Safety, Flexibility, and EfficiencySafety, Flexibility, and Efficiency
December 1, 2012
International pharmaceutical and biotech companies are demanding solutions for current and future challenges of their industries — solutions that will stand the test of time while offering significant advances over current manufacturing techniques. Modern and highly proficient production lines for commercial manufacturing of parenteral drugs can represent a crucial criterion in the success of these companies. New and innovative high-speed filling lines for prefilled syringes present an excellent opportunity to meet current production demands. Following is an example of how the latest filling technology fits in.
Creativity is critical for sustaining new solutions, but it can often be constrained. The global market for medications involves demands from a number of sources. For example, guidelines from official regulatory agencies are becoming stricter as drug patents are expiring. Meanwhile, competition is becoming fiercer, as are pressures on price. Original manufacturers of biopharmaceuticals faced with spending immense costs to develop and manufacture such products face competition from biosimilars.
Photo 1:
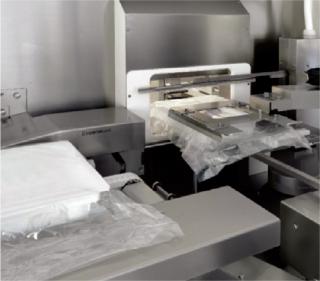
Photo 1: ()
The industry has changed, moving from a blockbuster-dominated market with a few drugs bringing in large revenues to one with a far broader range of products to offer. Although the current situation is tough and promises to remain so, leading market experts do see a number of areas in which growth is quite possible. Among those are “pharmerging” markets: countries and regions where income levels are rising and health care is growing in importance. Another growth area is in innovative therapies — for example, those based on sensitive biotech substances and injectable drugs (including the prefilled syringe segment). Drug manufacturers should take a careful look at such developments to discover what opportunities they might afford, the most basic of which would be modern solutions for commercial manufacturing. Taking advantage of the specialized know-how of contract development and manufacturing organizations (CDMOs) can help sponsors meet manufacturing demands. Because CDMOs keep close track of the market, they often operate facilities that are designed to meet future challenges.
Tomorrow’s Demands
To get a glimpse of what tomorrow’s fill–finish lines will look like, it’s a good idea to analyze and understand the market trends and developments. Many regulatory agencies have put forth strict guidelines regarding not only parenteral products themselves, but also the manufacturing processes that make them. Quality and safety have been rightly prioritized. Processes must be consistent and go beyond the capabilities of solutions that currently exist. For drug companies, however, cost pressures and competition require processes that are efficient and flexible. All the while, product sponsors must optimize unit costs and prevent losses due to waste of what is in some cases very expensive material.
The former blockbuster model, for example, allowed for “monoplants,” manufacturing facilities built and operated to support single products. To achieve an economically viable capacity use rate, modern facilities must allow for filling and packaging of multiple different drugs. Aseptically filling parenterals is a particular challenge because many such substances are complex and very sensitive to their environment and even traditional packaging elements such as silicon oil. Therefore, such products require special handling and often separate development solutions that must be conceived and implemented early in process planning.
Photo 2:
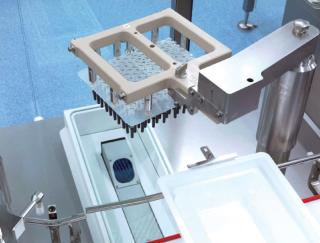
Photo 2: ()
Packaging options such as prefilled syringes and devices (e.g., autoinjectors and pens) require additional complex fill–finish processes. So CDMOs may well represent the facilities of the future.
Their business model requires that they be designed to meet those current demands while providing their customers with safe, flexible, and efficient solutions for tomorrow.
A Case Study
Current market trends call for new technologies and intelligent solutions for commercial manufacturing of injectable drugs. In response, Vetter has developed a novel, high-speed filling line for prefilled syringes. It was built in collaboration with Robert Bosch Packaging Technology specifically for manufacturing medium to large amounts of parenteral drugs. The filling line itself was designed for syringes that are presterilized and come in tubs. Automating the handling of those tubs demanded a number of technical innovations such as an automatic disinfection tunnel, which was crucial for future-proof quality and safety standards.
