Safety in Single-Use SystemsSafety in Single-Use Systems
August 1, 2012
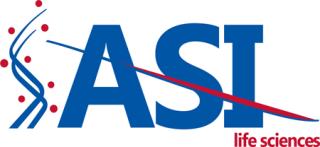
Single-use technologies are a growing market and becoming increasingly common in biopharmaceutical manufacturing. Because of this growth and their increasing use in further reaches of upstream and downstream processes, understanding the safety and sanitation of single-use technology is vital.
One of the key benefits of single-use systems is their potential to eliminate cross-contamination during pharmaceutical manufacturing. In processes that are entirely single-use, replacement of the fluid path assembly during production eliminates the concern for contamination in any valve or line.
Safe from the Start
A quality, sterile product comes from a quality, sterile manufacturing partner who understands the critical nature in which single-use systems will be used. ASI is an ISO 13485:2003, FDA-registered manufacturer that has built upon regulatory foundations through the use of a customized quality management system intertwined with enterprise resource planning (ERP) software. From incoming raw material inspection, throughout the entire manufacturing process, to the final finished product, ASI’s ERP and Quality Management system is integrated in every step — making ASI a leader in quality manufacturing.
Preassembly and Gamma Sterilization
To completely eliminate the concern for safety, ASI disposables can be ordered and delivered preassembled and sterilized. ASI has validated its irradiation process to ensure that each product exceeds industry standards regarding sterility and validation, delivering an assembled, sterile product in three weeks.
When using a preassembled product, the entire fluid path can be discarded after use, which negates the need for cleaning and vastly improves production turn-around time. In some cases, single-use systems can reduce the number or duration of technician ingress into controlled environments, thereby further reducing the risk of microbial contamination.
Less Contamination Risk, Less Capital Investment
Quality, safety, and production are all crucial considerations for the switch to or expansion of single-use systems in production. Many companies have realized savings in capital investment through the use of disposable products.
Cost reduction can be shown in several ways as it relates to incorporating single use. For a new installation, single-use-systems have been shown to be a less costly investment. The footprint needed for single-use-systems is considerably smaller, freeing up production space and utilities. Additional cost savings can be seen through the reduction in costs related to cleaning, validation, and qualification.
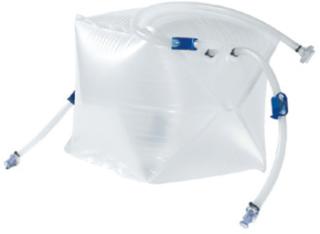
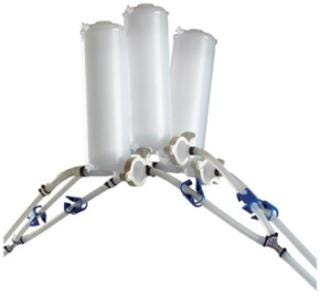
Innovative Safeguards
ASI takes every step to ensure quality, sterility, and regulatory compliance throughout their in-house design, product sterilization, and delivery but plans to extend the quality assurance a step even further through its patent-pending inSITE inflation and integrity test System. The Integrity Test System from ASI (which will become available in September) gives customers the chance to run a final Integrity Test on ASI’s single-use bags before loading and filling to eliminate concern for gross and fine leaks that could occur from delivery and loading procedures.
About the Author
Author Details
Derek Masser is the life sciences manager at ASI, 163 Research Lane, Millersburg, PA 17061; 1-717-692-2104 x256; [email protected]; www.asisus.com.
You May Also Like