- Sponsored Content
- Downstream Processing
Continuous Capture Chromatography, A simple, Robust Approach to Move From Batch to Continuous Capture
June 22, 2017
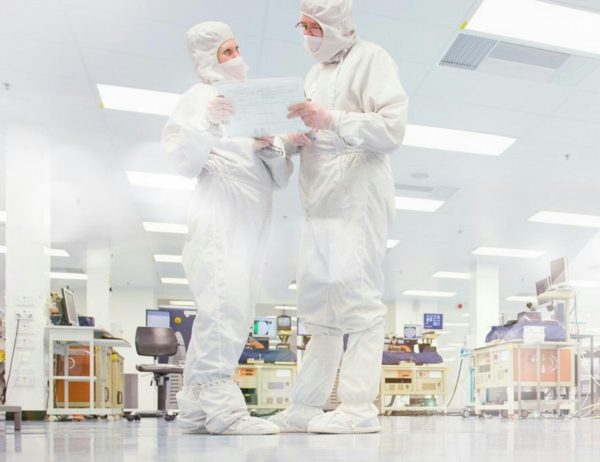
Already have an account?
Sponsored by LEWA
Increasing demands for the production of biopharmaceuticals, such as monoclonal antibodies (mAbs), vaccines and recombinant proteins, require new, innovative purification approaches with higher efficiency and productivity while maintaining or reducing costs. One of these approaches is continuous capture chromatography.
Continuous capture chromatography, also known as CaptureSMB was developed by ChromaCon AG. CaptureSMB is a 2-column periodic counter current chromatography (2-PCC) process where the first column is fully loaded and breaks through to the second column. The first column is eluted while the second column is loaded. After the initial loads, while one column is being loaded, the other column is eluted and made ready for the next load. The cycle is repeated until the entire batch has been processed. ChromaCon has a laboratory scale instrument, the Contichrom® CUBE that performs continuous capture chromatography as well as other chromatographic functions. The LEWA EcoPrime® Twin LPLC system is the pilot and production scale equivalent that employs ChromaCon’s patented continuous capture methodology and is intended for use in GMP environments.
This paper describes two monoclonal antibody purification case studies where traditional batch capture with Protein A was transferred to a continuous capture process on the EcoPrime Twin. Method transfer from batch capture to a continuous capture is straightforward involving the same chromatographic steps, load, wash, elute, regenerate, and re-equilibrate. The case studies provide insights into process design and optimization of the continuous capture process that enhance productivity and resin utilization.
The case studies demonstrate that for continuous capture, EcoPrime Twin enables faster processing (up to 2 times faster), Protein A resin utilization improvements of 40 – 60% while at the same time reducing buffer usage significantly. The results are achieved with a simple two-column design that is easy to understand and operate, reduces risk when implementing in manufacturing, facilitates qualification and validation, simplifies maintenance, and minimizes costly down-time and operating expenses.
About the Author
You May Also Like