Silicone rubber is widely used in the pharmaceutical industry, where sterilizability is an essential requirement for all fluid transfer equipment. Pharmaceutical products are sterilized frequently and repeatedly by high-level energy and/or chemical vapor to eliminate bacterial surface contamination. Such treatments may also affect the molecular structure of silicone rubbers, causing changes in their physical properties and performance. Several studies on this topic have been reported; until now, however, no systematic investigation has been performed on the effect of standard sterilization procedures on commonly used commercial silicone rubbers. Most investigations have focused on the treatment of unfilled silicone polymer under ideal radiation conditions, the results of which cannot be directly correlated with the effects of realistic sterilization conditions on commercial tubing, hose, and connection components. This report can serve as a material selection guide for process engineers working in pharmac...
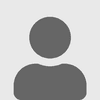
+3The materials used to fabricate single-use processing equipment for biopharmaceutical manufacturing are usually polymers, such as plastic or elastomers (rubber), rather than the traditional metal or glass. Polymers offer more versatility because they are light-weight, flexible, and much more durable than their traditional counterparts. Plastic and rubber are also disposable, so issues associated with cleaning and its validation can be avoided. Additives can also be incorporated into polymers to give them clarity rivaling that of glass or to add color that can be used to label or code various types of processing components.
Given all the positive attributes that polymers possess, there are also some negatives to consider when working with them in pharmaceutical applications. In the presence of heat, light, oxygen, and various external influences (such as sterilization), polymers can degrade over time if not properly stabilized. Degradation can manifest itself as cracking, discoloration, or surface blooming...
The Bio-Process Systems Alliance (BPSA) is an organization of equipment suppliers, service providers, and users in the biopharmaceutical industry whose shared mission is to facilitate implementation of single-use technologies in biomanufacturing processes. A key focus of BPSA’s core activities is to educate users and develop guides that help safeguard the quality of drugs and therapies produced with single-use process technologies.
As an extension of its technical guides and white papers, BPSA realized the importance of developing a white paper that provides a high-level understanding of single-use systems to an audience of manufacturing decision-makers within end-user organizations. For an overview of what is contained here, please see the “Implementation” box on the next page.
Section One: Perspectives on the “New” Pharma Market
Single-use systems (SUS) are gaining wide use and acceptance in the biotechnology and pharmaceutical markets. As our first publication to address the topic from this perspective...
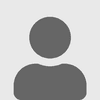
+8Today’s market demand for new drugs — combined with the difficult economic environment — is challenging bioprocessors to review their manufacturing systems and seek ways to make them more flexible, reliable, and cost effective. Increasingly, biomanufacturers are turning to single-use aseptic processing systems to meet or beat aggressive product-introduction timeframes while controlling costs.
Innovative new single-use technologies continue to be introduced, giving pharmaceutical companies greater flexibility for replacing traditional stainless tubing, equipment, and even entire process suites with plastics-based solutions. The benefits of converting to presterilized, single-use systems have been documented in many articles and case studies, but many of those benefits would be lost if manufacturers could not safely and securely connect systems and components to create a complete aseptic process.
Connecting devices and methods may appear to be a small part of these overall systems. But connection and discon...
Single-use technologies are coming of age and joining other driving forces to reshape the landscape of biopharmaceutical industry. This innovation has created new platforms for bioprocessing, offering competitive advantages and tremendous opportunities to current biomanufacturers. Moreover, the increasing acceptance of disposable systems with proven success will help enable niche products and bring emergent players to the market.
The Age of Stainless Steel
The discovery of DNA structure in the middle of the 20th century led to numerous breakthroughs in biological science and inspired a generation of entrepreneurs. The 1980s and 1990s saw a booming biotech industry with all eyes on bringing biologic products to market. As with small-molecule drugs, biologic development faces challenges in long development cycles, low success rates, and high costs. According to Tufts, it was estimated to take about $1.2 billion to commercialize a single biologic drug in 2008 (
1
).
Several additional barriers of entry are u...
A recent private grant of US$10 billion for human vaccine applications illustrates the revival of interest in vaccine science (
1
). The 2009 response by vaccine manufacturers to the H1N1 pandemic revealed the convergence of three technological developments. First is a revolution in technology: Vaccines are being developed for diverse and unprecedented applications through a number of entirely new approaches. Second is the recent adoption of cultured cell-based production for a growing number of vaccines, such as influenza. And third is the rapid acceptance of single-use technology in bioproduction overall.
The Revolution in Vaccine Technology
Because of remarkable technological innovations in both prophylactic and therapeutic vaccine science, it’s important to establish the exact scope of this topic. From novel and unique vaccine types (e.g., DNA plasmid vaccines) to their unprecedented indications (such as cancer and diabetes treatment) to innovative means of delivery (e.g., inhaled nanoparticles) to en...