Reducing the Environmental Impact of Single-Use SystemsReducing the Environmental Impact of Single-Use Systems
Committed to sustainability, EMD Millipore is working to provide solutions for the life sciences industry. This commitment is driven by four global issues: climate protection, global health, clean water, and resource efficiency. The company is designing product and process improvements to address these challenges and meet customer expectations.
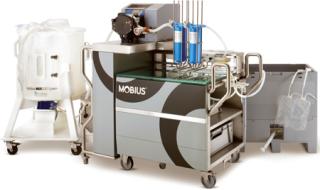
Figure 1: ()
Life-cycle assessment (LCA) is one of the most rigorous tools we use to help us understand and quantify our products’ environmental impacts (Figure 1). This holistic, science-based evaluation informs our company’s design, supply chain management, and product stewardship decisions. LCA allows us to identify improvement opportunities and provide environmental impact information to customers who seek such data to help them understand their own environmental footprints. EMD Millipore has performed LCAs on several representative products from key product lines, and it continues to build on that knowledge base with new LCA studies. The benefits of these analyses go far beyond the narrow limits of each study: Results spur sustainable design decisions for similar products and foster innovation in emerging product categories. The company is also integrating a “design for sustainability” approach into the product development process and piloting the use of a quantitative scorecard to evaluate environmental impacts, materials, manufacturing processes, and end-of-life management on proposed designs.
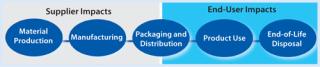
Figure 1: ()
Our LCA work has revealed that most opportunities for improving the environmental performance of single-use systems reside with their manufacturers, whereas many efficiencies that can be achieved with traditional, multiuse systems are under end-user control. As a manufacturer of disposable products, EMD Millipore thus has a responsibility to identify and pursue sustainable options.
The perception remains that single-use products have a greater environmental impact than do traditional approaches to biomanufacturing because they create significant quantities of visible waste. Although end-user benefits of lowered contamination risk, reduced cleaning and validation requirements, and increased flexibility are clear, the environmental effects are not.
To shed light on the “hot spots” associated with single-use systems, we conducted a comprehensive LCA of a 500-L Mobius buffer-media filtration (BMF) system. Two plastic film storage and mixing bags are key components. Some customers have voiced concern over the environmental impact associated with disposing of the plastic in those bags, so we investigated alternative end-of-life scenarios. We also studyied improvement opportunities associated with other life-cycle phases of our products.
We used appropriate ISO 14044 methodologies for our LCA, then evaluated the data with the ReCiPe 2008 impact assessment methodology (www.lcia-recipe.net). It measures processes according to 15 environmental-impact categories that include climate change, ozone generation, and water depletion. Here we focus on global warming potential (GWP), which serves as a useful surrogate for other impacts. It is also of particular interest when evaluating incineration, which is a common disposal pathway for single-use bioprocess systems.
Environmental Considerations in Manufacturing
Production of buffer solutions, using either single-use or traditional systems, consumes a considerable amount of energy. Our study results showed that making 200 500-L batches of buffer consumes ~605,000 MJ (megajoules) of energy, which is enough to heat 14 homes for a year. Associated life-cycle greenhouse-gas (GHG) emissions were equivalent to burning 5,000 gallons of gasoline.
Our overall results were very informative, yielding data about materials selection and process implications for our product managers and designers. Three findings regarding the manufacturing and distribution life-cycle phases stood out:
Supply chain management (12.5% of overall GHG emissions contributed by transportation of key subcomponents manufactured by third parties)
Shipping to end-users (GWP strongly influenced by customer location and mode of product transport; air transport to a Tokyo customer increased overall GWP by 48% over trucking product to a local customer)
Cleanroom HVAC needs (48% of life-cycle GWP from GHG emissions based on electricity and natural gas use during bag manufacturing and system assembly).
Our LCA quantified the energy used by cleanroom heating, ventilation, and air-conditioning systems as a key opportunity for improvement. EMD Millipore already has a number of initiatives under way to address all those findings. Mobius devices are manufactured in a LEED (Leadership in Energy and Environmental Design) gold facility in Danvers, MA (1). Facility improvements including addition of a particle counter allowed the company to change cleanroom airflow from a continuous stream to as-needed, reducing natural gas use by 26%. Adding a third manufacturing shift and increasing the production rate (products produced per square meter of floor space) reduced per-product GWP intensity. Other initiatives focus on minimizing air shipment of components and products to improve supply chain transportation efficiency.
Environmental Considerations in Disposal
We are exploring several end-of-life management options to reduce environmental impacts of our single-use products and address customer concerns about waste disposal. Our desire for robust scientific data to support this decision-making spurred an LCA study covering the environmental impacts of alternative end-of-life scenarios. Through this study, we determined that the disposal method with the highest GWP is incineration without energy recovery (Figure 2). When that method was modeled for the buffer-media filtration system, it represented 9% of the product’s total life-cycle GWP.
