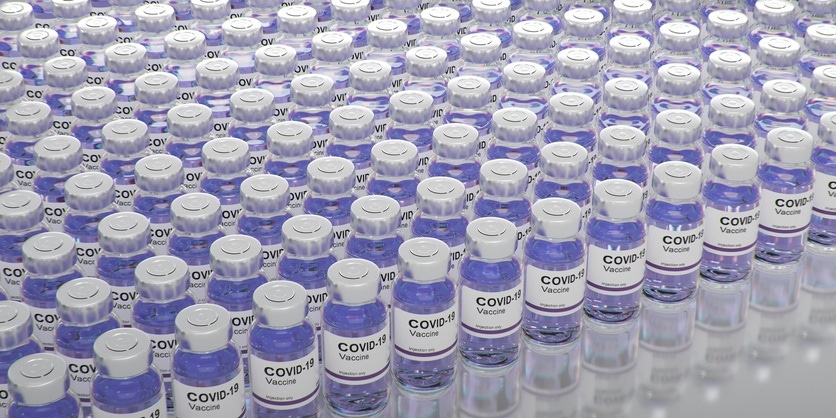
Avitide says a specific SARS-CoV-2 virus spike protein affinity resin greatly helps the current COVID-19 efforts and could greatly accelerate the speed of response in future pandemics.
Bioprocess service and consumable firms are looking to support the next wave of COVID-19 vaccines as they progress through the clinic. Last week, we reported that Repligen and Navigo launched an affinity resin specifically for the purification of COVID-19 vaccines. But they are not alone, and New Hampshire-based firm Avitide recently finalized its affinity purification chromatography resin for the purification of recombinant COVID-19 vaccines.
BioProcess Insider spoke with Karol Lacki, Avitide’s VP of Technology Development, about his firm’s resin AVIPure-COV2S.
Image: iStock/Kirill Reznichenko
Why is a specific SARS-CoV-2 virus spike protein resin necessary?
Karol Lacki (KL): [So far] there have not been any affinity resins specific for the COV19 receptor binding domain, so the vaccine developers that develop vaccines based on RBD or S1 spike protein constructs have had to rely on processes that require several chromatographic steps, resulting in very low yields at the desired purity.
Furthermore, improvement of the overall process yield, due to reduction in process steps, and reduction of processing time, will result in a significant increase in the amount of vaccine produced per batch and the number of batches produced, respectively, thus addressing the vaccine shortages currently reported.
While a specific SARS-CoV-2 virus spike protein affinity resin greatly helps the current pandemic efforts, some companies are already thinking about the next threat and hence universal or platform approaches to vaccine construction and manufacturing. Thus, irrespective of the nature of that next threat there will be a common element to that vaccine and all the other vaccines a particular company is making.
I stress ‘particular company’ because the common element seems to vary from company to company. Thus, while we will continue to develop protein specific affinity resins for viruses we also have initiatives to create affinity resins for these common elements. This is a new style of pandemic preparedness that we are excited to become involved in.
The affinity resins have the potential to greatly accelerate the speed of response in future pandemics and biological threats. In future years the world will look back and say if there was any good to come out of COVID19 it will be that the world was better equipped with new technologies to tackle future threats. Avitide is proud to be contributing a small but important part to this effort, and we are grateful to our collaborators’ vision and insight to be included in their mission.
How do you produce the AVIPure-COV2S resin, from where, and in what quantities?
KL: It is very similar to how protein A resins are made, in fact the base bead is used in a very successful protein A resin. The ligand is an alkali stable recombinant protein that is produced by a microbial production company, exactly the same as the protein A ligands are produced by a few manufacturers throughout the world. We marry this ligand with a modern 50 um agarose base matrix that we purposely selected for this product from one of the major agarose resin vendors. This bead is produced at very large quantities and as I mentioned the base for a widely used protein A resin.
We take these two critical raw materials and bring them to Lebanon NH, where we perform the conjugation of the ligand to the bead within our ISO9001 accredited facility. This facility continues to expand and we recently expanded our management team, establishing a VP of Commercial Supply Operations to support the production of these products.
After packing and quality control release, this combination allows for high binding capacities, relatively, regardless of the target size as well as on repetitive use of the column that significantly reduce the cost of the resin. With our resin, contribution to the cost of goods is reduced to a few cents per dose. Which is a several fold reduction as compared to COGs associated with current processes.
Are there any plans for scale up?
KL: That was the intention from the very outset. A resin like this needs to be on the manufacturing floor if it is going to make a difference to how people are treated and when.
Clearly there is a global imperative to produce as many vaccine doses as quickly and efficiently as possible and we want to be a part of that effort. The feedback we receive is that manufacturers are targeting large bioreactors, which will require large columns reminiscent of mAb processes.
Consequently, Avitide is anticipating 1,000 L of AVIPure-COV2S resin this year and capabilities for greater production to meet demand. One shouldn’t overlook the effect of the stability of the resin in helping to meet that demand. Because of the long resin lifetime and ability to reuse it throughout many production batches the actual resin consumption is reduced considerably. Ironically, this actually hurts our resin sales. Whilst a less stable resin would be used less times before being disposed of and replaced, this is not in the vaccine manufacturers best interests or frankly, the world’s best interest and the greater good. Optimum efficiency is required and we are very proud of how quickly we were able to engineer the resin for stability.
I should also add that all the focus upon scale shouldn’t ignore the other end of the spectrum. There are countless tireless researchers across the world whose studies will also benefit tremendously from small scale quantities. Some of this research has the potential to dramatically impact the course of the pandemic and hence we need to empower those researchers too. Consequently, we are also scaling small lab-scale prepacked columns to service the academic and research centers.
How does your resin differ from the Repligen/Navigo offering or any other SARS-CoV-2 virus spike protein specific resin?
KL: I am not privy to the other vendors data, but I can say that our resin is alkali stable, can be CIP with 0.5 M NaOH repeatedly without a loss of chromatographic performance, including capacity, yield, purity, etc. It is based on the top-class agarose base matrix offered by a major bioprocess resin vendor.
Since there is no information about other resins used explicitly for purification of COVID-19 vaccines it is difficult to compare. As you are aware no data has been provided yet on the new resin. We are happy to work alongside them with this shared interest in furthering the pandemic response. Just as there are multiple vaccine efforts that are each providing tremendous results and meeting the needs of billions of patients across the globe, so too are multiple affinity resins required. This is a collective effort.
About the Author
You May Also Like