An Integrated Filtration System for Harvest of Small-Scale BioreactorsAn Integrated Filtration System for Harvest of Small-Scale Bioreactors
August 1, 2013
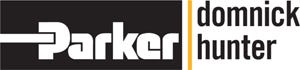
Parker domnick hunter’s HarvestClear™ Filtration System is a complete, out-of-the-box filtration system that provides automated clarification of small-scale bioreactor outputs while maximizing filtration performance. The HarvestClear™ System allows for walk-away cell-culture harvest, reducing hands-on time and increasing operator safety without filter blockage.
Summary
The clarification of batch and fed-batch bioreactor systems can pose a practical challenge to biopharmaceutical manufacturers because of high cell densities in cell culture process streams. The HarvestClear™ Filtration System provides an easy solution for clarifying 1–20 L of high-density fermentation batches of Chinese hamster ovary (CHO) cells.
Introduction
When correctly sized and controlled, single-use normal-flow filtration (NFF) systems can provide biopharmaceutical manufacturers with high-quality, fast, and cost-effective clarification of discovery and development-scale bioreactors. This offers an alternative to traditional time-consuming and sometimes messy techniques such as centrifugation or coarse filtration.
Plug-and-play functionality of filtration systems enables them to be immediately usable without the requirement for any preflushing, sterilization, or assembly — which saves set-up time.
Filtration has been a traditional expertise of Parker domnick hunter Process Filtration, a division of Parker Hannifin, the world’s leading diversified manufacturer of motion and control technologies and systems, providing precision-engineered solutions for a wide variety of markets. With the acquisition of SciLog in August 2012, Parker domnick hunter Process Filtration and SciLog Inc became a single global biopharmaceutical solutions provider. The new entity is committed to deliver single-use solutions that shorten product development times and improve bioprocessing productivity.
The HarvestClear™ System combines the filtration expertise of Parker domnick hunter with the single-use sensor and automation technologies of SciLog. This system is the first to be launched in a series of integrated single-use solutions for critical applications in biopharmaceutical manufacturing that promise to simplify bioprocessing, increase efficiency and safety, and guarantee reproducible product quality.
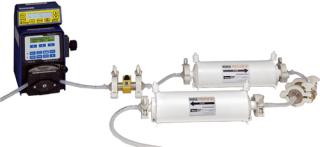
Filter Product Descriptions
PROCLEAR GF
Pharmaceutical-grade, glass-fiber depth media prefiltration product
Designed to provide exceptionally high dirt-holding capacity and low extractable levels, making it well suited to biopharmaceutical applications
PROPOR HC
Pharmaceutical sterilizing-grade, high-capacity polyethersulphone membrane filter
Designed to provide assurance of sterile filtrate without compromising on filtration system capacity.
The HarvestClear™ System combines automated normal-flow filtration with plug-and-play functionality for minimal investment in time and maximum filtration productivity.
HarvestClear™ System Description
The HarvestClear™ Filtration System uses SciLog automated pumping and single-use sensor technology to automate normal-flow filtration through a Parker domnick hunter 5-µm PROCLEAR GF prefilter and a 0.2-µm PROPOR HC high-capacity sterilizing-grade filter. The “Filter Product Descriptions“ box describes these filters.
The sterile filtration manifold (containing SciPres® precalibrated pressure sensors upstream to the filters) is controlled by a FilterTec™ controller connected to a SciPres monitor. Figure 1 shows the full system connected to a bioreactor and a bioprocessing container to collect the filtrate. When the container is mounted on a WeighPro™ connected to the FilterTec™ controller, the system also offers gravimetric control (Figure 2).
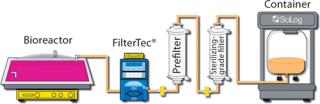
Figure 1: ()
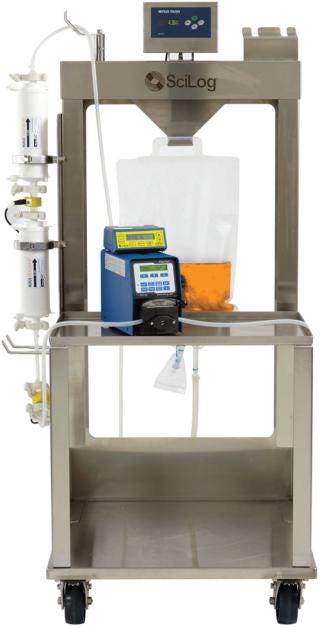
Figure 2: ()
The system incorporates a patented R/P Stat method, an innovation that delivers significant improvements in filter life expectancy. Using the R/P Stat method and the feedback from the inline sensors, as a membrane begins to foul the system dynamically adjusts the flow rate to allow up to 35% more filter throughput. This is accomplished by selecting three simple process variables including initial flow rate, maximum inlet pressure, and minimum flow rate. This is shown graphically in Figure 3.
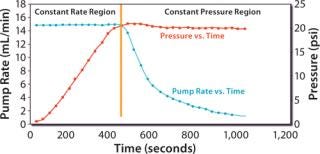
Figure 3: ()
Filter Sizing for the HarvestClear™ System
Trials of the HarvestClear™ System were performed in
conjunction with a large biopharmaceutical manufacturer on the output stream from single-use bioreactors used to grow CHO cells for research purposes. The typical viable cell concentration of the bioreactor output used for testing was 7 × 107 cells/mL. The key system performance criteria were speed of processing and ensuring that filter blockage did not occur in the middle of the batch.
Subsequent scale-up testing conducted using large-scale, single-use MURUS capsules provided confirmation of the initial results and helped establish approximate sizing guidelines for the three standard filter manifolds (Table 1).
Table 1:
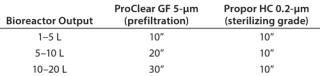
Table 1: 194; ()
Conclusion
The HarvestClear™ Filtration System provides plug-and-play functionality for clarifying the outputs from small-scale bioreactors, allowing immediate use without the need for initial flushing. The system’s sterile, preflushed, presized manifolds save time and effort.
The automation in the FilterTec™ controller, coupled with feedback from in-line SciPres pressure sensors, allows walk-away bioprocessing with reduced risk of product loss as well as an increase in product yield and operator safety.
About the Author
Author Details
Gregg Larson is single-use product manager at Parker domnick hunter Process Filtration; 1-608-824-0500; [email protected]; www.parker.com/processfiltration.
You May Also Like