Biomanufacturing Locally, Thinking GloballyBiomanufacturing Locally, Thinking Globally
June 1, 2010
Compared with other business sectors, the biopharmaceutical industry has been a high-tech laggard when it comes to outsourcing and off-shoring. That’s changing as companies acknowledge the strategic, cost, and market benefits. Over the past seven years of tracking outsourcing trends (1), I’ve seen interest in outsourcing grow, but that has kicked into high gear over the past couple years. Partly due to the economic and funding crisis and partly as a result of industry maturation, outsourcing is taking greater prominence as biopharmaceutical companies gain experience in managing outside operations. Bioexecutives are considering outsourcing models and creating the tools needed to assess different operating strategies.
This year, our seventh annual survey of biopharmaceutical manufacturing and capacity analyzed the data of 327 global biomanufacturer respondents and 125 suppliers to this industry. As detailed in the “Survey Methodology” box, the results cover a broad range of issues including capacity and outsourcing, downstream operations, disposables use, training, current budget shifts, refocusing of resources, quality management, and other trends. The study evaluates shifts over time and differences based on location.
Data this year indicate that companies are significantly more focused on improving manufacturing performance and efficiencies within existing budgetary and staffing levels. Outsourcing is one way organizations with the ability to manage outside vendors can achieve necessary efficiency. Companies often gain experience with outsourcing by progressing from managing less critical functions such as testing or fill–finish toward more complex services such as process development. As managerial experience increases, clinical-scale manufacturing and full-service operations can be introduced.
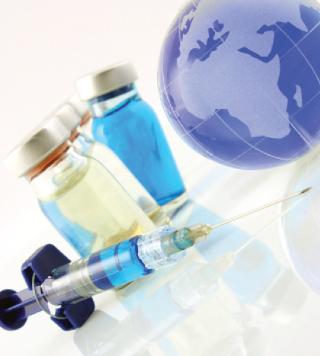
Industry news bears out this trend, especially in reports of how much Big Pharma plans to outsource. For example, Pfizer announced that it will increase outsourcing levels from ~17% to ~30% over the next few years. Merck also plans to double current outsourcing levels to 35% overall in the near future. AstraZeneca said in the fall of 2007 that it would outsource much of its drug manufacturing in 10 years, especially for projects with a sound business case.
Manufacturing Locally to Market Globally
Biologics outsourcing has clearly been on the rise. Companies are making decisions about where to manufacture based on strategic f it and proximity to markets. As developing regions such as China, India, and the Middle East grow economically, their demand for biologics is growing as well (2). Expanding middle-class populations are increasing those regions’ attractiveness as potential locations for outsourced and in-country domestic manufacturing.
Biomanufacturing is increasingly taking place in developing regions, and our study evaluated outsourcing outside the United States and Europe. Respondents were asked to predict their current plans for international capacity expansion, and we identified 35 countries as potential outsourcing destinations. Among all respondents, the United States topped the list as being a likely outsourcing destination (with 14% “strong likelihood” and 11.6% “likelihood”) over the next five years. After that, global manufacturers indicated India, Singapore, Ireland, Germany, the United Kingdom, and China as top international destinations.
US and European Outsourcing: Together, US and Western European biopharmaceutical companies represent >70% of the R&D efforts for the global biopharmaceutical industry and its primary sources of new drug innovation. In 1990, pharmaceutical R&D investment in the United States was actually less than that in Europe, but current investment in Europe is only ~70% of the US figure (3). During the past two decades, R&D investment in the United States grew by 5.6×, whereas in Europe it grew only by 3.5× (3). So an interesting angle to our seventh annual report is to see how biopharmaceutical companies in these two regions are outsourcing their manufacturing — and to compare the changes over time.
For example, US respondents see Singapore as an increasingly strong outsourcing destination (38% said the country was a “possible” destination this year, 31% in 2009’s report). Ireland jumped significantly as well, to second place this year with 35% considering outsourcing there as at least a possibility. Switzerland also showed a dramatic rise in popularity from last year; it will be interesting to see whether this preference continues into 2011. India ranked third. China fared less well as an outsourcing option for US companies in the latest survey, with an interest drop of nearly 10 percentage points from last year’s results.
