The Human Factor in Facility Design Innovation
December 1, 2010
Bioprocess and pharmaceutical production environments must be well designed to meet strict cleanroom and quality assurance (QA) standards and productivity requirements. Managers may also consider innovative ways to enhance the design of these environments to enable the people critical to their companies’ success to be more productive and effective. In today ’s work culture, countless hours can be lost to poor teamwork and ineffective communication. CGMP environments present additional, unique challenges to human interaction because of their built-in process and protocol barriers.
Effective space planning and design alone cannot create a culture of teamwork, but a lack of the right kind of space can inhibit it. Providing the right building blocks creates a place where a culture of teamwork can be developed: design of the right kind of space, staff training on how to use that space effectively, and management support of productive teamwork concepts.
Three key design strategies can help create this type of environment. One is to design spaces that enable face-to-face communication among staff without complete degowning or violating cleanroom standards. Another is to improve visibility within and into process areas to enhance safety, productivity, and marketing efforts. A third strategy pushes the design envelope even further, creating an open space plan that optimizes flexibility and teamwork with point-of-use isolator technology to control cross-contamination. Such a plan can liberate a production room and its personnel from as many environmental parameters as possible.
Face-to-Face Meeting Spaces
Consider the typical flow of people into a bioprocess or pharmaceutical manufacturing facility. Often there are separate entry points: one for production employees and contractors and the other for nonproduction employees and visitors. Each group must pass through a central checkpoint — with its reception desk, photo-ID and badging station, and often, uniformed security officers. To keep from impeding the flow of employees into a production facility, care must be taken at this point to separate them from visitors.
Production employees progress directly to a locker room, where they pick up their plant uniforms and begin the gowning process. A significant communication barrier occurs at the subsequent gowning portal, where a production employee puts on a gown and hair covering over the plant uniform and passes a step-over bench, adding shoe covers or changing to captured shoes. The gowning process is time-consuming, often taking 10 minutes or more, each time an employee enters or reenters the facility. So CGMP production employees must commit 10 minutes every time they want to use the restroom, eat lunch, meet with a nonproduction employee, or fill out a timesheet.
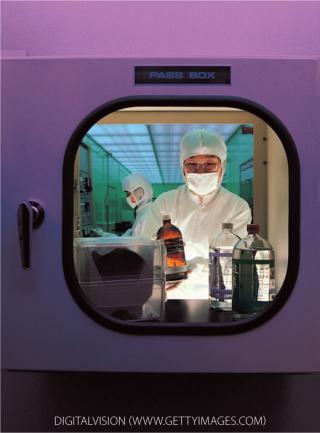
Imagine the barrier that time commitment creates to effective collaboration and teamwork. Surely issues arise every day that could be resolved with a simple five-minute face-to-face conversation. What if key production personnel could meet face-to-face in the production floor without needing to take the time to completely degown? What if nonproduction personnel could occasionally meet their production counterparts within their own territory, thus sharing the time commitment associated with gowning? This can be accomplished by creating a small meeting space within the larger cleanroom environment.
Facility designers may consider designing each production block with a “court” that could be accessed through the CGMP corridor (Figure 1). About 30 ft2 could contain CGMP clean space, a gowning area, and a non-CGMP space (Figure 2).
The first level of spaces within the court would meet a facility’s CGMP cleanroom standard. It might include a “huddle room,” where two production employees could meet in full gown and/or access a CGMP workstation (with no fabric or wood surfaces) to fill out a time sheet, write notes, or check e-mail.
To access the non-CGMP space, production employees would first enter a degowning area with a step-over bench. Here they would hang up their protective garments and put protective covers over their shoes. Then they could access a break room to relax and drink water as well as conference rooms where they could meet with nonproduction staff. Standard computer workstations would provide them with opportunities to analyze data or write reports. Such an area could not only reduce regowning times when production employees need to meet with one another or access a computer workstation, it also could improve communication between production staff and their office colleagues.
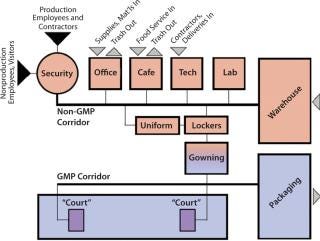
Figure 1: ()
Some companies don’t want to include this type of inexpensive “office” space within a valuable production environment. But how much value could be added to a bioprocess if employees could be more productive? The answer to that question is often dismissed because it is much easier to quantify the return on investment (ROI) for process technology than for people. If we buy a larger but more expensive bioreactor that can produce higher cell culture yields, the return is easy to measure. It is harder to quantify the results of investing in people. So how often do production needs grow just enough to require more space, but not enough to justify a large capital expenditure? The answer to that question may make investment in courts easier to understand. Strategically placed courts within a production environment could act as space “shock absorbers” when production demands increase. Over time, they could actually be repurposed, facilitating the incremental growth of production equipment, with new courts added during the next full capital expansion.
