Water is a key raw material used in manufacturing products within the healthcare, pharmaceutical, and biopharmaceutical industries. Microorganisms found in these water systems are mainly stressed, slow-growing strains characterized by long incubation times (five to seven days) before growth can be detected using traditional microbiology methods such as membrane filtration or pour plates. That time required before contamination can be detected in water can cause delays in product release and extend the storage time of products.
Using rapid detection methods, manufacturers can address contamination events sooner, avoid line shutdowns, release product to the market faster, and reduce warehousing costs. This study assesses the ability of the Milliflex Quantum System to detect microbial contaminants in pharmaceutical waters and evaluates its reduction of time-to-result compared with the five to seven days of the compendial method.
Methods and Results
Purified waters are sampled from sampling points from two di...
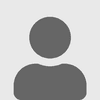
+3As the adoption of single-use products continues to grow at a very fast pace in the biopharmaceutical industry, customers and suppliers are becoming increasingly aware of the potential impact of these products on the net environmental footprint of operations. At Millipore, a key goal is to design and manufacture products with the lowest carbon and water footprints possible and to ensure that these products are managed in the most environmentally friendly way.
Millipore’s sustainability vision calls for the company’s operations to become environmentally sustainable in the long-term by dramatically reducing the consumption of nonrenewable resources, reducing waste, and adopting behavioral changes that support sustainability companywide. The multiprong sustainability approach includes specific initiatives focusing on climate and energy, waste, water, employees and communication, and product packaging.
These are challenging goals as our business has grown, but we have already made a great deal of progress sin...
A Comprehensive Solution
Innovative Viresolve Pro Family:
Robust, productive, next generation
Quality and Manufacturing Expertise:
Over 15 years of virus filter manufacturing experience; state-of-the-art membrane plant; comprehensive validation; raising the standard of performance and integrity tests
Industry-Leading Service and Support:
Process development, optimization, and scale-up; leading the industry with spiking strategy and validation; services covering every stage of adoption
Building Assurance Test By Test (Figure 1)
No one does more than Millipore to help assure virus filter performance and compliance: end-user validation and testing; device 100% tests (newly patented binary gas test); device release tests; membrane release tests; and process and product validation.
Figure 1: ()
Key Benefits (Figure 2)
Process Robustness:
Enables increased process robustness; protects against variability with respect to changes in solution conditions; relatively insensitive to stream plugging characteristic...
Mycoplasma is known to be a common source of bioprocessing contamination and one of the most difficult contaminants to detect. The effect of a mycoplasma contamination can be catastrophic, resulting in loss of a batch, loss of future production, down-time for investigation and corrective actions, and the potential risk of therapeutic supply shortages to immunocompromised patients.
To demonstrate Millipore Express SHR filters’ mycoplasma clearance capability over extended filtration times, two separate
Acholeplasma laidlawii
retention studies were performed using sterilizing-grade Millipore Express SHR with Prefilter (0.1-µm polyethersulfone) filters and
A. laidlawii
ATCC® 23206. In these experiments, the test conditions were modeled after typical cell culture processes, and testing was conducted using a low organism challenge level and typical operating pressures. The first experiment tested filters at production scale in a 3×30″ cartridge configuration (44,100 cm
2
). A second experiment tested the r...
In the pharmaceutical industry, there is a strong desire to introduce new drugs on the market as fast as possible (time-to-market) due to time-limited patent protection for new pharmaceutical products. The thinking behind this desire is simple: the sooner a new product can be introduced to the market, the sooner patients can benefit, and the better are the manufacturer’s prospects of financial returns. This consideration, however, should not allow compromises to enter into the manufacturing process design. This article provides an example of how good process design can both optimize and expedite the harvesting of cells in a biotechnological process.
In practice, there is a tendency to overlook the fact that a purification process developed at a small laboratory scale will not always work smoothly at pilot and commercial process scale. An effective scale-up cannot be taken for granted. Scale-up requires detailed knowledge of the process and of the tools required to implement and control it. The scale-up of...
Albumin and albumin-related proteins such as albumin fusion proteins represent an increasingly important platform for production of therapeutic proteins with extended in vivo half-lives. Affinity ligands directed to the albumin portion of the molecule are ideally suited to development of a purification platform for albumin containing proteins. In addition, significant reductions in manufacturing costs are possible, especially if processing times can be shortened through use of higher flow rates.
