Helium Integrity Testing (HIT™) for 2-D Bioprocessing VesselsHelium Integrity Testing (HIT™) for 2-D Bioprocessing Vessels
August 1, 2011
Technology Innovation
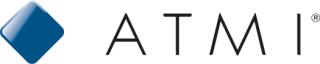
ATMI® is an acknowledged technology leader in the development and manufacture of single-use bioprocess systems and consumables. Its innovative disposable technologies, best-of-breed polymer films, ultraclean ISO Class 5 manufacturing conditions and whole-bag integrity testing set a high bar for the single-use industry. Today, ATMI is raising the bar even higher with the introduction of Helium integrity Testing (HIT™). Helium Integrity Testing
ATMI’s patent-pending HIT technology allows each ATMI 2-D Bioprocess vessel (BPV) to be tested for defects that can compromise sterility but are too small to be detected by conventional pressure-decay methods. The test protocol involves placing each finished BPV assembly into an enclosed test chamber, evacuating the chamber air to create a vacuum, and then introducing a measured quantity of helium gas into the BPV. The helium-filled BPV is then held for a fixed time while the surrounding vacuum is monitored for leaking helium using a sensitive mass spectrometer.
As with ATMI’s pressure-decay method, the new HIT technology is a “whole-bag” test. The entire finished bag, including fittings, tubing, and connectors, is tested at the end of the manufacturing process. This approach is much more likely to detect defects than less satisfactory “chamber-only” testing approaches. Detection Sensitivity
Independent third-party laboratories performing bacterial challenge testing on single-use bags have concluded that bacterial ingress can occur through pinholes as small as 15 µm, whereas pinholes at or below 10 µm present little or no risk of sterility breach. Conventional whole-bag pressure-decay integrity testing is typically sensitive enough to detect only pinholes down to about 90 µm. To gain more sensitivity, it is necessary to limit the testing to only the bag chamber and work at pressures and test durations that are ill-suited to in-production release testing. In practice, this limits the usefulness of pressure-decay integrity testing. By contrast, ATMI HIT technology has been validated for reliable detection of pinholes as small as 10 µm, even in the context of an in-process whole-bag product release test. This makes HIT the method of choice for testing BPVs destined for the most critical applications such as high-value API, final fill, and cell therapy.
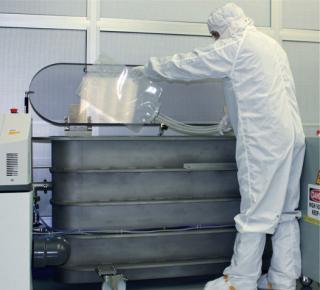
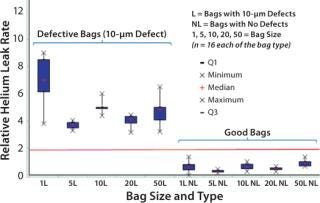
Figure 1: ()
Availability
ATMI 2-D BPVs up to 50-L size are now available as HIT-tested variants. Standard configurations are available, or custom assemblies can be tailored to end-user requirements. Contact your ATMI representative to discuss your specific needs.
About the Author
Author Details
Richard Bhella is global product manager of single-use storage and delivery technologies, 2151 East Broadway Road, Suite 101, Tempe, AZ 85282; 1-480-350-7142; [email protected]; www.atmi-lifesciences.com. ©2011 ATMI, Inc. All rights reserved.
You May Also Like