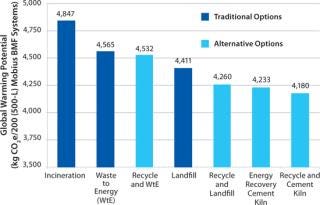
Figure 2: ()
We evaluated other end-of-life options: land-filling, waste-to-energy, waste recovery using products as fuel in cement kilns, and recycling. As Figure 2 shows, these options significantly affect the product’s overall life-cycle emissions. Note that analysis of recycling excluded mixed materials and components that were difficult to disassemble; if those could be realistically recycled, that would add a more comprehensive recycling option to the list.
Traditional Waste-Disposal Methods and Challenges: Although the end-user benefits of disposable systems are clear (lower risk of contamination, reduced cleaning and associated validation requirements, and increased flexibility), many companies struggle with managing the waste they generate. A number of challenges come with disposal of single-use buffer-media filtration systems. Mobius products contain a number of different types of plastics that cannot be easily disassembled or separated, which makes them difficult to recycle. Used systems can be contaminated with residual buffers or media, further complicating recycling efforts. Existing recycling infrastructure and regulatory guidance are inadequate.
Disposal options are limited in some regions, and landfilling may be the least expensive option. However, traditional waste management methods — such as landfilling and incineration, with or without energy recovery — do not address waste recovery and recycling goals of many end-users. As more companies adopt recycling or “zero-waste” goals, the need to provide a viable recycling process becomes more pressing.
Alternative Disposal Methods Are Innovative Solutions: In working to devise innovative solutions for better disposal of its single-use products, our company has developed two proposed options that involve energy recovery and recycling. From LCA studies of both alternative end-of-life scenarios, we found that they deliver a positive environmental benefit over traditional methods. And from speaking with various customers, we found that diverting waste from landfills and incinerators drives up energy recovery and recycling rates, which benefits customers in achieving common corporate goals related to sustainability. Identifying alternative disposal methods also provides an opportunity for vendors to be responsible for the end-of-life of their own products, which shifts that burden away from their customers.
Energy Recovery: The high energy content of plastic components in discarded single-use systems (~16,200 BTU/lb) makes the waste a cleaner fuel source than bituminous coal (~11,000 BTU/lb). Our company has evaluated repurposing single-use materials once destined for a landfill or incinerator into a useful source of energy through a waste-conversion process. This solution is significant for companies that consume a large quantity of single-use products that may currently be considered biological waste. Based on our end-of-life LCA study, this innovative disposal method involving energy recovery at cement kilns could decrease GWP by 13% compared with incineration and by 4% compared with landfilling. If every Mobius unit sold over one year in the United States was returned for this end-disposal method (rather than landfilled), 24.25 billion BTUs would be saved each year: enough energy to heat 600 homes for that same time.
Recycling: Our LCA study also verified that recycling these products reduces their environmental impact despite the energy used for material transportation and the recycling process itself. Our vision for end-of-life management with our single-use products is to find their highest-value use, whether that is energy recovery in the short-term or recycling and/or repurposing the plastic components into other products over the long-term. We have partnered with a recycling company to explore the logistical issues associated with recycling plastic components from EMD Millipore units. We are currently piloting this solution with a few US customers.
EMD Millipore plans to expand its product stewardship program to customers in the United States. The pilot project builds on the success of the company’s Ech2o product take-back and recycling program for laboratory water purification cartridges (in partnership with Heritage Environmental Services (www.heritage-enviro.com). Successful product take-back and recycling programs of this type require a high level of customer participation, identification of the best possible use for used materials, and establishment of markets for those material.
Our LCA study confirmed the positive environmental impact of this ground-breaking initiative. And a third-party peer review of our results is currently underway for further verification. As more customers embrace the new product stewardship opportunities we offer, our company will be able to explore more options to upcycle its products, deriving even greater environmental benefit than that from their original value. We are communicating our findings concerning the barriers to recycling back to our colleagues in product design in hopes that they can identify and incorporate solutions into the future products (e.g., designing for disassembly and reuse of recoverable materials into new products).
On the Road to Sustainability
We’ve highlighted some of the sustainability efforts under way at our company. Even though we have had some successes, we know that this is just the beginning of our sustainability journey. EMD Millipore seeks to partner with customers to align its sustainability strategy with their priorities. We want our products to help further their goals — whether those are in waste management, optimized manufacturing processes for reduced energy or water consumption, or reducing carbon footprints.
Our company will continue to integrate a design-for-sustainability focus across the bioprocessing system life cycle. We are committed to using rigorous tools such as product sustainability scorecards and LCA to identify environmental impact hot spots and guide improvements such as reducing hazardous substances, lightweighting, and design for disassembly in new product design.
About the Author
Author Details
Johanna C. Jobin is sustainability manager ([email protected]), and Mani Krishnan is director of single-use processing systems ([email protected]) at EMD Millipore Corporation, 80 Ashby Road, Bedford, MA, USA 01730. Mobius is a registered trademark of Millipore Corporation.
REFERENCES
1.) Scott, C. 2011. Sustainability in Bioprocessing. BioProcess Int. 9:32.
You May Also Like