June 4, 2020
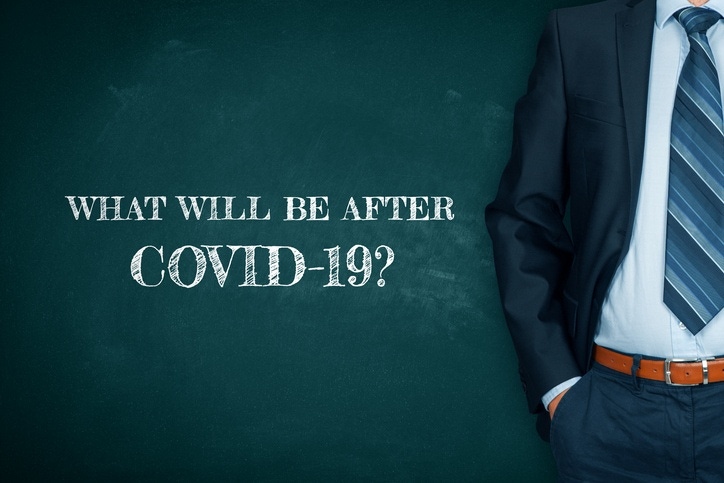
How pharmaceutical companies should plan to catch up after the pandemic and explain what happened to inspectors.
It is important to start planning for post-COVID-19 recovery even as the pandemic continues to impact pharmaceutical manufacturing operations, an expert panel told Food and Drug Law Institute members during a 19 May webinar.
Manufacturers should set priorities in advance so they can attack the most important backlogged activities first. They also should approach recovery with the right mindset: the need to act quickly will be too great to let anyone get bogged down in analysis paralysis.
Image: iStock/Jirsak
“The to-do list as companies come back up is really strikingly huge,” said Bob Rhoades, managing partner, Validant, who moderated the discussion.
Rhoades said the key question for operational managers and heads of quality is how to catch up with the list of crisis-related changes, particularly given that there might be less staff and, due to crisis spending, less money.
Understaffed and overwhelmed
Difficulties have arisen on several fronts as pharmaceutical companies struggle to maintain production during the pandemic, panelist Daniel Barreto told the Pink Sheet.
Unable to conduct onsite internal and supplier audits, companies are experimenting with remote alternatives that may not fully achieve their compliance objectives, he said. “Some activities will definitely be deficient, incomplete or inadequate in some cases.”
Some companies are operating below 50% capacity due to coronavirus-related absenteeism, Barreto said. In India, for example, no one is allowed to cross state lines during the current quarantine, not even essential workers who live in one state and work in another. Manufacturers will compete for outside experts to help make up the difference but, he said, “the amount of good resources is limited, so some companies will definitely suffer.”
This means that every day, more work is piling up, like annual product reviews, complaint investigations, manufacturing investigations, validations and even change control activities.
A post-coronavirus recovery plan would be a great help, but most companies have not considered developing one, and many would not know how to do it anyway, he told the Pink Sheet. “This is a significant problem that senior management needs to tackle now if they want to be successful.”
“Management oversight and control is essential here,” said Cathy Burgess, partner, Alston & Bird LLP.
Management must focus on getting facilities up and running in a way that is efficient, she explained. That means sending the right message to the organization on dealing with the uncertainty appropriately.
“Now is not the time to have a lot of deviations, a lot of investigation reports that are larded with irrelevant information.”
Plans should anticipate COVID-19-related demand spikes
Burgess gave the legal and regulatory case for why post-coronavirus recovery action plans are necessary.
For one thing, she said the recovery action plans should include the redundancy risk management plans for lifesaving drug products and drug substances that the 27 March CARES Act requires companies to develop.
Manufacturers should make sure they design the aspects of their recovery plans that are related to shortage-prevention redundancies in a way that satisfies related US Food and Drug Administration reporting obligations.
This includes preparing for the type of demand spikes that tend to follow publicity about existing drugs that might have efficacy against the coronavirus, as happened with chloroquine and hydroxychloroquine as well as famotidine and the investigational drug remdesivir, she noted.
A formal plan is needed
Companies should develop a formal post-coronavirus recovery and remediation action plan for restarting routine manufacturing operations, said Daniel Barreto, CEO, PharmQ Global Consulting.
The plan should have a risk-based rationale because, as Barreto explained, “you’re not going to be able to do things in a normal way and you’re going to have to prioritize. And you’re going to have to make a lot of decisions, and in many cases, you’re not going to have all the information that you usually have to make a decision.”
There will be a new focus on producing medically necessary drugs as customers and government authorities clamor for them due to the COVID-19-related demand surges.