Introduction
Mimetic Blue® SA ligand is selective for human serum albumin and commonly used for the purification of human albumin and albumin fusion proteins. Optimization of the PuraBead® base matrix (6% beaded agarose) cross-linking chemistry and Mimetic Blue® SA ligand coupling has led to the development of an improved adsorbent called Mimetic Blue® SA HL P6HF. This new SAHLP6HF product retains the excellent selectivity and high binding capacity (up to 30 g albumin/L) provided by Mimetic Blue® SA HL P6XL produc...
The demand for biopharmaceutical products, in particular, monoclonal antibodies (MAbs), is rapidly increasing during recent years. The necessity for pharmaceutical companies of being first to market combined with the need to cut development costs makes the application for high-throughput screening (HTS) techniques and tools in downstream process development indispensable.
Atoll’s 96 MediaScout® RoboColumn® array together with Tecan’s Freedom EVO® liquid handling workstation enables fully automated parallel column chromatography for the first time.
The RoboColumn® design allows the user to select any chromatographic material which is packed with due consideration to individual material compression requirements. Bed containment between two filter frits ensures high efficiency and peak symmetry similar to that of preparative and process separation columns and distinguishes the system from the current filter based systems for simple on/off sample equilibration operation.
This article describes how automated p...
Chromatographic resins for a new purification process are initially selected based on prior experience and knowledge of the feedstock and the target compound. As the process scales larger, and hopefully through therapeutic commercialization, developers seek opportunities to maximize throughput, remove impurities, and reduce cost.
Responding to the dramatic increase in batch titers over the past decade, products such as the Toyopearl GigaCap series of resins (first introduced in 2007) were developed to meet the titer challenge with their high capacities and faster elution kinetics. Not surprisingly, process developers are taking advantage of these developments to improve their process platform by replacing traditional purification media with high dynamic binding capacity (DBC) resins for the capture step.
While this approach is making a positive impact in the industry, the combination of higher protein titers of feedstocks, higher DBCs of the capture resins, and a 60–70% reduction in target elution volume ...
Single-use systems have become all the rage in the biotechnology industry, driven largely by the need to reduce cleaning requirements and associated time, validation, and cost factors associated with stainless vessels. A well-developed single-use system will ensure lower risk of contamination in manufacturing while eliminating the cleaning process and cleaning validation.
Providing Solutions
Advanced Scientifics provides specific solutions to process needs in fluid transfer and handling, offering flexibility in the design and componentry of individual systems.
Advanced Scientifics offers a wide assortment of transfer and filtration sets for most any application, providing sets that are used throughout the cell culture/fermentation process, from media or buffer transfer to seeding or harvest — to separation and purification — to final packaging. Advanced Scientifics offers more than 80 different tubing sizes and types, as well as more than 900 off-the-shelf connectors. As a leader in the design and manufac...
At a time when most companies endure the effects of a global economic melt-down, ALLpaQ™ seizes the opportunity for growth on the international stage. ALLpaQ™ Packaging Ltd. develops, manufactures, and supplies standard and custom bioprocess containers for the storage, transportation, and handling of biopharmaceutical fluids on both three-dimensional (3D) and two-dimensional (2D) design platforms.
During the past twelve months, ALLpaQ™ has emerged as a strong contender on the world stage in providing packaging solutions to the biopharmaceutical industry. With over seven years of experience in bioprocess containers, the company is proud to be at the forefront of innovation and development, which provides its stability and platform for growth.
Philosophy
ALLpaQ™ is built upon the foundation of professional relationship. The culture of the company is founded upon sustainability, responsibility, and value added.
Our customers assume on-time performance and delivery; therefore, speed and reliability are viewed...
Applikon Biotechnology is the world’s leading manufacturer of glass autoclavable vessels. Over 25 years ago, autoclavable vessels were sold as systems by many companies. When large west-coast biotech companies wanted a modular approach and also wanted changes in the design of the vessel, Applikon listened and complied. The glass bioreactor is now the standard of the industry and is sold in similar forms by many of Applikon’s competitor.
Applikon has kept its focus on the bioreactor and anything related to or working with the bioreactor. In doing so, Applikon has become the innovator in this segment of the market. Through listening and observing, Applikon has introduced the following innovative products to the market:
Applikon’s business philosophy has evolved to be open to change and willing to accept new technologies from sources outside the industry.
Historically, the bioreactor supplier market has had high rates of turnover. This is due to the complexity of the equipment being used and the great need f...
Efficient movement and storage of liquids is critical to modern biotechnology processes. The deployment of single-use containers for this task has become ubiquitous in recent years because they reduce risk while driving down costs in comparison with traditional stainless steel equipment
ATMI’s integrity 2-d and 3-d Bioprocess vessel (BPV) products have been developed to meet the demand for cost-effective, scalable, single-use liquid storage containers that are compatible with ATMI’s market-leading range of single-use mixing and bioreactor technologies.
