LEWA developed its first pulseless pump for liquid chromatography in the late 1970s and delivered its first chromatography system in the early 1980s. LEWA is the leader in supplying pumps used for pilot and industrial HPlC, SMB, and lPlC chromatography worldwide.
A customer came to us several years ago requesting a lowpressure liquid chromatography system with a flow range of 20 − 2,200 L/h. They also wanted the ability to achieve linear gradient from 1 to 99%. We designed and built the system, and it is now in a validated process. This was a very challenging task. Upon completion, this question was asked: “is there a better way?” The intellidrive technology is the answer. LEWA has now integrated this technology into chromatography skids.
The LEWA EcoPrime brings wide dynamic flow range, low-pulsation flow, and accuracy to modern chromatography as unique features. We have combined state-of-the-art functionalities into one unit: it can be a buffer dilution skid, or directly connected to a column to be a ch...
A subsidiary of the M + W Group, M+W Process Industries GmbH is a leading global engineering and construction company offering complete process and facilities solutions from design to construction.
M+W Process Industries has the experience and the know-how for design and execution of all types of biotechnology and pharmaceutical production systems. The portfolio includes research plants as well as industrial facilities, monoproduct and multiproduct plants, variable single-use systems, and large-volume stainless-steel production units.
The needs and requirements of our customers are key priorities. Experienced project managers offer customized and cost-effective, single-source solutions by integrated project teams. High international standards for safety and product quality are required for biopharmaceutical plants in particular. Our work is therefore based on current EU GMP and FDA guidelines as well as other international standards. Complete qualification and validation services will verify your project ...
Continously new bioprocesses are evolving, and bioprocessors are searching for the easiest way to process samples in R&D. Currently, a huge trend towards disposable production systems is notable. For these purposes plastic bags, stirred-tank reactors, and storage tanks established on the market. Unfortunately, these reactor types are not suitable to perform sophisticated bioprocess development. In bioprocess R&D, throughputs of 50 to 1,000 fermentations are needed. Therefore, m2p-labs developed intelligent new tools at microscale to fulfill the needs in bioprocess development. The combination of high-throughput experimentation, online monitoring, scalability, and automation made it possible to provide unique and very efficient bioprocessing tools at microscale. Our mission is to bring bioprocesses as fast as possible from microreactor to process — m2p.
BioLector® Technology
The Biolector is a unique high-throughput fermentation system. In 48 parallel cultures, the most important fermentation parameters su...
With a renewed acceptance of perfusion processesin cell in culture, both in the laboratory and for production applications (
1
), New Brunswick packed-bed bioreactors using Fibra-Cel® disks are seeing an upsurge in interest. This article examines Fibra-Cel technology and its many advantages, from increased yields of secreted proteins to labor savings in applications ranging from rabies vaccine production to production of the first licensed gene therapy drug.
What Is Fibra-Cel?
Fibra-Cel from New Brunswick Scientific (Edison, NJ) is a solidsupport growth matrix (Figure 1) for anchorage-dependent and suspension cell cultures. It is used predominantly in perfusion processes for the production of secreted products — such as recombinant proteins and viruses — and it is currently being evaluated for stem cell research (
2
).
Figure 1: ()
Since the 1980s, scientists around the globe have been using Fibra-Cel to grow a wide range of cell types (see box, right), including hybridomas and insect cultures. Originally...
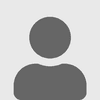
+1Advances in sensor materials and optoelectronics have enabled new optical sensors for use in biotechnology, food and beverage processing, and more. These fiber optic chemical sensors work by trapping an oxygen-sensitive fluorophore or pH indicator dye in a sol-gel host matrix that is applied to an adhesive patch, the tip of a fiber, or a flat substrate such as a cuvette. The indicator materials change optical properties in response to analytes in their environment, and electronics measure the response. For oxygen, the NeoFox Phase fluorometer measures the partial pressure of dissolved or gaseous oxygen. For pH, a spectrometer measures the colorimetric response of the pH dye.
Experimental Conditions
We placed oxygen-and pH-sensitive patches inside a bioflask in which red grape biofermentation occurred. Bioreactors are closed-environment systems in which cells are cultured under specific conditions to synthesize a final product.
RedEye® oxygen patches were attached to the container with adhesive backing to ...