Plant-wide buy-in required
The plan must win the endorsement of all of each site’s organizations and it must be enforced and audited, Barreto said.
It’s important to realize that it is not a quality plan, he stressed. “This is a plan that involves also a lot of production activities, where now you’re going to have to reassess how do you schedule your production work.”
For that reason, he said, it must involve not only the quality group, but also the production group and the engineering group: “Everybody has to be able to know exactly what is the role that they’re going to play.”
Risk management is key
Even though it’s not a quality plan, it should rely on quality risk management principles, he said. “You’re going to have to assess what sort of decisions you’re going to make based on a quality risk assessment approach.”
For example, he said a lot of change control activities will be backlogged. Instead of trying to do them all right away, managers will have to choose which ones to address first.
“You’re going to have to do that deep analysis that allows you to not only select which things to be done first, but the reason why this is more important than the things that you’re going to do later on.”
Additionally, workarounds may be needed for issues in the supply chain that may have arisen from the pandemic.
“You’re going to have to have a program whereby, on a biweekly basis, you and your team are going to meet and assess the extent to which you are sticking to the objectives of the plan.”
At some point, he noted, site inspections will resume, and plants will have to be prepared to show the rationale for the decisions they made as they came back from the crisis.
Putting a premium on productivity
Barreto hammered on the theme of productivity during the anticipated rush to resume more normal operations. “Sometimes we write extensive investigation reports unnecessarily. This is not the time about writing a lot. It’s a time about writing what you have to write in a very concise and precise way.”
He underscored the importance of making decisions without complete information during this period. When it comes to gathering the information needed for good decision making, he pleaded the audience to “please avoid an overkill approach.”
As for performance goals, just be realistic, he said. “Don’t overdo it. You’re not going to be able to do everything.”
Taking a new look at the supply chain
To develop the risk management plans the FDA expects for lifesaving drugs, companies will have to examine how they manage their inventories of raw materials and critical components, including active pharmaceutical ingredients, excipients and reagents, said Joseph Jimenez, managing director, Arches Consulting LLC.
As part of their examination of potential post-coronavirus supply chain issues, they will have to revisit the compliance history of their suppliers as well as the supply and quality agreements they reached with them.
Operationalizing priorities
Manufacturers also will have to take a new look at their portfolio in light of post-coronavirus priorities, focusing first on their lifesaving drug products and second on their other high-value products.
That means making sure everyone knows what the priorities are and how to apply them if, for example, a machine broke down or if there were a cluster outbreak among workers that limited the number of personnel available for night or weekend shifts.
Another issue is whether there is a team appropriately staffed to dust off dormant dossiers of medically necessary drug products and resume their manufacture to ward off shortages.
Pushback on redundancy
There is significant industry pushback to the idea of building domestic capability for critical materials, largely due to cost, Jimenez noted. However, the future supply chain could be reworked to qualify and regularly use multiple suppliers in different geographies.
“There should be a cost-effective model that companies could develop that would allow for the contingency or redundancy built into their supply chain,” he said.
However, each additional plant would come with its own tech transfer requirements, supply chain needs and staffing requirements that would have to be addressed.
Defining when conditional release could be OK
Change control procedures and related training will play a critical role in the process, Jimenez said. Strong post-coronavirus recovery action plans, or PC-RAPs as he calls them, would help ensure that the right questions are asked and answered for a manufacturing process change, and with the appropriate urgency.
The pandemic and the recovery from it “is going to put significant pressure on your front line management,” Jimenez said. These supervisors and team leaders “may find themselves with conflicts due to interruptions in schedule that may trigger the need to expedite steps.”
So for example, managers may be tempted to approve conditional release of drug products. “Most organizations do not permit conditional release. Perhaps that is something that should be considered and within the framework of a PC-RAP, you could define appropriately under what conditions or what controls would need to be in place to allow that to be a pressure release valve.”
A smoother return to stability
While standard operating procedures must be followed even if they cause conflicts, they could at least be simplified in a PC-RAP. Even though deviations will be difficult to avoid, companies will not want to have to explain any failures to comply, he said. “You do not want to find yourself in a post-facto rationalization exercise.”
No one wants to have to explain to an inspector how forced degradation studies from the stability program show that it was OK to leave product in bulk containers for too long, or how complex statistical analysis of laboratory results show that a release decision was justified, he said. “In the end, it will not change the fact that the GMPs were not followed.”
But all that waste of resources, time and energy could be avoided by simplifying processes up front, he said. A good risk-based plan can provide what Jimenez called “guidance for smooth execution to return to a stable state of operation.” There is another benefit as well, he said: “It will also improve your ability to absorb the unexpected.”
This article was first published on 26 May 2020 in The Pink Sheet.
About the Author
You May Also Like