At the heart of ATMI’s Integrity systems and products is integrity TK8 film, a state-of-the-art multilayer gas-barrier polymer laminate. The product-contacting layer of TK8 film is blow extruded in-house by ATMI under cleanroom conditions using medical-grade ultralow-density polyethylene resin, then laminated to create a gas barrier film of exceptional cleanliness, strength, and clarity that is animal-derived component free (ADCF) and complies fully with US...
BioConnexx specializes in engineering, manufacturing, and distributing reusable and single-use fluid handling components and systems for the biotechnology and pharmaceutical fields. BioConnexx products are designed and manufactured to meet or exceed all standing guidelines and regulations with stringent material selection and carefully considered design. With years of intense and thorough research and engineering, BioConnexx has assembled a complete line of “off-the-shelf” and custom products manufactured under specific guidelines and engineering tolerances and tailored to meet the needs of GMP pharmaceutical and biotech processes.
Bio Valve
The Bio valve is a simple straightforward designed tube valve/clamp. It is easily manipulated and manufactured from a lightweight reinforced nylon. It may be easily applied to tubing in use and offers the option to calibrate flow through the tube. The design of both the gate and seat lends itself to being user friendly. Should the tube not be centralized within the va...
Catalent Pharma Solutions offers a total solution for the development and manufacture of biopharmaceutical and sterile products. Our proprietary technology — and expertise in working with proteins, peptides, and other biotechnology-derived active materials and small molecules — helps to maximize the potential of your API and accelerate your product’s speed to market. From cell line engineering to manufacture of API and drug product for clinical trials, our team of highly experienced protein chemists, biochemists, pharmacists, and pharmaceutical scientists provide the exceptional service, focus and expertise that your project needs.
GPEx® Technology
Setting a New Standard in Mammalian Cell Line Engineering and CGMP Manufacturing:
Catalent’s proprietary GPEx® (Gene Product Expression) technology enables genetic engineering of highly stable, high-yielding mammalian cell lines with unmatched speed and efficiency. More than 150 different antibodies and antibody fusions and more than 40 different recombinant p...
The high cell culture process (XD®) is a continuous process in which both cells and product are retained in a stirred-tank bioreactor using suspension mammalian culture. This is accomplished using a retention system: Fresh medium is continuously supplied, and metabolic byproducts are withdrawn and discarded through the retention system. XD® provides a controlled environment that leads to consistent product quality in terms of bioactivity, glycosylation pattern, and other product characteristics. Moreover, XD® technology is independent of the cell line (e.g., CHO, PER.C6®, hybridoma, myeloma). Developments have led to very high viable cell densities of >150 × 106 cells/ml and IGG concentrations of 10–27 g/L in a period of 10–14 days. In the case of CHO cells, XD® delivered 8–13 times higher titer than comparable fed-batch runs. With the XD® technology the volumetric productivity of the bioreactor is boosted to very high levels and can ideally produce large amounts of product with minimum development and in...
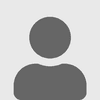
+2top) and TruBio µC (
bottom
()
In order to reduce scale-up costs and facility capital expenses, biotechnology companies are adopting single-use systems. To fully enable the single-use paradigm, automation software, hardware, and single-use sensors must be optimized; moreover, both validation documents and materials certifications must be readily available for cGMP implementations.
Finesse provides turn-key, configure-to-order measurement and automation solutions for many single-use bioreactor types: “stirred-tank,” “paddle,” or “rocker” systems. The Finesse turn-key system is optimized for each bioreactor type to maximize product yields. Finesse systems are scalable from R&D to process development to cGMP manufacturing. Finesse also provides full support for its systems, including installation, training, validation packages (FAT, SAT, IQ/OQ), and service/maintenance programs.
Figure 1:
top) and TruBio µC (
bottom
()
The primary enablers of single-use systems, however, are the sensors. Finesse offers di...
In response to the biopharmaceutical market needs, the focus of Irvine Scientific today is to provide chemically defined and animal-derived component-free cell culture media for use in the production of recombinant proteins. Drug development companies that do not invest in the costly and complex work of media development can rely on the services of Irvine Scientific to obtain and optimize formulas for their production cell lines. As the leader in rapid turn-around time for providing specially formulated products to clients, Irvine Scientific’s Express Media Service and Custom Media Service are the key aspects of the development and manufacturing services that differentiate our company from other media suppliers.
Media Development and Optimization
Our research and development team specializes in the development of optimized chemically defined media formulations for industrial applications. We can work with customers in many different capacities, using our services as much or as little as required.