Photo 3:
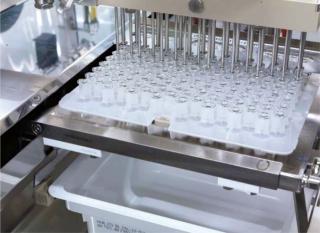
Photo 3: ()
To enable high-capacity use, the line had to be conceived for a number of filling processes depending on the specific drug substance involved. Efficiency for fast and safe product changeover was achieved through creation of a fully automated processing sequence. The following detailed review of the new line shows how and why it can support high quality and safety for streamlined operations in the future.
Achieving Safety: Presterilized injection systems are now an accepted alternative to bulk systems. Syringes are delivered washed, siliconized, sterilized, and validated — ready to be processed — and are nested in magazines that are sterile-packed in tubs for transportation. The tubs themselves are wrapped in sterile, protective bags. According to client preference, those tubs can also be packed in a second protective bag.
Presterilized syringes simplify production preparations for drug manufacturers. Nevertheless, the entire process must be maintained at a high aseptic level, which is not as simple as might be imagined. The most difficult challenge comes in i
ntroducing the tubs and the syringes into the critical area for filling. So the new filling line features several innovations. Necessary for the fully automated processing of the tubs is a specially developed disinfection tunnel and a number of solutions for aseptic transfer of those tubs from lower to higher cleanroom classes.
Safe Tub Processing: Syringe tubs begin their journey in a hygienic logistics area, where they are still wrapped in their protective bags. They are then placed on a conveyor belt that transports them to a class C cleanroom. If a tub is wrapped in two protective bags, then the outer one is removed on the way from the logistics zone to the classified area. An automated cutter performs this task, and a unique tool keeps the bag shut until the zonal transition. At the edge of the classified zone the protective bag is opened, then a tub proceeds into the higher cleanroom classification area. Tubs with a single protective bag are transferred directly into the class C cleanroom. Either way, this process ensures that tubs in the classified area have a single protective covering.
Packaging is then disinfected in an automatic spraying tunnel, where the wrapping is liberally sprayed with a disinfectant by jets on all sides. The automatic spray disinfectant system can be used with alcohol as well as sporocides and other substances that meet regulatory requirements. Syringe tubs remain in the tunnel for a determined reaction time before being transferred through a crossing point into the filling zone, which is a class A cleanroom. The disinfected wrapping is cut open here — but again, it is kept mechanically closed until the tubs can be introduced into the higher-classification cleanroom. So before entering class A, the protective bag is automatically removed and disposed.
Raising the Standards: The problem of transferring syringe tubs into the classified area is solved by automatic handling. The process at the Vetter line was designed to go beyond current standards, which representing an answer to future demands as well. That is further supported by a number of innovative in-process controls. Before filling, for example, each syringe is tested for having its necessary closure parts. The test is performed using an in-line three-dimensional (3D) scanner. Any syringe with missing parts will not be filled.
That monitoring system is based on an end-to-end, track-and-trace system with testing and documentation features. Cameras feed fundamental data about the tubs into the system, including the number and formats of nested syringes. Any errors are noted, such as the absence of closure parts. The tubs and syringes concerned are precisely recorded. An in-line printer writes related data onto a given tub for follow-up measures. And at the end of the line, a robot automatically removes all syringes with missing closure parts from the tub. This process is vital for safety because it prevents contamination of the machine base through missing closure parts.
Flexibility for the Future: For economic reasons, future-proof filling facilities need to meet the specifications of many different substances. Like the line described above, they must be prepared to implement a number of different processes. A fundamental criterion for effective lines is their ability to fill a range of products, delivery systems, and formats. Suitable packaging and volumes will be needed to meet different demands.
The possibility of using tubs with single or dual protective bags allows for use of presterilized syringes made by different suppliers. The filling station can operate up to 16 filling heads. Tubs with up to 160 nested syringes can be processed on the line. It is also flexible in handling format parts for different syringe sizes. A number of procedures may be used to set stoppers so that syringes and stoppers with a range of silicon films can be processed. To create the right production conditions for different substances — each with its own unique requirements — the line was built to integrate several pumping systems. For suspensions, permanent recirculation of solution is also possible.
