Vaxess says one of its biggest challenges in delivering a patch-based vaccine is there is not a contract manufacturer with the expertise to produce the product.
Vaxess, a company that aims to engineer more effective and accessible vaccines and therapeutics by focusing on the skin as an active immune organ, is developing a patch-based delivery system. Its lead program MIMIX-Flu is a seasonal influenza vaccine that is mailed directly to patients’ homes for self-administration.
The patch works by applying it to the skin for five minutes. Once applied, tiny micro needles go into the skin.The microparticle payload is only in the upper tip of the needle. The micro particle then delivers the vaccine to the individual over a two-week period.
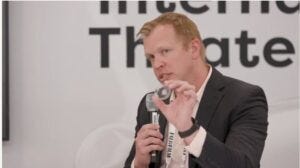
Michael Schrader spoke at the BPI Theater at BIO
While the self-administration process sounds straightforward, the manufacturing process is not as simple. Speaking to BioProcess Insider at BIO in Boston, Michael Schrader, CEO at Vaxess, said “one of the biggest challenges for us is there is not a contract manufacturer that we can go to and say please make this for us.”
With no feasible option to outsource, the firm has established a manufacturing facility in Woburn, Massachusetts. Schrader described the manufacturing process at the Woburn plant as “highly automated” and said it essentially “uses a very fancy inkjet printer.”
“Think of a mold that’s loaded into an inkjet printer.That mold is basically a negative of the patch, the inkjet printer has a very high-resolution camera, it can identify where it is relative to the patch. And then it actually comes in and presents very tiny droplets into each individual needle to fill that mold. There’s a short drying process, and then we go back in and do that one more time. And then the adhesive backing is applied demolded and packaged. It was a process that we really had to develop from scratch to get, you know, high quality, consistent dosing into the patch.”
According to Shrader, the firm has identified other challenges companies have faced when trying to manufacture patch-based delivery vaccines. As a result, another recognized challenge “is getting a consistent dose into the patch,” which is why the “precision printing process” is so important to us.
Another complex manufacturing requirement to solve is “the differences in patient’s skin based on age, tissue structure, and hair content,” said Shrader. Thus, the ability to design and manufacture a patch that delivers efficiency, regardless of the skin type has “proved to be a big challenge for us.”
To tackle this issue, Shrader told BioProcess Insider’s Millie Nelson “a lot of engineering went into the design that patch so that no matter the skin type, we know how much we are delivering to the patient.”
While the company can be described as “product developers,” Shrader said the those at the firm also see themselves as “system developers.” The patch is one element, but there is also an applicator that has been “purpose built for patient self-application to simplify the process” and the thought process runs through instructions, training, packaging, and ordering procedure.
“So really, I think it is full user experience and system design that we’ve got to think about, which to me is really fun, because it [goes beyond] just designing a device or a product.”
This is one of the reasons Schrader said it is “not a traditional device company, but we need people who understand the device development process.”
Talent
The lack of qualified staff in the life sciences space is well documented, with professionals forming a general consensus that the industry’s growth does not match the amount of talent coming through.
With complex manufacturing processes, Schrader said Vaxess has “been so lucky to find the broad range of talents that we needed for this.” He added it is “not a traditional biotech company” but it still requires employees who “understand processing and the formulation of biologics.”
Another element of understanding the device is “that the manufacturing process is a kind of machine vision guided robotics process.” When thinking about hiring talent to work for the firm, we thought “of the robotics talent and vision system talent that we find in the ecosystem, and we had to draw from all those expertise.”
Vaxess’ MIMIX-Flu vaccine patch released its Phase I trial results in June. “We found the vaccine delivered an immune response that was consistent with existing commercial products with two main improvements.” Said Schrader.
“The first is the durability of protection was significantly better than existing flu vaccine [and] we think it’s due to the slow release of the vaccine in the skin driving that. The other thing we looked at with was breadth of protection […] and we saw very, very good protection against that as well. The final I’ll say surprise for us was that the safety profile for the patients was actually far better than what we see with licensed vaccines.
Its Phase II trial is anticipated to start sometime next year.