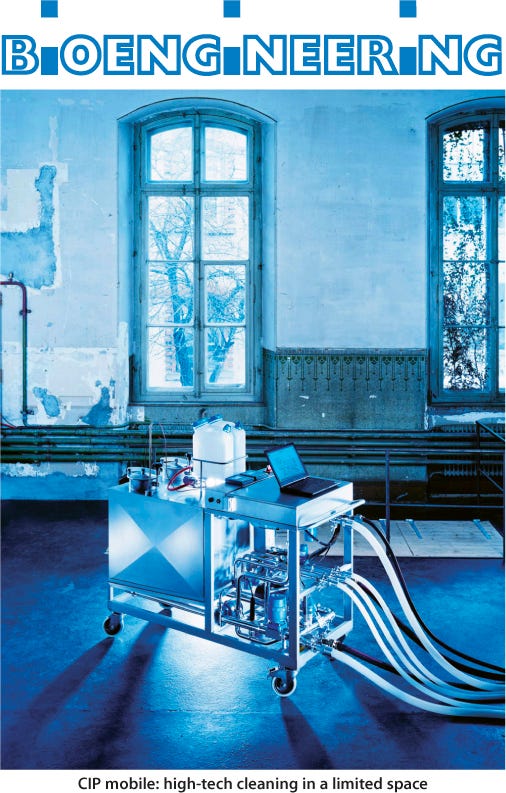
Bioengineering AG looks back at over 35 years of experience in the planning and construction of biotechnological plants. Holistic solutions have become the status quo: from inoculation to harvest, from feed line to CIP-system, and from automation to validation. Because we do not want to limit our know-how to customers fermenting with Bioengineering equipment, we made components for all process steps available as single parts. To support progress in biotechnological processes, we also develop custom-made components for special applications.
Operational Safety
Crevices, deadlegs, and leaks are potential sources of microbial contamination or environmental hazards in biotechnology. Valves and sterile couplings are necessary for process control and maintenance, and often constitute the transition from unsterile to sterile plant segments. Bioengineering manufactures sterile couplings with deadleg-free passage and seals flush with the pipe wall. Hygienic diaphragm valves are available from manually operated one-way valves for simple applications to fully automated multiway valves for sterile crosses, ring distributors, and transfer panels. Leaks in the system are prevented with hermetically sealed magnetic agitation systems, aerosol-free Hi Containment sampling, and harvest valves with bellows construction.
Measurement, Control, and Automation
Control of agitation, temperature, pH, and DO is vital in biotechnological cultivations. Additional control of parameters such as gas composition, foam formation, off-gas analysis, or dosage of nutrients and inducers can improve product yields significantly. Bioengineering’s BioSCADA software not only visualizes and controls the process with or without distinct local controllers, but also documents generated data and performed operations. Integration of a variety of interfaces creates flexibility in process management and enables progressive upgrading. Intelligent selection of control loops, concise automation, and data analysis establish perfect processes and ensure product safety.
Special Cultivation Processes
Many innovative processes cannot make do with the traditional stirred tank alone. Bioengineering’s rotorfilter supports the perfusion process of cell cultures without clogging and fouling as a standalone unit or integrated into the bioreactor. Adherent cells are cultivated in a radially perfused fixed bed insert that is mounted into existing vessels.
Extremophile and marine microorganisms require cultivation conditions that corrode stainless steel. In Bioengineering’s PEEK fermentor, all stainless steel parts are replaced with PEEK high-performance thermoplastic. This enables culture in high-salt conditions even at high temperatures.
Cleaning Efficiency
Cleaning processes must be thorough and reproducible, economically feasible, and ecologically advantageous. With RotaCIP, CIP mobile, and the CIP-valve, Bioengineering has designed innovative equipment to streamline the CIP-process, to reduce chemical and water consumption, and to minimize contamination risks. RotaCIP is a rotating CIP-lance equipped with a spray ball. Rotation increases the spraying intensity, reduces cleaning time, and eliminates spray shadows. The CIP-valve sprays the vessel with a jet nozzle from below. The fully automated CIP mobile features controlled recycling of chemicals, quality control, and full documentation. As single components or in combination they increase efficiency, safety, and operability of the cleaning process.