Fed-batch protein production processes have become more favored because of their simplicity under large-scale conditions. PAA laboratories′ ActiCHO media system is an industrial media package for the cultivation of Chinese Hamster Ovary (CHO) cells in large-scale applications. It contains all media needed from cell thaw until harvest in large scale, which are a stock culture and cell-expansion medium, a production medium, and two appropriate feed media. The formulation of each single medium is titrated carefully to complement the other.
Features of ActiCHO
All parts of the ActiCHO media system are free of animal-component–derived substances. The media are available free of growth factors and peptides. This reduces the complexity of the media and reduces the number of critical components in each formulation. All media are also free of peptones, which is an important feature for reproducibility of production runs under large-scale conditions because peptones are known to have lot-to-lot variability. The Act...
In many biopharmaceutical companies, chromatographic purification in downstream processing is a key focus for optimization studies. The objective is to streamline the process, which may be achieved by the elimination of intermediate unit operations. The main question, therefore, is how to optimize the adjustment of individual chromatographic process steps.
Currently there is a broad range of next-generation sorbents and membranes available for process chromatography. These new chromatography media are characterized by significantly improved performance compared to their classical predecessors: e.g., higher dynamic binding capacities, higher operational flow rates, and specific and distinctive retention mechanisms. Nevertheless, traditional media (based on agarose or polymers) continue to be routinely used for new method development due to their proven suitability for protein purification in FDA- or EMA-approved applications. In these cases, the potential of modern ion exchangers and novel mixed-mode or mu...
Oligonucleotides are entering clinical trials in increasing numbers. In many ways, their entry into the clinic mirrors the development of protein therapeutics in the late 1980s and early 1990s. On the other hand, the purification process for an oligonucleotide therapeutic is very different from that for a protein. Typically one high-resolution, high-load step is used rather than a train of capture, intermediate purification, and polishing columns.
TSKgel SuperQ-5PW (20) resin — a 20-µm particle size anion-exchange medium — is becoming the “go-to” product for oligonucleotide purification. This article demonstrates the performance of the resin at higher loads while maintaining the resolution and purity of a target molecule.
Oligonucleotides are short, linear sequences of deoxyribonucleic acid or ribonucleic acid that are generally manufactured by chemical synthesis. Due to the unique structure of these molecules and the way they are synthesized, oligonucleotides require special considerations during chromat...
PBS Biotech® makes the industry’s most advanced single-use bioreactors. With low-profile, easy to use, and plug and play designs, these systems range from 3 liters to 2,500 liters permitting fully scalable bioprocess solutions from benchtop to production.
At PBS Biotech we provide bioprocess solutions. We work with each customer to develop a tailored, single-use bioreactor plan that delivers optimal value in your bioprocess and provides competitive advantage and value that is developed, applied, and measured. We realize investments in capital equipment and recurring costs are complex and critical to your company. The PBS team helps customers migrate from legacy systems and equipment to a sustainable, cost-effective, single-use solution for cell culture development. We are bioreactor experts and know how to make them efficient, cost-effective, reliable, and powerful tools in your bioprocess.
PBS 3 benchtop bioreactor: Compact and fully scalable from 3 L to 2,500 L, PBS bioreactors are an ideal solution fro...
The
Pf
ēnex Expression Technology™ platform is a powerful protein Expression Technology based on the novel host
Pseudomonas fluorescens.
Legacy recombinant protein expression hosts such as
E. coli
and yeast tend to have high failure rates with regard to expression of soluble, active protein. In addition, the time required to identify the optimal expression strain in these systems is protracted, resulting in significant opportunity cost for drug developers. Leveraging the
Pf
ēnex Expression Technology™ shortens development time via higher success rates and lowers overall cost of goods associated with rapid process cycle times, high cell densities, and low-cost media.
Overview
: Tables 1 and 2 are based on a case study presented by Georg Klima, head of microbial process science at Boehringer Ingelheim. It outlines the expression of a Fab fragment through four different approaches including
E. coli
(periplasmic),
E. coli
(inclusion body),
Pichia pastoris,
and
Pseudomonas fluorescens
(
Pf
ēnex E...