For Western European biomanufacturers, the United States remains the primary destination for outsourcing. When we evaluate destinations according to any level of interest (rather than just a “strong” or “likely” response), 50% of these companies point to the United States (down two percentage points from last year). And India’s potential among Western Europeans grew significantly this year, with 22% considering it a possible outsourcing destination. Following were Germany and the United Kingdom as options, but both countries showed a noticeable drop in popularity from last year. On the other hand, India showed a rise in popularity for Western European biopharmaceutical companies — as did China, reflecting a more favorable view of these emerging markets by European respondents than those in the United States.
SUMMARY OF GLOBAL/LOCAL OUTSOURCING TRENDS
Issues that seem to have increased in perceived importance over the past few years:
Establish a good working relationship
Protect intellectual property
Effectively handle cross-contamination issues
Offer a secure supply (control of capacity)
Have regulatory compliance expertise
Issues that seem to have decreased in perceived importance over the past few years:
Demonstrate cost effectiveness of services
Demonstrate a track record with similar products
When asked about predictions of a strong likelihood or likelihood for expansion, Western European biomanufacturers indicated the United States at the top of their list (28.1% of respondents). Following was the United Kingdom (12.6%) and Germany (9.4%). India was next in line, with nearly 9.1% of respondents suggesting a strong or moderate likelihood to expand there (Figure 2). China was ranked lower on the list.
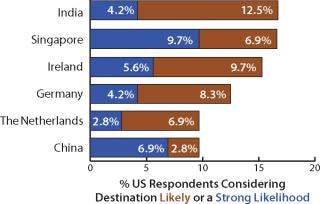
Figure 1: ()
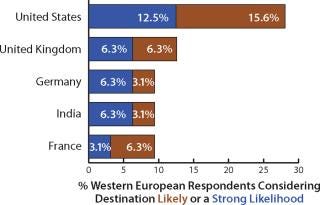
Figure 2: ()
However, China has been a very late starter in contract manufacturing, so it may still be too early for us to see it matching the growth prospects of India (4). The few internationally based contract manufacturing organizations (CMOs) in China are doing relatively well — e.g., AutekBio (www.autekbio.com). Nevertheless, there is excess pharmaceutical production capacity in China, where outsourcing is likely to take off once the idle capacity of many production facilities can be dealt with. Future annual surveys will be interesting indicators of when that trigger point is reached and how biopharmaceutical companies respond to the new opportunities that result.
Outsourcing Trends
Many biopharmaceutical companies have turned to outsourcing to control costs and manage their internal staff and other resources so in-house activities will be cost efficient. Economic conditions today are causing most organizations to reevaluate their core competencies and decide how they will direct their R&D and manufacturing resources. Our annual report shows that many today are using outsourcing more strategically than in the past. Outsourced projects now cover all areas of R&D, manufacturing, testing, and other services. CMOs and contract research organizations (CROs) are being used to fill temporary gaps in capacity, to focus companies’ skill base on their core competencies, and of course to control costs. Bio-outsourcing is maturing and becoming an essential part of both R&D and manufacturing strategies. Companies today face some tough economic challenges, and understanding trends can help the industry adapt to new realities in hiring, budgeting, and training.
In extreme conditions (such as the current economic situation), biotechnology companies have fewer choices and must reevaluate current strategies to survive and prosper. As a result, activities that were previously considered essential to retain in-house may become options for outsourcing. Although cost has always been an element of such decisions, biopharmaceutical companies are increasingly looking to the long term because their R&D cycles and production build-outs are lengthy and risk-intensive. Therefore, the additional benefits that outsourcing can bring to drug development and manufacture will swing many decisions toward this option. Similarly, potential outsourcing partners who can showcase value-added services beyond mere cost will be in the strongest position for deal-making.
Companies such as Pfizer are approaching outsourcing strategically as they determine what can be outsourced to reduce costs, optimize speed, increase flexibility of internal operations, and redeploy internal full-time employees (FTEs) on more value-added activities (5). Outsourcing decisions, although ultimately centered on financial return on investments, are thus initiated by analyzing the value of FTE activities, staff allocation, and hiring.
