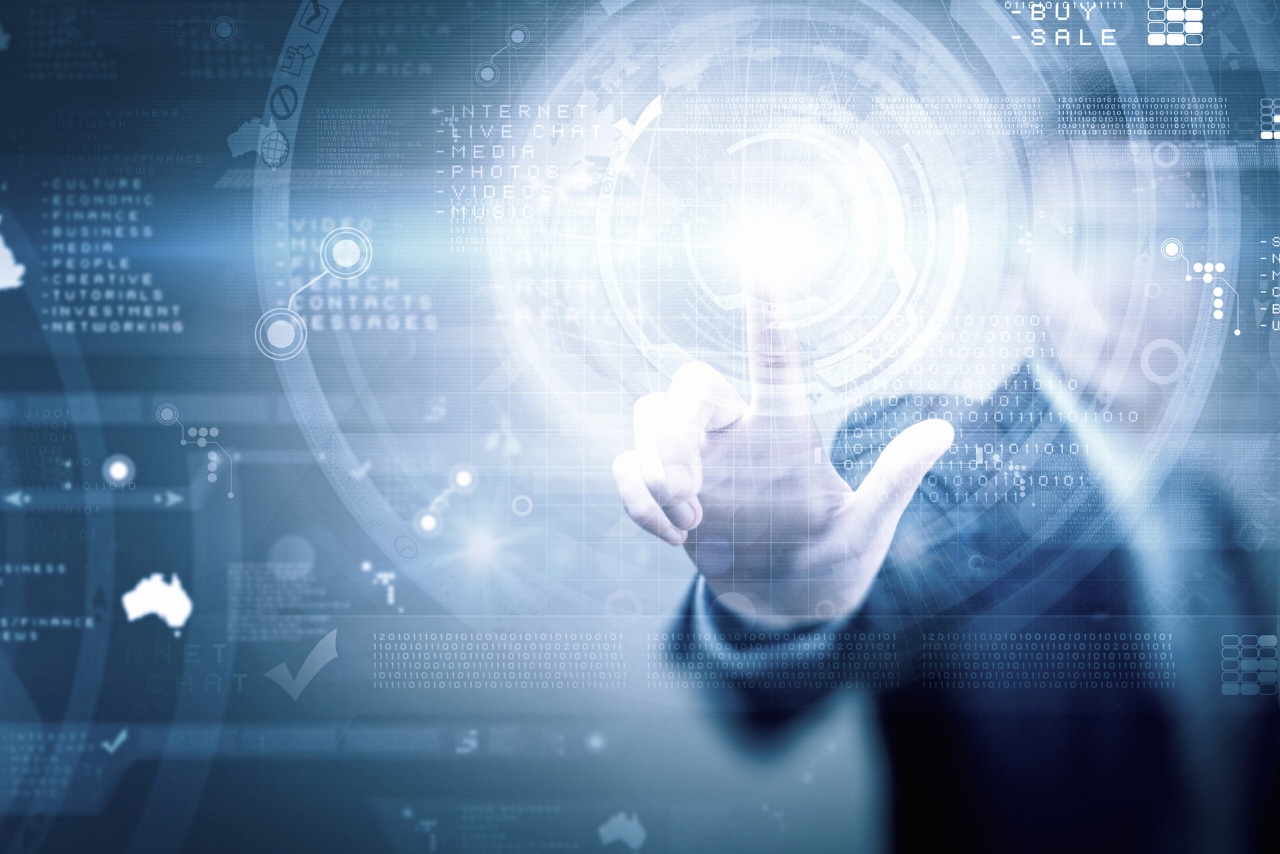
Merit says the adoption of digital technology has enabled it to construct biopharmaceutical facilities three times faster than the industry standard.
According to Merit, a major issue in the construction space is the scarce implementation of digital technologies.
However, the firm decided to rethink, reengineer, and reform how to deliver a construction project, leading to the creation of an integrated IT platform and digital form of construction using Revit, a software to plot and track stages in the building’s lifecycle alongside BIM (building information modelling).
Image: Stock Photo Secrets
“The construction industry is fragmented, insofar as you get Engineering, Procurement and Construction Management (EPCM) or consultant designers, and then separately, contractors, and then they subcontract to a supply chain,” Tony Wells, CEO at UK-based construction specialist Merit told BioProcess Insider.
“We don’t have this fragmented delivery approach. We don’t have any consultants and we do our own design. We are the main contractor ourselves, and then we self-deliver most of the internal content in our own factories, and then on site.”
BIM provides digital representations of the physical and the functional characteristics of structures. Merit said it developed its own “extended BIM model in-house, which is built by our vertically integrated Virtual Design and Construction (VDC) team to develop 3D models to millimeter accuracy, facilitating the export of drawings directly from the model. It can be used to plan, design, visualize the construction sequence, construct, operate and maintain facilities.”
Merit claims it has added additional dimensions to the system, “including a fourth dimension to oversee installation sequencing (in order to reduce delays and costs), and are in the process of building the fifth dimension a real-time costing schedule, the sixth dimension to measure embedded carbon, as well as the seventh dimension simulating monitoring behavior of the real building, which can provide guidance for sustainability and energy-efficiency solutions to be implemented for the proposed facility.”
Three times faster
GMP compliance and qualified person at Merit, Pauline Johnstone described the firm as a “one stop shop,” and noted how the COVID-19 pandemic drove the acceptance of an accelerated approach and pushed firm’s to “look at alternative technologies to get to market faster.”
By creating “digital twins of the products that we make and then producing them in our own factories,” we are “approximately three times faster than anybody else in producing a new biopharmaceutical facility,” Wells told us.
“We wanted to come up with a solution that was so compellingly different and better [that] no other offer would make sense,” said Wells.
“It’s not about tweaking how a construction project would normally be done, it’s about starting from a clean sheet of paper, researching it and, coming up with a solution that is faster, cheaper, more flexible, particularly around biopharma processing.”
One example of Merit’s work in the biopharma space is Autolus Therapeutics’ cell therapy facility in Stevenage, UK – the firm broke ground on the 70,000 square-foot building in November 2021.
About the Author
You May Also Like