Fast and Safe Product Change-Over: One of the most complex and risky processes in aseptic filling is the transition between products on a line, which usually involves time-consuming disinfection and sterilization of everything in the cleanroom. Designing a state-of-the-art facility — one that can handle tomorrow’s industry needs — must include a concrete strategy to perform change-overs quickly and efficiently. For Vetter, the best solution was to rely on a technology with which the company has had long experience: the restricted access barrier system (RABS).
Photo 4:
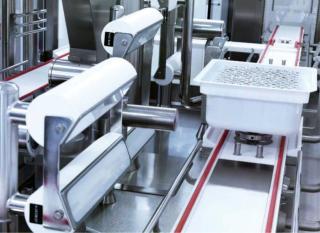
Photo 4: ()
RABS derives its flexibility and safety from the basic idea that germs and particles tend to enter cleanrooms with people. So a RABS structure essentially enables stringent separation of users and areas/equipment that contact a drug product. Critical zones in a filling area are segregated by walls and doors made of synthetic materials. Special ports at strategic locations in the walls allow the use of gloves to perform the few remaining manual tasks needed for a product change. The area inside the walls is maintained under cleanroom class A conditions. Laminar-flow air travels from the ceiling downward and surrounds the filling machine. That air then leaves the class A area by flowing underneath the barrier into the operating area, which is under class B conditions. From there it is redirected, filtered, and returned to the ventilation system.
During format change and filling operations, separating walls are kept closed. Barrier doors can be opened only when a machine is cleaned after a manufacturing process and microbiological monitoring. Line clearance can be given only after a high-level disinfection process using a sporocide. When production is complete, gloves are removed and tested for integrity (e.g., using a pressure decay test to spot even the tiniest of holes). If the gloves are airtight, then they can be cleaned, sterilized, and mounted back into the glove ports. A format change can then be performed using those gloves and without any tools. Format parts are equipped with click-on locks for rapid change-over. Parts can be installed easily in their appropriate place using the glove ports.
Sterilized format parts must be brought into the line using a SteriSet container from Medline Industries Inc. of Mundelein, IL. In support, disinfection is performed quickly and reliably, with all parts of the machine or format parts that will contact products made of resistant and autoclavable materials such as stainless steel or silicon. Depending on the products involved, line clearance and set-up can be finished within as little as four hours.
Creating Greater Efficiency
Shortening the time needed to prepare this filling line for operations means greater capacity use of the facility. The line can work on a 24-hour day to manufacture several products, which greatly increases the facility’s efficiency and productivity. Depending on the format and substances being filled (and substracting the time needed for line clearance and set-up), a filling line of this type can operate for up to 20 hours each day. If all 16 filling he
ads are used, up to 50,000 units can be filled in an hour for a maximum daily output of up to a million syringes.
Smooth operations are enabled by a system that automatically prevents erroneous filling of syringes that don’t have closures, which in turn allows for fewer interruptions. And the high level of automation allows for a lean operating concept. Three operators are the most needed to run this line, depending on the situation and momentary requirements.
Naturally, the filling system itself is not the only contributor to high-efficiency operations in this case. The design of the building itself is important to enable short paths between processes. The distance between compounding and the filling station should be as short as possible to permit the greatest possible use of available substance supplies and prevent losses of active pharmaceutical ingredient (API). Overall, shorter preparation times, higher capacity use, and leaner operating resources all contribute to optimizing operations — thus keeping unit costs down.
Tomorrow Begins Today
A high-speed filling line like the one described herein illustrates how tomorrow’s requirements in the field of aseptic filling of injection systems can be anticipated and met. The decisive qualities that a manufacturing plant must have in the future will be flexibility and efficiency — while maintaining high aseptic safety. High-output processes can be adapted for different substances, changing from one product to the next quickly, reliably, and safely. The innovations described above demonstrate how commercial manufacturing lines can contribute to meeting cost and competitive pressures amid increased regulatory demand. They also support drug companies in their efforts to develop innovative therapies and enter growing market segments for injectables.
About the Author
Author Details
Bernd Stauss is vice president of production and engineering at Vetter Pharma-Fertigung GmbH & Co. KG, Schützenstraße 87, 88212 Ravensburg, Germany; 49-751-3700-0, fax 49-751-3700-4000; [email protected]; www.vetter-pharma.com.Vetter Development Service of Chicago, IL, was a manufacturing technology finalist in the BPI Decade awards for its clinical trial solutions for filling drug-delivery systems.
You May Also Like