CelliGen® BLU Single-Use, 5-L and 14-L BioreactorCelliGen® BLU Single-Use, 5-L and 14-L Bioreactor
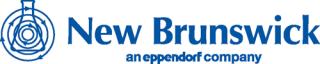
Whether you are culturing animal cells in an R&D laboratory or in a pilot production facility, your ability to precisely control all process parameters is critical. Culture yield depends on it, and should your process go into production, FDA requirements mandate it. Therefore the performance of your bioreactor’s controller is as important as a good vessel design, as an optimized medium formulation, or selection of the right cell line.
This article focuses on the process control capabilities offered by the CelliGen® BLU, New Brunswick Scientific’s new, benchtop stirred-tank bioreactor with single-use, 5- and 14-L vessels. While much has been written (1,2,3) about its unique vessels, non-invasive sensor design, and rapid turnaround time between runs, much less has been documented about its custom-configurable process control capabilities. Designed to provide the flexibility for high-density growth of animal or insect cell lines, the highly flexible CelliGen BLU bioreactor is as capable as it is easy to use.
Flexible Control Options
New Brunswick’s CelliGen BLU bioreactor controller has been specifically engineered to be easier to operate, yet offer a high degree of advanced control options as well as the ability to fine-tune settings to your process needs, than any NBS benchtop bioreactor we’ve previously designed.
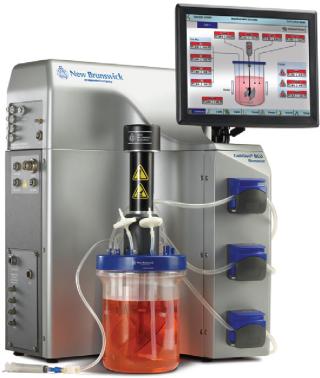
Featuring highly configurable controls and interchangeable 5-L and 14-L single-use vessels, New Brunswick Scientific’s CelliGen BLU bioreactor provides the versatility needed for research as well as the advanced process control required for cGMP production. ()
Process control options offered with the CelliGen BLU include the following:
User-definable Proportional and Integral (PI) settings for pH, DO, temperature, and agitation-speed control loops. PI settings affect how quickly and to what degree the controller responds to a deviation between setpoint and current value for a given process control parameter. PI values can be easily altered by entering new values through the bioreactor’s control screen.
User-definable cascade control settings. Cascade control simply means that one process control parameter (e.g., pH or DO) is regulated by other (one or more) process control parameter values (e.g., agitation speed or gas flow). CelliGen BLU’s cascade control screens incorporate temperature, agitation speed, gasses and three pumps; as well as values from up to 7 ancillary devices such as a gas analyzer or supplementary pumps (Figure 1).
Additionally, standard cascade control settings are built into each system to simplify operation. A weight scale option is offered that can be directly linked to integrated peristaltic pumps to precisely measure feed additions or harvest volumes. Multiple options for gas-flow control are also offered, as described in detail below.
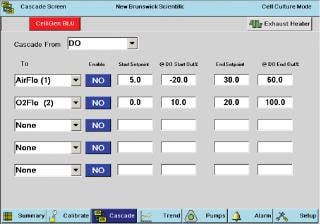
Figure 1: ()
Advanced Gas Control
Gas control (percentage proportion of gas in total gas mixture and the gas flow rate) is critical in animal cell culture applications as a means of controlling important process control parameters, such as pH, DO, and other dissolved gasses. Therefore how the bioreactor controls the addition of one or more gases is of vital importance.
The CelliGen BLU can be equipped with controls for direct sparging of gas into the culture medium, and for addition of gas above the liquid contents (the overlay). Depending on the requirements of your process, factory-installed options for none, one, three, or four Thermal Mass Flow Controllers (TMFCs) are offered for sparge gas control (Figure 2) and up to one TMFC can be installed for the overlay gas control. Alternately, a manual Rotameter may be installed for sparge and/or overlay gas control.
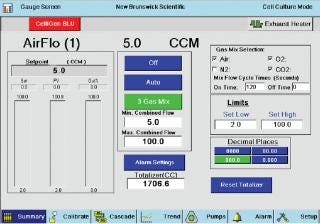
Figure 2: ()
TMFCs are extremely accurate gas-flow control devices that can be used to automatically alter gas flow rate based on a feed-back mechanism by the system controller. Because there is a direct communication between the TMFCs and the controller, the TMFCs provide a digital recordable signal back to the controller regarding the amount of individual gas being supplied to the cell culture medium in the vessel and head space. Further, the use of TMFCs for accurate gas control allows easy and rapid scale-up of your cell culture process from laboratory to production scale level.
Control Screens: Easy to Use and Navigate
Each CelliGen BLU controller runs on New Brunswick’s Reactor Process Control (RPC) software, which is the same control platform used on all New Brunswick’s benchtop CelliGen® bioreactors and BioFlo® fermentors manufactured after 2007. The RPC is interfaced through a bright, fifteen-inch color touchscreen display. Control screens include features such as on-screen calibration of pH and DO, a synoptic display to show system control; and a multi-parameter user-customizable trend screen to display setpoints and current values over time. Control screens have been specifically created for ease of navigation between screens (Figure 3).
‘width:330px;background-color: #f7f7f7;border:1px solid #adaaad;’>
Figure 3: ()
The RPC also provides the ability for users to customize and fine tune their control strategy by editing factory-set P and I settings for each control parameter, and to construct custom cascades. Cascades –like PI settings — allow users to dictate when and to what degree the controller will respond to correct deviations from setpoint. The RPC provides an easy-to-edit cascade control screen, making it simple to fine tune process control. To further enhance control, each CelliGen BLU comes equipped to communicate with New Brunswick Scientific’s optional BioCommand® Supervisory Control and Data Acquisition (SCADA) software, as well as with up to seven analog input/output devices which can accept 4-20ma or 0-5v signals.
With such a wide array of installable options, together with the capability to accurately and precisely control process parameters, and an easy-to-use interface, the CelliGen BLU is an ideal bioreactor system for any animal cell culture facility.
About the Author
Author Details
Rich Mirro is product manager; Vikram Gossain, PhD, is applications and training manager, and Suzy Kedzierski is marketing communications manager of New Brunswick Scientific, PO Box 4005, 44 Talmadge Rd., Edison, NJ 08818-4005; 1-732-287-1200, toll-free in N. America 1-800-631-5417; [email protected], www.nbsc.com/BLU.
REFERENCES
1.) Gossain, V, R Mirro. 2010. Hybrid System Aims to Streamline Cell Culture: Bioreactor Combines Single-Use vessel with Stirred-tank design, GEN. Gen. Eng.Biotechnol. News.
2.) Wang, G, W Zhang, and R. Mirro. 2009. CelliGen BLU applications report: New Benchtop Bioreactor Uses Presterilized, Prevalidated, Single-Use vessels to Simplify Cell Culture. Nature Methods.
3.) Wang, G, R Mirro, and V. GossainCelliGen BLU Protocol: Growing CHO Cells in a CelliGen BLU Benchtop, Stirred-Tank Bioreactor Using Single-Use Vessels.
You May Also Like