Transparent Production Processes
A second design strategy improves visibility within and into process areas to enhance safety, productivity, and marketing efforts. Typically, production lines are separated by solid walls to minimize the chance of cross contamination. Such designs limit sight lines both on the production floor and between it and the rest of a facility. Smaller compartments also tend to drive staffing decisions. Managers tend to put people in each individual space even when the process in that space doesn’t require staff.
It’s possible to create greater visibility, both for safety and marketing purposes, while simultaneously minimizing facility-imposed staffing barriers. These spaces can be visually opened up by using observation windows or creating an elevated area above the production suite that provides di
rect view of the production floor.
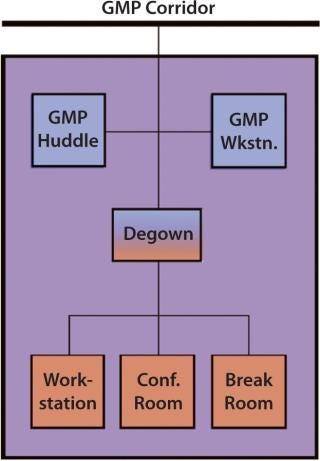
Figure 2: ()
Improving sight lines into and within a cleanroom also improves efficiency and decreases the risk of contamination by reducing the need to enter it for routine purposes (e.g., to find a certain staff member). This may also shorten response times during unexpected incidents. And it enables companies to offer tours to potential collaborators and/or clients without requiring them to go through the gowning process, exposing them to possible hazards, or disrupting activity on the production floor. More important, communication and teamwork can increase with a descreased need for contamination protocols.
Isolator Technology Approach
Production rooms and personnel can be completely liberated from many environmental parameters in an open space plan that optimizes processes using point-of-use isolator technology to control cross-contamination. A case in point is Coldstream Laboratories. A 20,000-ft2 sterile manufacturing facility is located on the company’s Coldstream Research Campus in Lexington, KY.
Its business model was developed for production of sterile parenteral clinical supplies and low-volume, high-potency niche commercial products. The plant uses isolator technology to control cross-contamination in a manner that could change how space supports biomanufacturing processes. The technology enables operators to handle sterile, potent, cytotoxic, and radiolabeled products in a contained box that functions both as a barrier to protect product streams from contamination and operators from exposure. As the industry moves toward low-volume, high-changeover products, this provides great opportunities for flexibility in a biomanufacturing environment. And liberating or minimizing the constraints of elaborate gowning protocols on people may both improve the quality of their work environment and allow more effective teamwork.
The system is a change from cellular production facilities in the past, and with change comes risk. Managers ask whether the potential benefits of better teamwork and increased flexibility are worth that risk. So don’t forget that product cross-contamination is significantly reduced with isolator technology.
Designing a building that enables production personnel to work efficiently and effectively with isolator technology is not a matter of simply providing large, column-free spaces. Effective design for such an approach — and for that matter, any type of process technology — first requires a thorough understanding of how people work within it. Only then can a designer create a space that enables the most productive working relationship among team members and their processing technology. Simply put, a successful outcome requires integration of people, process, and design
Light, Security, Productivity
Research by the Rocky Mountain Institute and the Lighting Research Center of Rensselaer Polytechnic Institute has shown that natural light contributes to human health, productivity, and safety while decreasing overall building energy usage (1, 2). Ideally, a bioprocess floor would include skylights or clerestory windows to bring natural light into a facility. A facility design must be responsive to issues of security as well as cleanroom and quality control (QC) standards. However, many industries for which security is paramount have successfully increased the penetration of natural light using such windows and/or skylights manufactured with security glazing such as polycarbonate or glass-clad polycarbonate.
For example, in a project for a highly secure research facility, our firm used a Kalwall Corp. system (www.kalwall.com) with insulated, diffuse, light-transmitting, structural composite sandwich panels to cover the windows. That made it possible to achieve a sound transmission class (STC) rating of 45, “faint to moderate.”
All design innovations require investment and have associated risks and benefits. Not every project can provide meeting spaces within a cleanroom environment, increase use of glazing into and on the process floor, or use windows/skylights to provide natural lighting. Point-of-use isolator technology pushes the envelope even further. Innovations are not without their costs and risks. But if we design our facilities only to meet cleanroom and QA/QC standards without considering the human factor, then we have missed opportunities to enable the people who are critical to their success to be as productive and effective as they can be. And as in any other industry, productive and effective people can provide a competitive edge in bioprocessing.
About the Author
Author Details
Lawrence DiGennaro, AIA, is the science market leader for BHDP Architecture, 302 West Third Street, Suite 500, Cincinnati, OH 45202; 1-513-527-0243; [email protected]. A member of the International Society for Pharmaceutical Engineering, he manages the planning, programming, and design of projects for both the public and private sectors, including academic and government institutions and pharmaceutical companies.
REFERENCES
1.) Romm, JJ, and WD. Browning Greening the Building and the Bottom Line.
2.) Figueiro, MG Daylight and Productivity: A Field Study.
3.) Galliher, P. 2008. Achieving High-Efficiency Production with Microbial Technology in a Single-Use Bioreactor Platform. BioProcess Int 6:60-65.
You May Also Like