Turn-Key Bioreactor Solutions July 2010Turn-Key Bioreactor Solutions July 2010
July 1, 2010
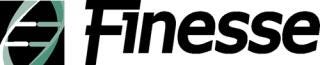
top) and TruBio µC (bottom ()
In order to reduce scale-up costs and facility capital expenses, biotechnology companies are adopting single-use systems. To fully enable the single-use paradigm, automation software, hardware, and single-use sensors must be optimized; moreover, both validation documents and materials certifications must be readily available for cGMP implementations.
Finesse provides turn-key, configure-to-order measurement and automation solutions for many single-use bioreactor types: “stirred-tank,” “paddle,” or “rocker” systems. The Finesse turn-key system is optimized for each bioreactor type to maximize product yields. Finesse systems are scalable from R&D to process development to cGMP manufacturing. Finesse also provides full support for its systems, including installation, training, validation packages (FAT, SAT, IQ/OQ), and service/maintenance programs.
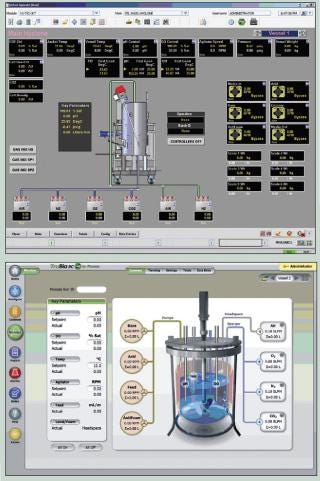
Figure 1: top) and TruBio µC (bottom ()
The primary enablers of single-use systems, however, are the sensors. Finesse offers disposable sensors for dissolved oxygen (TruFluor DO), pH (TruFluor pH), temperature (included in both TruFluor DO and pH), and headspace pressure (TruTorr),which are pre-inserted into and gamma irradiated with the single-use bioreactor bag, so that the entire system arrives sterile and port leakage is minimized. Finesse sensors have embedded, gamma-radiation–resistant “smart chips” that contain the relevant calibration parameters and minimize operator time during process setup. The disposable sensor performance meets or exceeds that of electrochemical sensors in noise and time response without sacrificing reliability or precision. The unique, patented sensor design eliminates the long-term drift issues observed with competing fiber-optic–based fluorometric systems.
Automation hardware systems used with single-use bioreactors must be flexible, in order to adapt to the different processes that can be run in a multiproduct facility. The Finesse hardware product family is user-friendly and plug–and–play with a wide variety of external equipment, such as pumps, scales, and off-line analyzers. Finesse equipment has a modular design, allowing fast and easy reconfiguration of the bioreactor train for different bioreactor sizes and types, as well as different processes or cell lines.
Our automation software allows rapid scalability of a process through advanced process models and smart algorithms, as well as ease of data collection and analysis. Finesse TruBio DV software has been developed with GAMP4 methods and validated for cGMP applications. TruBio DV software allows easy process reconfiguration through drop-down menus without DeltaV programming and allows the user to save and load process recipes for accelerated process scale–up or transfer.
TruBio µC software is based on the Wintel (Microsoft Windows operating systems/Intel microprocessors) platform, uses the latest in embedded processors (similar to those used in military systems, automated teller machines, and medical devices), and leverages off of the economics that drive the consumer electronics market. TruBio µC has been designed to free bioprocessing professionals or their operators from many of the mundane tasks that defocus them (slowing their progress toward completing their runs), and it minimizes situations by which a batch is not usable.
As more companies involved in bioprocessing realize that they can scale their ideas into clinical production, these turn-key system will become ubiquitous. Finesse’s mission is to serve this new market paradigm with complete, configure–to–order single-use bioreactor systems.
About the Author
Author Details
Barbara Paldus, PhD, is chief executive officer ([email protected]; 1-800-598-9515) of Finesse Solutions, 71 Daggett Drive, San Jose, CA 95134; http://finesse.com.
You May Also Like