Over the past decade, the cell therapy field has matured into the next generation of medical technology. In both the United States and the European Union, physicians now have an option to write prescriptions for manufactured engineered cell therapeutics, as they routinely do for prescription medications. And the number of available commercial cell therapies is expected to grow. However, unlike traditional pharmaceuticals, engineered cell therapeutics require geographically dispersed networks of cell collection, engineering, manufacture, distribution logistics, and treatment facilities, thus presenting a yet unseen set of challenges for those involved in cell therapy development and commercialization. Development teams must design and support clinical trials; optimize economics, manufacturing capacities, and distribution logistics; manage evolving regulatory framework; and work to develop and strengthen the IP claims vital to future commercial success. From the early stages, cell therapy must be developed ...
Rentschler Biotechnologie GmbH is a full-service contract manufacturer with over 35 years of experience in the development, production, and approval of biopharmaceuticals in compliance with international GMP standards with a highly skilled staff of 650. As part of the Rentschler Group and headquartered in Laupheim, Germany, Rentschler is one of three leading European CMOs operating globally. Dedicated to delivering high-quality biopharmaceuticals produced in mammalian cell culture, Rentschler has nine stand-alone GMP suites with volumes of 30 L, 250 L, 500 L, 1,000 L, and 2,500 L, which allows producing material for clinical trials and supplying the market. Rentschler Biotechnologie is a pioneer in the development and production of biopharmaceuticals — it was the first company in the world to gain market authorization for an interferon-containing drug.
Rentschler Excels with Expertise and Full Service from “Gene to Drug Product”
Rentschler provides customized, integrated biopharmaceutical services: from t...
Repligen™ OPUS (open Platform User Specified) prepacked columns packed with CaptivA™ PriMab™ Protein A resin offer high performance and all the advantages of single-use technology (reduced validation effort, reduced risk, faster time-to market). What makes this solution truly unique, however, is that oPUS prepacked columns provide lower total cost of ownership in many applications compared with conventional stainless steel or glass columns.
Single-Use Chromatography Study
BioPharm Services ltd (Chesham, UK) conducted a study to assess the impact on total cost of ownership of using low-cost, high-performance Protein a resin in prepacked, disposable columns. the conclusions reveal that for applications in which the bioreactor is 1,000 L or smaller and the number of batches does not exceed 20, the use of oPUS columns prepacked with Captiva PriMab resin can result in savings up to 15% as compared with conventional columns packed with more commonly used resins.
Figure 1 compares the cost of goods per gram for ...
Sandoz is one of the leading specialists in biotech development and manufacturing. Comprehensive know-how is based on more than wo decades in microbial and mammalian cell culture production at commercial scale. Today Sandoz offer a broad variety of integrated services including innovative expression systems, process development, scale-up, and production of recombinant products derived from microbial systems and mammalian cell culture in state-of-the-art facilities.
Our expertise is based on numerous projects successfully erformed in collaboration with our customers. Currently, Sandoz is manufacturing more than 25 different recombinant products for well-known pharmaceutical and biotechnology companies located in USA, Europe, and Japan. our FDA approved facilities fulfill worldwide quality requirements.
Services Offfered
Production of Recombinant Peptides and Proteins:
150-L, 1,300-L, 3,000-L, 13,000- L, and 40,000-L fermentors are available in our facility in Kundl, austria. each fermentation unit is ful...
Filters rated at 0.1 µm have been increasingly used for cell culture media filtration due to concerns about mycoplasma contamination of cell cultures. Sartorius Stedim Biotech has recently launched a new 0.1-µm, mycoplasma-retentive, sterilizing grade filter: Sartopore® 2 XLM. it is a heterogeneous, double-layer PES membrane filter with a highly asymmetric 0.2-µm prefilter layer in-built with the same 0.1 µm mycoplasma-retentive final membrane as its predecessor, Sartopore® 2 0.2/0.1. Sartopore® 2 0.1-µm. 10″ cartridges have been validated as mycoplasma-retentive by testing at a third-party laboratory using a modified AStM F838-05 method to show removal of
Acholeplasma Iaidlawii
at LRV = 7/cm
2
.
We have tested Sartopore® 2 XLM filters extensively in different media applications. Two examples of its excellent performance are presented here. one is for serum-free media specifically developed for adherent cell lines used in vaccine production (e.g., Ex-CELL Ebx GRO-I from SAFC), and the other is for a ful...
