November 9, 2020
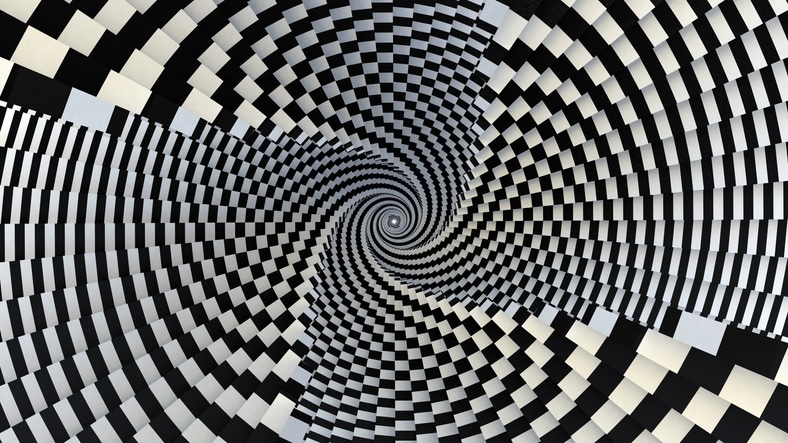
Continuous processing technologies and methods should be tested with actual production processes says Tom Ransohoff from CDMO 4th Dimension Bioprocess.
Continuous-mode manufacturing has been a hot topic for the drug industry for the past few years but, as yet, few companies have fully embraced the approach and even fewer have switched from fed-batch production.
But the change is coming according to Tom Ransohoff, COO at recently founded CDMO 4th Dimension Bioprocess, who told delegates at the BPI East conference in September the advantages of continuous mode are becoming impossible to ignore.
Image: iStock/thiago melo
“We really do see significant benefits in a number of areas from applying this approach to manufacturing, including improved speed both to clinic and to market. Significant improvements in manufacturing flexibility and the ability to respond to varying demand.
“There are also significant capital efficiencies. The ability to produce more product in a smaller footprint and a less capital-intensive way of manufacturing. And finally, we think there is growing evidence that this approach to manufacturing should improve our ability to control product quality.”
Little and large
Continuous manufacturing is a growing area of activity for the entire pharmaceutical industry – both the large and small molecule sectors – according to Ransohoff.
“There’s already at least six approved small molecule products manufacturing using continuous processing approaches. There’s significant investment both in the larger biopharma companies as well as some CDMOs.”
Ransohoff highlighted companies like Merck, Bayer, Amgen, Janssen, Novartis and Sanofi as some of the firms embracing continuous manufacturing.
He added that “there’s a regulatory framework being developed and defined for continuous manufacturing and certainly regulatory support for this approach,” citing the ongoing work on ICH Q13 as an example.
Sandbox
4th Dimension Bioprocess – which was founded last year – markets itself as the only US-based CDMO exclusively focused on continuous bioprocessing.
The firm plans to work with viral vectors, recombinant proteins and mRNA. However, its initial focus is on monoclonal antibodies Ransohoff said,
“Monoclonal antibodies are industrialized and produced with well-established processes and platforms, so we can really focus on the work to solve the operational and tactical problems of getting a reliable, robust GMP manufacturing operation running in continuous mode.
“Also antibodies are a large and growing market, despite the fact most of the press is focusing on cell and gene therapy products… The pipeline is very robust for antibodies and antibody related products with over 1,000 products in clinical development and many more in preclinical development.”
To cater for the mAb market, the CDMO plans to develop a development “sandbox” where new ideas and systems can be trailed in a setting that is as close to real world manufacturing as possible.
Ransohoff said, “As former founders of other businesses developing technology for continuous manufacturing, we recognized how difficult it is to get new technology ideas tested in an actual working manufacturing process.
“So what we plan to do is build a test platform using a biosimilar mAb that is not a commercial product but just a model product that is relevant… that will allow us and other to generate data using new technologies, new approaches.”
He cited in-process monitoring and data analytics as likely areas of innovation, explaining “we think these will be important for improving our ability to manufacture products continuously.”
The firm also plans to generate the data in a way that can be published and shared so the wider industry can benefit from the evaluation of new technologies, instrumentation and systems.
Learning process
For process development 4th Dimension plans to keep the final manufacturing platform in mind according to Ransohoff.
“Process development work will begin with a platform in mind. The goal will be to operate as close as possible to the platform framework. This enables the same types of benefits generated by platform process operation in fed batch processes…We can leverage platform knowledge across many products where relevant.
“One of the things we plan to explore is the ability to adjust parameters off of a steady state and monitor impact as a way to run experiments in continuous processing. When coupled to analytics we think this will provide the opportunity for rapid feedback loops and streamlined ways of developing process understanding.”
About the Author
You May Also Like