Ian Lichfield, CEO of WHP Engineering figuratively sat down with BioProcess Insider to discuss the key things to consider when planning a facility and how the business will adapt to suspected future changes.
WHP Engineering is located in Newcastle, UK and describes itself on LinkedIn as a “multi-disciplined, engineering company dedicated to providing both standalone and turnkey solutions for highly-regulated, controlled environments and complex manufacturing processes across Europe.”
The firm works with a wide range of customers in the life science and clean industrial markets, including Oxford Biomedica, GlaxoSmithKline (GSK), Touchlight, and Merck.
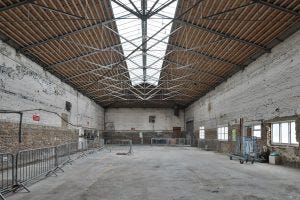
Synthetic DNA plant WHP are building for Touchlight. Image c/o WHP Engineering
BioProcess Insider (BI): What are the key things to consider when planning a facility?
Ian Lichfield (IL): Understand your process architecture and user requirements. Process architecture means understanding how you want raw materials and resources to enter the facility, how you want them to be processed whilst there and how you want the finished product to be packaged and transported when they leave the facility.
BI: Are there any other considerations?
IL: Considerations such as HVAC zoning, room adjacencies and relationships, utility requirements and waste management also need to be considered. User Requirements usually involve us conducting a ‘day in the life of’ study for the facility. This effectively determines how the client wants to operate the facility. This will include number of production cycles, shift patterns, 24-hour working, the number of operatives which will determine levels of automation. In addition, important issues such as how hazardous materials are handled safely and eliminating operational risks.
BI: What other questions are important for your customers to consider?
IL: Any project has three drivers: Quality, time, and cost.
Quality – It is always a given with a WHP project but often we operate in regulated environments so compliance to external standards may be the key driver to gain approvals to operate the facility.
Time – Fulfilment of an existing order may be driving your decision and a delivery strategy may need to include a modular solution to avoid delays or a more intense delivery program.
Cost – If cost is the number one driver then cost-effective delivery and value engineering may be top of your list.
BI: What would you encourage your customers to do?
IL: Identify your key driver, don’t just take the easy option, and list all three. If time is critical does the mitigation of very high late delivery penalties mean you are prepared to spend more on a delivery strategy? If your budget is finite be prepared to look at value engineering which may mean less automation or reducing capacity or process time for example.
BI: Location must also be a vital part of this process; can you expand on this aspect?
IL: This may seem like a simple question, but you would be surprised how often the decision isn’t fully explored. Often clients look to add to their existing facility or find a pre-built building close to their current location.
BI: What questions would you ask the customers that want to add to their existing facility to consider?
IL: Does the existing building have enough space and is that space suitable for the application? Do you want to use a brownfield or greenfield site as each has its pros and cons?
Consider critical factors such as access to markets, the location of raw materials and key suppliers and the availability of labor [and] planning issues for new builds, converting premises or extending existing buildings, possible grants, and funding incentives available in development zones.
BI: How does WHP support its customers through this period of time?
IL: WHP often gets involved in projects at their inception which means we can help our clients navigate this process. Our experience as a principal contractor means we can deliver new builds, extensions or re-purposing existing properties, including historic listed buildings.
BI: What else should customers consider when selecting what type of building they want to locate the facility in?
IL: Your business may have set environmental goals for carbon reduction and this may impact the type of building you want to locate your facility in, the design and equipment you want to use to reduce energy consumption. In addition, the amount of power you will require needs to be considered and if it will need upgrades. Finally, how will waste be treated so it does not impact the environment and can be disposed of effectively and efficiently, ideally being repurposed.
BI: What does WHP to address sustainability concerns?
IL: WHP has been working with Ecovadis on its sustainability strategy for 3 years now and this encompasses not only how we operate as a business but also how we incorporate sustainability into our designs and construction. Recently we have been collaborating with a company that is developing zero carbon solutions for primarily the food sector, but the applications of the technology are far wider. WHP will be bringing its design, fabrication, and installation skills to a first of its kind zero carbon solution in the new year. We see this as critical step in offering our clients new and affordable solutions to the sustainability agenda.
BI: What changes do you expect to see in the future?
IL: The use of single use technologies in the biomedical environment means traditional multi-use facilities are no longer required. The environmental agenda means energy efficient processes and renewable will be far higher on the agenda. The progress in design software and interactive solutions are bringing a far more interactive process for clients and this will continue. The time to deliver facilities is constantly under pressure which means that the modular build solution is now becoming higher on the agenda.
BI: How will WHP adapt as a business to these changes?
IL: WHP has developed partnerships with some of the UK’s leading component manufacturers such as Steris and Alfa Laval (WHP is now an Alfa Laval approved installer). These partnerships give us access to a wealth of solutions and technical support to guide our customers to the optimum solution. WHP has been building modular process solutions for many years but recently it has delivered a large scale modular clean room facility as well. Although modular is a solution we do not believe it is the answer to every problem and we tailor our solutions to our customer’s needs. In addition to modular there are a lot of lean manufacturing techniques that can be brought to a project to reduce delivery times.