Minimizing the Environmental Footprint of Bioprocesses September 2010Minimizing the Environmental Footprint of Bioprocesses September 2010
September 1, 2010
Biomanufacturers must take active measures to minimize their environmental footprints and promote environmental sustainability. The collateral benefit of reducing environmental footprint often is viewed as only a secondary consideration after cost of goods and product quality. Biopharmaceutical processes are 80% defined by the time of proof-of-concept studies (clinical trial stage 2b). This milestone is before the official technical transfer to commercialization or manufacturing organizations and almost always before the environmental evaluation of a production process. This step is considerably earlier in the development lifecycle than it is for the development of pharmaceutical products. Consequently, an urgent need exists to rebalance current process evaluation criteria and advance evaluation timing to raise emphasis on environmental footprint reductions early in biopharmaceutical product development.
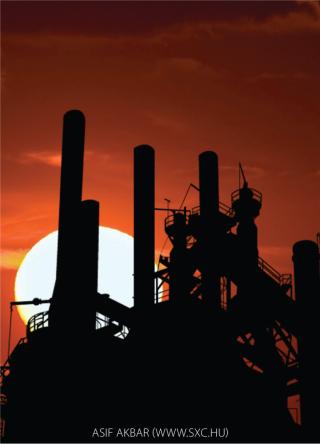
Because the number of biopharmaceutical products is increasing and bioprocess productivity is rising, several biomanufacturers are redefining their missions or in some cases constructing new facilities. Therefore, the opportunity is expanding now to examine these environmental footprints. I’ve developed an initial framework for assessing microbial and animal cell biopharmaceutical processes, focusing on opportunities in early stage process development. Part 1 of this article identifies the impact of solid waste disposal. In an upcoming issue, Part 2 will discuss waste water, electricity, and air emissions.
PRODUCT FOCUS: ALL BIOLOGICS
PROCESS FOCUS: UPSTREAM AND DOWNSTREAM
WHO SHOULD READ: PROCESS DEVELOPMENT AND MANUFACTURING
KEYWORDS: SINGLE-USE, DISPOSABLES, SUSTAINABILITY, ENVIRONMENTAL IMPACT
LEVEL: INTERMEDIATE
About the Author
Author Details
Beth Junker is senior scientific director at Merck and company, RY808-130, PO Box 2000, Rahway, NJ 07065; [email protected].
REFERENCES
1.) Duran, N. 2002. Ecological-Friendly Pigments from Fungi. Crit. Rev. Food Sci. Nutrition 42:53-66.
2.) Thayer, AM. 2009. Supplanting Oil. Chem. Eng. News 87:22-26.
3.) Lütke-Eversloh, T, and CNS Santos. 2007. Stephanopoulos G. Perspectives of Biotechnological Production of l-tyrosine and Its Applications. Appl. Microbiol. Biotechnol. 77:751-762.
4.) Jenck, JF, F Agterberg, and MJ. Droescher. 2004. Projects and Processes for a Sustainable Chemical Industry: A Review of Achievements and Prospects. Green Chem. 6:544-556.
5.) Linich, D, and C. Park. 2009. It’s Not Easy Being Green — Unless You’re Lean. iSixSigma Magazine 3:45-50.
6.) Chatterjee, B. 2009. Lean Sustainability: Extending the Operational Excellence Paradigm. Controlled Environ. 12:19-21.
7.) Sciortino, M, and S. Watson. 2009. The Importance of Energy Efficiency in Lean Manufacturing: Declaring Energy the Ninth Waste.. ACEEE Summary Study on Energy Efficiency in Industry, American Council for an Energy Efficient Economy.:3-133-3-122.
8.) Calia, RC, FM Guerrin, and M. de Castro. 2009. The Impact of Six Sigma in the Performance of a Pollution Prevention Program. J. Cleaner Production 17:1303-1310.
9.) Jacobs, T. 2007. Taking the Lead in CGMPs: Is a Sustainable GMP Manufacturing Facility Achievable?. Contract Pharma:82-87.
10.) 2008. Facility of the Year Award Winner, Sustainability, Centocor Biologics, Ireland. Pharma. Pro.:24.