Outsourced Activities: Increasingly, biomanufacturers are outsourcing some activities to maintain productivity. This is especially true for current activities that are typically outsourced. In our study, we looked at 24 current areas of outsourcing. We found, for example, that 25% of biomanufacturers will be outsourcing significantly more fill–finish operations over the next 24 months than is currently done (Figure 3). Following are validation services and product characterization testing, with 24% and 23% of respondents, respectively, indicating them to be where the greatest changes will occur in their outsourcing. Other areas of substantial growth include toxicity testing and downstream production operations (with 18% and 14% of facilities, respectively, expecting substantial changes).
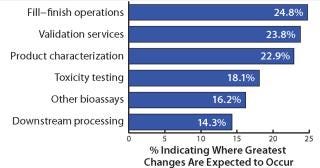
Figure 3: S ()
Given the more rigorous regulatory standards being imposed on biomanufacturers, it is interesting to note that relatively few respondents expect GMP training to be outsourced. Presumably, companies want to keep tight control over specific aspects of their operations and management. Biomanufacturers may not yet be sufficiently confident in their outsourcing partners’ ability to guarantee quality standards. An increase in regulatory inspections — often featuring collaborations among agencies — possibly accounts for the reluctance to outsource in this area.
Outsourcing Budget Changes: The annual report also looks at budgets for manufacturing activities. For example it shows that 30.4% of biomanufacturers plan to increase their budgets for outsourced biopharmaceutical manufacturing by at least 5% and 14% will increase them by at least 10%. Figure 4 shows average industry budget shifts for a few activities studied this year. Outsourcing budgets were relatively flat on average.
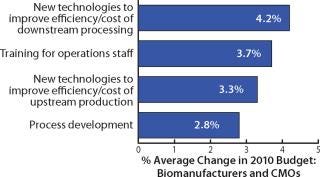
Figure 4: ()
Outsourcing today continues to be dominated by relatively lower value-added services such as fill–finish and product characterization testing. We found that the activity outsourced by the greatest percentage of respondents was product characterization testing, with >76% of biopharmaceutical companies outsourcing at least some of it (Figure 5). Toxicity testing (71.4%) and validation services (64.3%) were next on the list. At the other end of the scale appeared relatively low outsourcing activity for API biologics manufacturing and project management services.
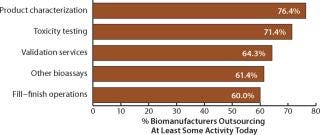
Figure 5: ()
Production Systems: Among respondents producing in mammalian cell culture this year, 57% indicated that they performed all their production in house (up slightly from last year), whereas 10.5% of respondents outsourced <10% of their production and 10.5% outsourced 10–25%. A small number (3.5%) outsourced 90–100% of their production. Over the past few years, the percentage of biotherapeutic developers doing all their mammalian cell production in house shifted upward slightly from 55.6% in 2006 to 57% today.
In microbial fermentation, 64.2% of respondents indicated this year that they performed all their production in house (up from 60.3% last year), whereas 17% of respondents outsourced 90–100% of their production. The percentage of biotherapeutics developers performing all their microbial fermentation in house has increased slightly over the past five years as well (from 58.1% in 2005 to 64.2% this year).
Interestingly, insect cell culture was reported to be done 100% in house (not outsourced), and 75% of plant cell culture is fully in house. With few insect and plant cell production platforms used in commercial manufacturing, these numbers indicate that both types of systems are primarily used for in-house manufacture of preclinical (and perhaps some early clinical) supplies.
We also examined how biopharmaceutical companies viewed the manufacturing outsourcing environment in the near future (to 2014). Overall, most companies plan to outsource at least some manufacturing. This was most relevant to mammalian cell culture, microbial fermentation, and yeast systems. By contrast well over half the respondents believed that no outsourcing would occur in the domains of insect and plant cell culture. It is interesting to see that some biopharmaceutical companies believe that certain areas are still not appropriate for outsourcing. Relatively few organizations want to hand over plant or insect cell projects to outside control (6). This trend has generally grown over at least the past four years.