The development of insect cell culture production systems has produced opportunities for the expression of recombinant proteins for research and therapeutic applications in a non–mammalian cell culture environment. Various insect cell lines have been developed for the baculovirus expression vector system (BEVS). Development of stable transfected
Drosophila
and lepidopteran cell lines has offered a nonlytic culture for the production of recombinant proteins from insect cells.
Spodoptera frugiperda
Sf9 cells have been successfully adapted to suspension culture and have become an attractive platform for industrial-scale cell culture, lending them for use in stirred-tank bioreactors, including single-use bioreactors (S.U.B.s). S.U.B. vessels reduce capital costs, cleaning, maintenance, and installation and validation time in comparison with traditional, stainless-steel vessels. The Thermo Scientific HyClone S.U.B. can be used to culture cells at scales of 25 to 2,000 Lin working volume. Such bioreactors us...
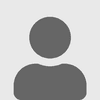
+1Vetter, a leading provider of aseptically prefilled drug-delivery systems, launched a new state-of-the-art facility at the Illinois Science + Technology Park in suburban Chicago. The site offers a central US location with a domestic and international airline hub. Moreover, it is uniquely situated in a thriving biopharmaceutical region that offers an established infrastructure, prominent research institutions, and a talent pool of 70,000–80,000 professionals.
An expansion of Vetter Development Service, the Chicago site supports preclinical through phase IIdevelopment projects. The 24,000-ft
2
facility’s functional areas include microbiology and chemical analysis laboratories; materials preparation; compounding; aseptic CGMP filling for vials, syringes, and cartridges; quality assurance; and seamless transfer to Vetter Commercial Manufacturing.
Early Phase Work
Developed at the urging of Vetter’s North American clients, the Chicago site supports small-batch, early stage products. Vetter has extensive exper...
Since 2006, Vivalis has operated and maintained a GMP manufacturing facility for the production of monoclonal antibodies, recombinant proteins, and viral-based products. Founded in 1999, Vivalis has developed a series of innovative technologies to address the needs of biopharmaceutical development. These include novel cell substrates, such as our avian EB66® cell line, which has seen wide application in areas from vaccine manufacturing to monoclonal antibody development. Our CMO services not only include those for clients using the EB66® cell line, but also other mammalian cell platforms, such as CHO and HEK-293. As a CMO, we remain platform neutral.
Antibody Production Services
The development of single-cell clones, either in CHO or Vivalis’s EB66® cell line, is performed by our scientists located in either our Saint-Herblain or Lyon facilities. These activities are performed under GLP so Vivalis can move a clone into advanced development to ready it for GMP production. Services offered in this area inc...
Wacker Biotech is a dedicated contract manufacturer of biopharmaceuticals with more than 20 years of experience in microbial systems. We offer proprietary technologies (ESETEC®, DENSETEC®) that significantly lower the cost of goods. Our customers benefit from a comprehensive service for the development of robust and highly efficient processes and GMP-compliant manufacturing for clinical trials and commercial supply. We opened recently a new process-development unit to optimize the entire process-development chain, from gene to purified protein. Asecond extension at the Jena site came on full stream in March 2010 after a multimillion investment. We doubled the production area in the existing GMP plant and added a brand new downstream processing suite.
Services
We work in close collaboration with our customers. Projects are managed by dedicated project managers supported by cross-departmental teams. Depending on our customers’ requirements, we have the flexibility to perform the whole process, or transfer ...
For many developers of new biologics, outsourcing clinical or commercial manufacturing with a contract manufacturing organization (CMO) makes good sense. Dozens of capable CMOs offer ready capacity to companies who can’t afford the time, capital or risk involved in building their own biomanufacturing capacity.
Of course, the convenience of instant access to a CMO’s infrastructure comes at a steep price: Many CMOs use proprietary cell lines, media, and other technology that will limit a drug developer’s options in the future. Process development work done by a CMO may create barriers to future technology transfer, effectively marrying drug developers to that CMO indefinitely. This creates a structural disadvantage, resulting in economics that may limit the future value of a drug to its developer.
How to Add Long-Term Control to the Speed and Economics of Outsourcing:
The FlexFactory® biomanufacturing platform from Xcellerex provides a new level of flexibility to biomanufacturing structure and deployment. ...
