMP production activities in-house have complex product pipelines and need the flexibility to develop different modalities in parallel.”
And here, some progress is being made. More than half of survey respondents said they expect to adopt a multimodal manufacturing solution within the next two years, with flexibility, scalability, operational efficiency and speed to market as the top drivers.
About the Author
You May Also Like