Only 17% of companies in 2009 projected that over the next five years they would be outsourcing projects involving insect cells (compared with 33% interested in outsourcing insect cell work the previous year). With respect to plant cells, 33% of companies in 2009 indicated that as an area for outsourcing over the coming five years. Although this represented an increase over the previous year, the figure represented the first rise since the 2007 survey for this aspect of outsourcing.
Critical Outsourcing Issues: We evaluated responses to critical issues concerning the outsourcing of biomanufacturing to a CMO. Of those respondents indicating an attribute was important or very important, “comply with my company’s quality standards” topped the list, with 93.3% considering it important or very important (Figure 6). Following that was “protect intellectual property,” which showed up with 90.5%, pointing to biomanufacturers’ desire for keeping their product-specific manufacturing operations proprietary. That may be the result of an increased focus on outsourcing of operations. “Establish a good working relationship” and “effectively handle cross-contamination issues” followed in importance, suggesting that sponsors are demanding greater levels of effectiveness in managerial and technical areas from their contractors.
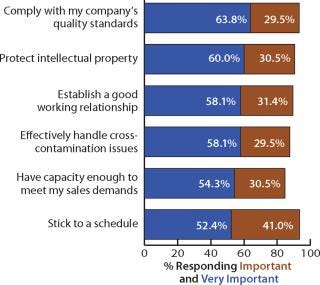
Figure 6: ()
Contrary to commentary and experience among many contractors and sponsors these days, the importance of a CMO’s location continues to be relatively unimportant (with 10.4% in 2005 and 4.8% today indicating the factor as very important). This may be a function related to globalization of this industry, with the off-shoring of greater numbers of successful production projects.
Over the past four years the attribute rankings have shifted to some extent. For example, we found that “establish a good working relationship” is always a top contender that varies from year to year. It moved from the #4 spot in 2006 to #1 last year and #2 this year, with 58.1% of respondents indicating it as a critical selection attribute. Despite the maturation of the biopharmaceutical industry, these data suggest that customer service and establishment of good client–vendor relationships appear to have gotten worse over the past few years, not better. The current economic situation may exacerbate this problem. “Sticking to a schedule” is another soft client-relationship issue that does not seem to be resolving. In 2005, 47% of respondents indicated it was very important — compared with 52.4% today.
Capacity Trends
Capacity constraints continue to be an issue for commercial-scale biomanufacturers, but constraints at later clinical stages appear to be easing. In 2009, 19.7% of respondents reported experiencing severe or significant constraints at the commercial manufacturing level (compared with 17.3% in 2008). We found that 39.4% were experiencing more than just minor constraints (not very different from 39.7% in 2008). In addition, 12.3% of respondents were experiencing severe or significant constraints at “later-stage clinical manufacturing” (phase 3) compared with 14.3% last year, and 31.3% were experiencing more than just minor constraints (also barely changed from 31.8% last year).
From 2003 to 2009, capacity constraints have loosened significantly. Today, 13.4% of respondents at all manufacturing scales reported that their facilities are experiencing significant or severe capacity constraints, whereas 47.9% reported experiencing no constraints at all. This is consistent with a general trend over the past several years toward a lessening of capacity constraints. The trend reflects many factors including improved efficiencies and productivities, shrinking of the product blockbuster product pipeline, global economic factors, better capacity management by the industry, improved market and production forecasting, more flexible expression systems, and wider access to outsourced capacity.
Factors Creating Future Capacity Constraints: We asked respondents to identify the major factors that were likely to constrain their organizations’ production capacity over the next five years. This year, the most frequently checked factors were “facility constraints” (55.4%), “physical capacity of downstream purification equipment” (41.7%), “analytical testing and drug product release” (31.9%), and “costs associated with downstream purification” (29.4%). Those respondents who felt that they were “unlikely to see capacity constraints in five years” were in the minority (10%), down significantly from the 21.4% of respondents who indicated last year that they did not expect capacity constraints.
