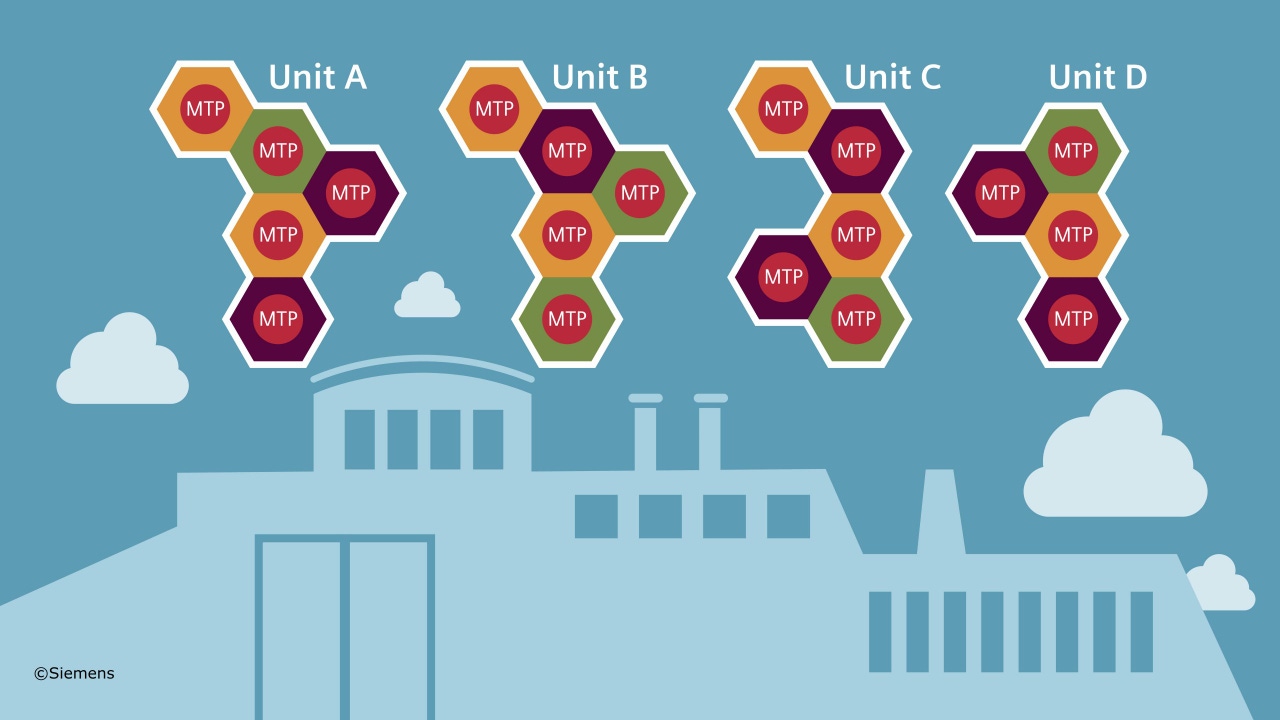
Merck KGaA will construct a €10 million ($12 million) modular plant at its site in Darmstadt, Germany as part of a collaboration with Siemens for the digitalization of production.
The partnership aims to advance the development of a process control system for the manufacture of Merck’s products – including biopharmaceuticals and life science tools – by using Siemens’ tech platforms for the joint development of an overall system for automating the modular production.
“We are able to setup any kind of chemical synthesis and workup process based on our modular concept, with this we are not limited to products or even regulated materials such as active pharmaceutical ingredients,” a spokesperson from the Big Pharma firm told this publication.
Flexibilization of a plant, c/o Siemens
The initial stage of the collaboration will see Merck invest € 10 million to construct a modular plant at its Darmstadt site and headquarters. The facility will also benefit from funding from the German Federal Ministry of Economic Affairs and Energy, and falls under part of plans by Merck to invest upwards of €1 billion across the site.
German automation firm Siemens will develop a supervisory control system, known as process orchestration layer (POL), offering various production modules that can be interlinked to an overall process.
“The POL enables us to use standardize modules in the same scale from R&D to production,” we were told. “With this we are able to provide a useful framework for manufacturing scale-up following the FDA’s ‘scale-up and post approval changes’ (SUPAC) guidelines, which rely on highly beneficial equipment of the same SUPAC class, available for development, scale-up and commercial manufacturing.”
Merck is not the first firm to introduce modular and digital technologies to its manufacturing network, nor the first to partner with Siemens. German CDMO Vibalogics, as an example, added a Siemens process control system at its site in Cuxhaven last year.
Meanwhile, Amgen, is building a $160 million “next-generation biomanufacturing plant” in Rhode Island based on enabling technologies including single-use, modular design, process intensification, and digitization.
Speaking this week at the Evercore ISI 3rd Annual HealthCONx Conference, CFO Peter Griffith said of the plant that “digitization is important, so we’re allocating capital to that.”
Read more: Automation can help biopharma enjoy the benefits of continuous processing says CPI
About the Author
You May Also Like