Enzymatic DNA manufacturer Touchlight has repurposed a derelict waterworks in London, UK and redeveloped it into a DNA production facility.
While it is not common practice that a Victorian derelict waterworks located near to the River Thames in Hampton, London is repurposed into a DNA manufacturing plant, CEO of Touchlight, Karen Fallen told BioProcess Insider “this was a unique option presented to us, and we didn’t want to pass on the opportunity to be situated in such an attractive location.”
The building was originally constructed to tackle a cholera epidemic by delivering clean water into the city during the 1850s. “The fact that the building was at the cutting edge of technology during the Victorian period, and now once again it is at the forefront of technological advancement, enabling the genetic medicine revolution, is a truly unique story,” said Fallen.
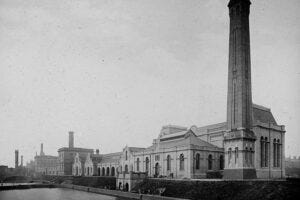
The building before repurposing. Image c/o FTI Consulting
The firm started work in June 2021 but could not disclose the financial costs associated with repurposing the facility. However, Fallen said the build-out did not take longer or incur more cost than selecting another type of plant.
The expansion has tripled the manufacturing capacity of the facility, and the firm claims it can now produce over eight kilograms a year. Moreover, the firm said this surpasses the current and growing worldwide supply of DNA for genetic medicine. The plant includes 11 suites, two filling suites and warehousing with quality control capability.
Fallen told us there are many advantages associated with repurposing a building and transforming it into a manufacturing space. One of the benefits is speed, “from a timeline perspective, repurposing means not having to build the facility from its shell, and also it avoids building a greenfield facility.”
Additionally, the space has a large footprint and the “beautiful Victorian buildings which, now converted, provides a stunning and iconic facility that is an inspiring place to work.” In turn, the workspace has been “designed to encourage and support a creative and innovative culture, alongside the delivery of […] products and outstanding performance.”
Fallen also pointed out the advantages of the location of the plant as it is situated closely to London, Oxford, Cambridge, and benefits from the M4 corridor.
Challenges
However, l, Touchlight’s plant build-out came with its own challenges, described by Fallen as “threefold.” Firstly, because it consists of heritage buildings, it is subject to specific conservation requirements meaning “that any changes do not alter the exterior and in any way diminish the history of the buildings.”
Furthermore, Touchlight must have a facility that can meet GMP manufacturing status in order to reach production potential. Therefore, the firm had to make the design process a key part of the project and regularly had “detailed discussions taking place with the multiple stakeholders (heritage building authority, local residents, Touchlight manufacturing team and design engineers).”
However, despite these challenges, Fallen said the company believes it has “created something which meets all our objectives and speaks well to the ambitions and ethos of Touchlight more generally.”
The expansion comes after the authorization of a Drug Master File and investigational new drug (IND) application using doggybone DNA (dbDNA). The technology creates a small, linear, double stranded, closed DNA vector through an enzymatic production process and is rapidly scalable.
The firm has previously said dbDNA can overcome the costly manufacturing limitations of plasmid DNA and the complex formulations and cold-chain issues of messenger RNA (mRNA).