Not long ago I assembled a few current and former coworkers to meet with a young woman who is contemplating a career in journalism. Part of that visit involved comparing experiences of those who had been in the field for many years with those who had finished their formal education only a few years ago. We wondered whether the field still welcomes newcomers with degrees other than in journalism; or whether publishers now insist on that specific academic background — becoming more selective because a shrinking market allows them to.
At that same time, I was also following a similar thread in the MyBIO group on LinkedIn (
www.linkedin.com
): What levels of education are advised these days for launching a career in biotech? Topics include the pros and cons of combining an MBA with a BS (or MS), the importance of having multiple years of lab experience on your resume, and the importance of networking (but not in all national cultures). They recommend a number of academic programs that combine business with sc...
Even before the advent of biosimilar products, biopharmaceutical products faced life-cycle concerns. The discovery–development–licensure process is just the beginning. Drug sponsors hope each new product will enjoy decades of relevance and generate millions of dollars in sales. But “me-too” products will come along, process technologies will change, and patents will expire.
Even product innovators have to think about comparablity. Out-of specification results can signal problems that have their roots in raw material choices and sources, equipment deviations, analytical method limitations, or training and standard operating procedures. Regulatory authorities expect to see appropriate corrective and preventive measures taken. And if process changes become necessary, they must be reported in compliance with the rules. Risk management is importantwhen it comes to making product and process-related decisions over time. And quality by design (QbD) approaches to process development, validation, and integration w...
Now in its 11th year, IBC’s Formulation Strategies for Protein Therapeutics is a must-attend annual conference for formulation, delivery, and analytical development scientists from biotherapeutic development organizations around the world. The 28 case studies to be presented at this year’s conference were chosen to offer solutions to the most pressing day-to-day challenges in formulation development for therapeutic proteins. Additional presentations address cutting-edge protein science from leading academics and include briefings on strategic issues of importance to this important field:
Formulation Strategies is colocated with the BioProcess International Conference and Exhibition. This provides the opportunity to visit with more than 150 suppliers of bioprocess technology and services and network with over 1,500 industry leaders.
These topics are
new this year
:
Conference Sessions
Keynotes
“Understanding How Solution Conditions Affect Stability by Investigating Site-Specific Changes within Proteins,”
Continuing the theme of this occasional series, we examine the role of manufacturing in the supply chain in terms of what is required to deliver affordable medicines to patients. The industry has debated the relevance of manufacturing costs in the overall big picture (
1
). Rising manufacturing costs as a proportion of the overall selling price coupled with increased competitive pressures creates a strong drive to reduce manufacturing costs. However, cost of goods (CoG) is not the only strategic driver. Other important factors associated with bulk manufacturing are
Inability to tackle some of those factors has caused significant problems for the biopharmaceutical industry during the past decade. A combination of capital intensity, uncertainty regarding product success, and long lead times required to build a large-scale facility has resulted in redundant capacity (
2
). Much capacity is no longer needed, and it is often not economically viable to change its use. The urgent challenge facing our industry is...
Progress in the development of bioprocessing-related assays and analytical instrumentation has not kept up with industry demands. The industry wants analytical technologies (especially for single use) to help improve productivity, optimize and monitor processes, provide real-time product quality control, and characterize biosimilars. These trends are reflected in our recent survey data.
Over 30% of biopharmaceutical manufacturers and contract manufacturing organizations (CMOs) have expressed demands for improved assays and analytical equipment (
1
). BioPlan Associates’ eighth annual survey of biopharmaceutical manufacturers (with 352 global respondents) shows that, second only to single-use/disposable bioprocessing equipment, the industry is asking for new, improved, more relevant and cost-effective assays and analytical instruments. In particular, this need is felt most acutely among CMOs that use a lot of disposables — and that often requires greater process control to ensure cost management for their ...
Today’s renewed interest in perfusion culture is due to an increased awareness of its advantages, some general improvement in equipment reliability, and a broadening of operational skills in the biomanufacturing industry. Some misperceptions persist, however, according to a 2011 review by Eric Langer (
1
). Our view here of the history of perfusion and fed-batch processes includes some discussion of technological process improvements and challenges that the bioprocess industry faces.
A team of authors at Serono in Switzerland wrote in 2003:
The major advantage of the perfusion mode is high cell number and high productivity in a relatively small-size bioreactor as compared with batch/fed-batch. In order to sustain high cell number and productivity, there are needs to feed medium during the cell propagation phase and the production phase. In contrast to batch and fed-batch processes, where there is no metabolites removal, in continuous processes medium is perfused at dilution rates exceeding the cellular gr...
The 2009 Biologics Price Competition and Innovation Act (BPCIA) provided the bioprocessing industry with the legislative pathway toward approval of biosimilars. US Food and Drug Administration information regarding how it will translate that legislation, however, had been limited until an August 2011 article finally provided some insight on how those guidances might actually play out (
1
). As expected, the agency appears to be implementing a science-driven approach, with sponsor companies needing to apply complementary orthogonal analytical methods to present a “totality of evidence” required to verify “sufficient similarity.”
Even before BPCIA, the industry had some ideas of the manufacturing requirements and analytical specifications that might pertain to biosimilars development. The European Union developed a general guidance in 2005 (under revision) and has since released other guidances for specific biologic types. Likewise, the International Conference on Harmonization (ICH) published its Q6b quali...