Xcellerex’s XDRbioreactors are well suited for production processes that require the use of anchorage-dependent cell lines grown on microcarriers. The bioreactor agitation assembly is the driver for these factors. To assure robust bioreactor operation, the M40Eimpeller was designed to perform well above the minimal mixing constraint for uniform gas distribution and fluid homogeneity and well below the maximum shear constraint to assure a viable and productive cell population.
Cell lines such as Vero, MDCK, and MRC-5 are commonly used in production of vaccines or other therapeutic products. These cell lines are anchorage dependent, and they will undergo apoptosis if grown in suspension culture. Mass production of anchorage-dependent cell lines can be accomplished in Tflasks or roller bottles, and the production process can be automated by the use of robotics. However, these methods are laborious and can be prohibitively expensive. Microcarriers are the most common alternative for mass production of anchora...
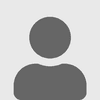
+5Richter-Helm BioTec is a dynamic and expanding biotechnology company located in Hamburg, Germany. Being one of the first biopharmaceutical enterprises in Europe, Richter-Helm has more than 20 years of experience in the development and GMP-compliant production of recombinant proteins, plasmid DNA, and microbial vaccines. With more than 120 employees Richter-Helm offers customized state-of-the-art solutions for all steps in biopharmaceutical projects through contract development and manufacturing services in GMP facilities for microbial production (fermentation scale up to 1,500 L). Beside our strong expertise in
Escherichia coli,
Richter-Helm successfully produces proteins in yeast (e.g.,
Pichia pastoris
). Thus Richter-Helm is the ideal partner for biopharmaceuticals development by offering material from preclinical and clinical trials to market supply at a large scale. In addition Richter-Helm is the platform of Gedeon-Richter and Helm AG for worldwide licensing options as well as partnerships for cod...
The following is an extract from a paper presented at the Orlando ISPE Annual Meeting on November 2010 by Dr. John Toynbee.
Seal or gasket material protruding into the process flow within pipework carries a number of production issues, many of which have serious cost implications.
Areas of seal intrusion or recess are caused by oversized or undertightened gaskets that create a trap at the clamp union. This creates a number of production problems:
The following chart, compiled from James Walker test data on 1-inch clamp gaskets, demonstrates rates of seal intrusion plotted against clamping force for James Walker Elast-O-Pure EP75 and the three closest competitor materials.
The traces clearly show that only Elast-O-Pure meets ASME Category 2 (± 0.2 mm) for intrusion performance on installation at the ASME recommended clamping force of 3.3 Nm/30 in.lb.
Figure 1: ()
As the clamp is tightened, three of the materials soon reach intrusion levels in excess of a millimeter, while Elast-O-Pure remains within Catego...
The risk of viral contamination is a feature common to all biotechnology products produced by processes that use cell lines and raw materials of animal origin. Such contamination could have serious clinical consequences, and worldwide regulatory bodies expect that the viral safety of these products be ensured.
Viral clearance studies are performed as one way of demonstrating viral safety. The studies are executed by intentionally adding or “spiking” large amounts of virus into the starting material for individual manufacturing steps and assessing the capacity of those steps to eliminate infectious virus from the product stream.
Spiking virus preparations are considered to be critical reagents in viral clearance studies. The Parenteral Drug Association recently issued
Technical Report 47: Preparation of Virus Spikes Used for Viral Clearance Studies.
The technical report emphasizes that the production of virus stocks must be well controlled and that the resulting stocks should be tested for identity, stre...
Disposable cell culture bags are used in conjunction with rocker platforms in an array of cultivation applications (insect and mammalian cell lines, virus, protein expression). Rocking platforms provide the dynamic motion and oxygen transfer for cell culture environments. Disposable culture bags are designed to allow for a large air-liquid surface for oxygen transfer, easy access for sampling/filling, and a sterile environment. Venting issues have been reported in the field during rocking of disposable cell culture bags. Therefore, venting and cell growth testing were performed for optimized Charter Medical Clear-Pak® cell culture bags.
Product Optimization
An optimal cell culture design was prototyped with modifications. These changes were chosen to address venting in the cell culture bag and incorporated into standard Charter Clear-Pak® 10-L cell culture bags (5-L working volume). Bags were gamma irradiated.
Venting Experiment
A venting study was first executed to gage suitability of the modifications...