- Sponsored Content
- Downstream Processing
A Frost & Sullivan Virtual Think Tank: 3M™ Polisher ST Beta Testing SeriesA Frost & Sullivan Virtual Think Tank: 3M™ Polisher ST Beta Testing Series
December 2, 2021
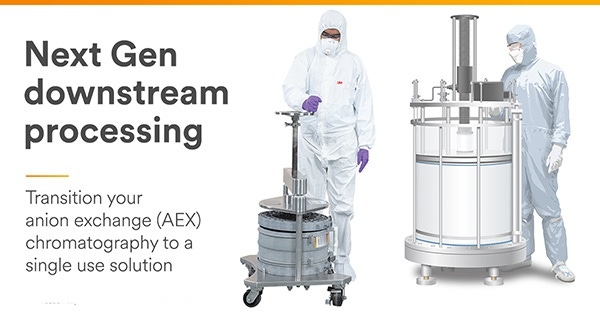
Already have an account?
Sponsored Content
One step can change everything: Replace your flow-through AEX column with a novel single-use polishing solution
3M™ Polisher ST single use polishing solution – from lab to manufacturing scale
Frost & Sullivan recently invited a panel of bioprocessing industry leaders and key opinion leaders to participate in a Virtual Think Tank (VTT) Early Access series – a new and unique thought leadership forum.
Each VTT panel, comprised of professionals from top pharmaceutical companies, contract development and manufacturing organizations (CDMOs) and 3M Company, discussed the 3M™ Polisher ST technology following participation in a beta test program.
Overall sentiments from the panelists indicate that adoption of 3M™ Polisher ST allows for high product purity and process compression of polishing step to create a robust manufacturing process that can be applied across a range of process conditions.
Manufacturing biopharmaceuticals at a commercial scale is a costly, complex, and lengthy process due to their unique properties and the variations of monoclonal antibodies (mAbs). Despite this, biopharmaceutical companies continually face pressures to commercialize and manufacture therapies faster and at lower costs. Consequently, technology developers like 3M™ are heeding their demands and developing innovative new technologies to improve the tedious and expensive biologics manufacturing workflow. As part of their process intensification strategies, biopharmaceutical companies and CDMOs are turning to innovations like single-use technologies that condense process steps, drive efficiency, and reduce the total cost of ownership. One such technology launched by 3M™ is their 3M™ Polisher ST—a single-use AEX chromatography device that uses a guanidinium-functionalized polyamide membrane protected by a Q-functionalized non-woven material. 3M™ Polisher ST replaces the traditional resin-based columns in the biopharmaceutical manufacturing process while simplifying the workflow. The ST stands for its functional membrane’s salt tolerance capability, which allows it to function at a wide range of conductivity.
The major benefits hailed by expert panelists during the VTT included:
• The disposability, speed, ease-of-use, modularity, and configuration of the product
• The improved viral clearance ability and flexibility to work with various conditions (pH 5.5 to 7.5) and conductivity of 3 to 20 mS/cm
• The single-use aspect, which drives the volume adaptability
• The capsule capacity of 100 times that of a traditional Q resin, which allows for easy commercial scalability
This white paper summarizes the VTT and the panelists observations.
About the Author
You May Also Like