11.) Fitzgerald, D, and K. Bradley. 2009. Speed and Efficiency in Designing and Building a Monoclonal Antibody Pilot Plant. BioPharm Int. 22:24-31.
12.) Harrold, D. 2009. Going Green with MES. Control 22:33-35.
13.) El-Halwagi, MM. 2009. Apply Process Integration to Environmental Impact Assessment. CEP 105:36-42.
14.) Sheldon, RA. 1994. Consider the Environmental Quotient. ChemTech 24:38-47.
15.) Ho, SV. 2010. Environmental Considerations in Biologics Manufacturing. Green Chem 12:755-766.
16.) Kidwell, M. 2000. Lean Manufacturing: The Environment and the Bottom Line GreenBiz.com.
17.) Rawlings, B, and H. Pora. 2009. A Prescriptive Approach to Management of Solid Waste from Single-Use Systems. BioProcess Int. 7:40-47.
18.) Newman, D, and V. Isner. 2004. Environmental Considerations for Biomanufacturing Processes. French Industri Pharma page numbers not available 32.
19.) Mauter, M. 2009. Environmental Life-Cycle Assessment of Disposable Bioreactors. BioProcess Intl. 7:S18-S41.
20.) Sinclair, A. 2008. The Environmental Impact of Disposable Technologies. BioPharm International Supplement Guide to Disposables 4:4-15.
21.) Papavasileiou, V, C Siletti, and P. Demetri. 2009. The Role of Single-Use Systems (Disposables) in the Development and Manufacturing of Biopharmaceuticals. Pharma. Chem. 8:14-20.
22.) Patterson, BJ. 2009. A Closer Look at Automated In-Line Dilution. BioPharm Int. 22:52-65.
23.) Trexler-Schmidt, M. 2009. Purification Strategies to Process 5 g/L Titers of Monoclonal Antibodies. BioPharm International Supplement, Advances in Separation and Purification: Purifying High Titers:8-15.
24.) Anicetti, V. 2009. Biopharmaceutical Processes: A Glance into the 21st Century. BioProcess Int. 7:S4-S11.
25.) Zhou, J. 2008. Implementation of Advanced Technologies in Commercial Monoclonal Antibody Production. Biotechnol. J. 3:1185-1200.
26.) Rao, G, A Moreira, and K. Brorson. 2009. Disposable Bioprocessing: The Future Has Arrived. Biotechnol. Bioeng 102:348-356.
27.) Panda, AK. 2003. Bioprocessing of Therapeutic Proteins from the Inclusion Bodies of Escherichia coli. Adv. Biochem. Engin. Biotechnol. 85:43-93.
28.) Wegner, EH. 1986.. Biochemical Conversions by Yeast Fermentation at High Cell Densities. US Patent #4,617,274.
29.) Potgieter, T. 2009. Production of Monoclonal Antibodies by Glycoengineered Pichia pastoris.. J. Biotechnol. 139:318-325.
30.) Hang, H. 2009. A Simple Fermentation Strategy for High-Level Production of Recombinant Phytase by Pichia pastoris Using Glucose as the Growth Substrate. Enzyme and Microbial Technol. 44:185-188.
31.) Markl, H 1993. Cultivation of Escherichia coli to High Cell Densities in a Dialysis Reactor. Appl. Microbiol. Biotechnol. 39:48-52.
32.) Fuchs, C. 2002. Scale Up of Dialysis Fermentation for High Cell Density Cultivation of Escherichia coli. J. Biotechnol. 93:243-
251.
33.) Wang, DIC. 1979.Fermentation and Enzyme Technology, John Wiley and Sons, New York:94-95.
34.) Doran, PM.Bioprocess Engineering Principles, Academic Press, NewYork:75.
35.) Zabriskie, DW. 1999.Traders’ Guide to Fermentation Media Formulation, Traders’ Protein, Memphis.
36.) Gurramkonda, C. 2009. Simple High Cell Density Fed-Batch Technique for High-Level Recombinant Protein Production with Pichia pastoris: Application to Intracellular Production of Hepatitis B Surface Antigen. Microbial Cell Factories 8:13-20.
You May Also Like