Despite the global economic downturn, scientific labor markets seem to be tightening somewhat.Expectations of constraints due to the “inability to hire new, experienced scientific staff ” jumped from 15.9% of respondents last year to 22.7% this year. Much of the tightening in the market for experienced bioprocessing specialists may not be due to an actual shortage. Instead, those specialists are increasingly spread out over a growing number of biopharmaceutical companies worldwide, including dozens of new biosimilar entrants and many new companies in India, China, and other developing countries worldwide.
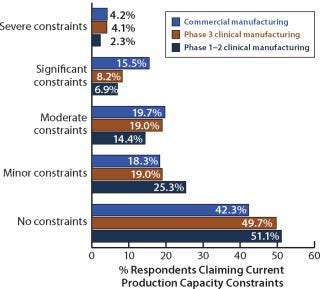
Figure 7: ()
From Growing Pains to the Challenges of Maturity
Among other findings, the seventh annual report quantifies how outsourcing has changed as the biopharmaceutical industry has matured. Today, most companies recognize the strategic necessity of using their internal resources more efficiently and focusing on core competencies. Outsourcing can improve overall efficiencies while reducing costs. However, management of relationships continues to evolve as contract manufacturers restructure their service offerings to ensure they provide the flexibility to meet the shifting needs of their clients. This change in relationship management will probably take some time as current economic, hiring, and budgetary realities settle in.
Today, most areas of R&D and manufacturing are being considered for outsourcing. The impact is being felt globally, with emerging markets showing favorably alongside established markets as potential outsourcing destinations. The increase in outsourcing has led to some companies establishing centralized contracting groups to handle the complex and time-consuming business of selecting and managing outsource partners. This provides for greater consistency in evaluating the progress of projects, and it can reduce start-up times. As the use of contract partners becomes more embedded into the strategy of biopharmaceutical companies, effective contract management will become a more critical issue.
SURVEY METHODOLOGY
This seventh in the series of annual evaluations by BioPlan Associates, Inc. yields a composite view and trend analysis from 327 responsible individuals at biopharmaceutical manufacturers and contract manufacturing organizations (CMOs) in 35 countries. The methodology also encompassed 125 direct suppliers of materials, services, and equipment to this industry. This year’s survey covers such issues as current capacity, future capacity constraints, expansions, use of disposables, trends and budgets in disposables, trends in downstream purification, quality management and control, hiring issues, employment, and training. The quantitative trend analysis provides details and comparisons of production by biotherapeutic developers and CMOs. It also evaluates trends over time and assesses differences in the world’s major markets in the United States and Europe. Other areas tested include downstream process development, API biologics manufacturing, contract manufacturing of biologics, upstream process development, regulatory services, testing (lot release, media optimization, cell line development and stability, environmental monitoring services, design of experiments, and host cell protein analysis), plant maintenance services, upstream production operations, GMP training, contract research (laboratory), and quality by design services
About the Author
Author Details
Eric S. Langer is president of BioPlan Associates, Inc., a biotechnology and life sciences marketing research and publishing firm established in Rockville, MD in 1989; 1-301-921-5979; [email protected]; www.bioplanassociates.com. He is editor of numerous studies including the second-edition Advances in Large-scale Biopharmaceutical Manufacturing, and publisher of industry reports.
REFERENCES
1.) Langer, ES. 2010. Seventh Annual Report and Survey of Biopharmaceutical Manufacturing Capacity and Production, BioPlan Associates, Inc., Rockville.
2.) Langer, ES. 2009. Quick Guide to Biopharmaceuticals in the Middle East, BioPlan Associates, Inc., Rockville.
3.) 2008. The Pharmaceutical Industry in Europe: Key Facts and Figures, European Federation of Pharmaceutical Industry Associations (EFPIA), Brussels.
4.) Zhou, EY. 2006.Biopharma CMOs In China Contract Pharma.
5.) Mehelic, P. 2010.Case Study: Analytical Due Diligence to Enable Multi-Project Platform Analytics Support Outsourcing Manufacturing of Biopharmaceuticals, IBC Life Sciences, Westborough.
6.) Rader, R. 2007. Biopharmaceutical Products in US and European Markets, BioPlan Associates, Inc., Rockville.
You May Also Like