Vaccines are powerful and cost effective prophylactic tools for protecting public health. The Global Alliance for Vaccines and Immunizations (GAVI) estimates that ~5.4 million lives are saved each year by the administration of vaccines for hepatitis B, measles, haemophilus influenza type B (hib), pertussis (whooping cough), yellow fever, and polio (
1
). According to the World Health Organization, seasonal influenza alone claims 250,000–500,000 lives every year globally, many of which could be prevented by more widespread vaccination with the seasonal influenza vaccine (
2
). Currently, vaccines are available for 26 indications, and those for at least 12 more indications are in clinical trials, with anticipated approval and launch in the next five years (
3
). Overall, the worldwide vaccine market registered revenues of US$10.6 billion in 2005 and $21 billion in 2008, and they are projected to increase to $35 billion by 2015 (
4
,
5
). Thus vaccines represent a clinically important sector as well as one ...
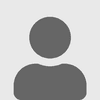
+1At small to medium scales, single-use technology offers significant advantages over traditional reusable (e.g., stainless steel) manufacturing technology with regard to flexibility, cost of goods, implementation timelines, and maintenance. However, process design based on disposables does create new challenges. With traditional fed-batch processes, harvest clarification is usually achieved by centrifugation followed by depth filtration. For processes based entirely on disposables, the disc-stack centrifuge needs to be replaced by filtration alone.
To extend its manufacturing capabilities and capacities, Rentschler decided to build two 1,000-L scale cell culture good manufacturing practice (GMP) lines based exclusively on single-use equipment. During the design phase, the team performed and reported several studies on disposable equipment characterization (
1
,
2
). In this concept study, we evaluated single-use depth filtration systems from different suppliers for potential implementation into a high–cel...
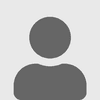
+2Scaling up biological processes from laboratory bench to process scale is complex and requires considering a number of factors to ensure process robustness. Due to variability among raw materials and processes, most process developers use generous safety factors to ensure that their systems are not undersized. Although that method can be reduce process risk, it is inefficient.
To improve process efficiency and reduce risk, we conducted a study to identify and quantify key factors that contribute to variability in filtration scale-up. The results from this investigation revealed that successful scale-up and improved process efficiency could be realized by
PRODUCT FOCUS
: ALL BIOLOGICS
PROCESS FOCUS
: DOWNSTREAM
WHO SHOULD READ
: PROCESS DEVELOPMENT AND MANUFACTURING
KEYWORDS
: MICROFILTRATION, SCALE-UP, VARIABILITY, MEMBRANE FOULING
LEVEL:
INTERMEDIATE
PROCESS DEVELOPMENT SCALE-UP CHALLENGES
Process developers favor small-scale sizing tools for initial evaluations of filter performance in process streams ...
The biopharmaceutical industry needs faster and more efficient development of new drugs and their market introduction as well as shorter process development times for both upstream and downstream operations. It has become more commonplace to use high-throughput development techniques to save time (
1
). Development is also sped up by applying platform technologies based on the unsurpassed selectivity of protein A resins (
2
,
3
,
4
,
5
,
6
), which is the foundation for downstream processing of monoclonal antibodies (MAbs).
This is the second of two articles describing development of a downstream process for a MAb product, from screening in 96-well plates to scale-up using two separate formats. The first article covered rapid microplate development in
BioProcess International
a year ago (
7
).
We developed a highly efficient two step chromatography process by applying high-throughput process development (HTPD) techniques using PreDictor plates for screening (
7
) followed by optimization in small-column...
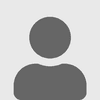
+3Antimicrobial Incubator
Product:
Multitron incubator shaker
Applications:
Cell line screening and seed cultures for larger validated processes
Features:
ATR has added an optional antimicrobial coating to the interior of its Multitron incubator shaker cabinet. This exclusively formulated coating inhibits the growth of bacteria, molds, and fungi over 100,000-fold. The coating is safe, effective, long-lasting, and approved for use in medical and food industries by independent certification. It is applied in production and can be ordered with any Multitron unit. All cabinets incorporate an independent control and power system, with redundant control of speed, temperature, lights, humidity, and CO
2
Contact
Appropriate Technical Resources
www.atrbiotech.com
Disposable Flow Control
Product:
Bioclamp, BioEnd Cap, and Biovalve components
Applications:
Single-use systems
Features:
Qosina offers a number of new bioprocessing components for disposable systems. Patented barbed flanges with preattached gaskets...
The BioProcess International Conference is where challenges are explored, solutions are uncovered, and opportunities are developed, making it the largest and most highly respected event solely dedicated to biopharmaceutical manufacturing. Save time and reduce cost of goods with tips on streamlining processes and implementing novel technologies. Find new collaborators and partners with superior networking opportunities at the industry’s largest event devoted solely to biopharmaceutical production. Consult with >150 providers of novel and practical services and products in the exhibit hall. Present a poster of your own early results and receive feedback from your peers. Benchmark your company’s projects against industry leaders by hearing >180 case studies and cutting-edge presentations. Participate in strategic discussion forums to hear behind-the-scenes perspectives on the latest industry challenges. Get exclusive preevent access to attendees online at LinkedIn; start discussions with fellow attendees wel...
On 31 March 2011, ~50 delegates attended a workshop organized by STEMCELL Technologies on implications of standard defined culture conditions for embryonic and induced-pluripotent human stem cells as part of the annual meeting of the UK National Stem Cell Network in York, UK. Researchers from both academia and industry need to develop a better understanding of those implications. Our company wanted to give them a better appreciation of key challenges facing ancillary material suppliers who manufacture standard defined reagents. The workshop fits within the overall UKNSCN meeting, especially given increased interest in robust production of human pluripotent stem cells (hPSCs) for applications such as disease modeling, cell therapies, and drug screening.
On Defined Media
Scientific talks began with an excellent exposition of key issues and challenges in using commercially available media by Lyn Healy from the Health Protection Agency’s UK stem cell bank based at its NIBSC site. Such media make it possible t...