Express ...
Life Technologies is at the forefront of a quest to improve the human condition. Growing numbers of biotherapeutics, revolutionary blood products, emerging biosimilars, and a vaccine industry moving toward cell culture–based production systems all promise to transform traditional disease treatment.
Leveraging core expertise in cell culture, downstream purification, and rapid molecular-based contaminant testing, life technologies offers biotherapeutic and vaccine production solutions under trusted GIBCO® and Applied Biosystems® Brands.
GIBCO® Media and Feeds for Upstream Cell Culture
New in 2010, GIBCO® CD FortiCHO, is a fortified, protein-free, animal origin-free medium for recombinant CHO cells designed to deliver better cell productivity, better cell growth, and longer culture duration. GIBCO® PD-direct Services continue to help with process optimization, spent media analysis and rapid prototyping.
POROS® Chromatography Resins for Downstream Purification
POROS® chromatography resins are today’s best-per...
The Mobius Cellready 3-L bioreactor is a single-use, stirred-tank bioreactor ideal for bench-scale cell culture of mammalian cells. The Mobius Cellready bioreactor is preassembled and gamma-irradiated to reduce set-up and cleaning times compared with glass stirred- tank reactors. It can be used right out of the box, and after a simple set-up, turn-around can be achieved in as little as a few hours.
The Mobius Cellready bioreactor has the benefit of single- use technology coupled with the familiarity of bench-top glass stirred-tank bioreactors. The system includes
The Mobius CellReady bioreactor has added functionality over traditional glass stirred-tank systems with subsurface integrated side sampling, liquid addition, and a bottom drain port for harvesting. The Mobius CellReady bioreactor integrates with most standard bioreactor controller configurations and most standard 3-L motors by a motor drive adaptor (sold separately). It is compatible with most standard 3-L scale heating blankets.
The Mobius Cell...
Transient transfection in mammalian cell lines provides an avenue for researchers to bridge the development bottleneck and shorten the time to usable protein. The method also maintains post translational modifications crucial for biotherapeutic function. Chinese hamster ovary (CHO) suspension cells are especially suited for high-yield production of recombinant proteins, despite being refractory to commonly used transfection methods (e.g., 25-KDa linear PEI). Mirus Bio has developed a more effective alternative, the
Trans
IT-PRO™ transfection kit. Using this kit increases yields of recombinant protein that can be obtained with minimal optimization of transfection parameters. Transfection complexes are made in serum-free media by adding plasmid dna,
Trans
IT-PRO Transfection Reagent, and the PRO Boost reagent (optional). After incubating complexes for 15–30 minutes, they can be added directly to cells in normal growth media. Transfection using the
Trans
IT-PRO Transfection Kit eliminates the need for a c...
Whether you are culturing animal cells in an R&D laboratory or in a pilot production facility, your ability to precisely control all process parameters is critical. Culture yield depends on it, and should your process go into production, FDA requirements mandate it. Therefore the performance of your bioreactor’s controller is as important as a good vessel design, as an optimized medium formulation, or selection of the right cell line.
This article focuses on the process control capabilities offered by the CelliGen® BLU, New Brunswick Scientific’s new, benchtop stirred-tank bioreactor with single-use, 5- and 14-L vessels. While much has been written (
1
,
2
,
3
) about its unique vessels, non-invasive sensor design, and rapid turnaround time between runs, much less has been documented about its custom-configurable process control capabilities. Designed to provide the flexibility for high-density growth of animal or insect cell lines, the highly flexible CelliGen BLU bioreactor is as capable as it is easy t...
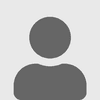
+1PBS 3-L benchtop bioreactor ()
PBS Biotech has emerged into the growing single-use bioprocessing space with an offering truly unlike any other: elegant, powerful, and incredibly easy-to-use bioreactors. A commitment to quality and innovation is evident in every design element of PBS Biotech’s Pneumatic Bioreactor System™. The proprietary Air-Wheel™ agitation mechanism powered by gas buoyancy provides unparalleled mixing performance for cell cultivation. The result is rapid liquid mixing, efficient mass transfer, and significantly lower shear stress — all of which remain consistent across the broad range of bioreactor scales offered.
The PBS Biotech platform of fully integrated, modular, single-use bioreactors includes bench-top R&D systems at 3 L and 15 L, pilot-lab systems at 80 L and 500 L, and manufacturing systems at 2,500 L and 5,000 L. The performance and elegance of design in these systems are only rivaled by the simplicity of their controls. The proprietary controller’s architecture is logical and...
Interferon beta-1b is a protein in the interferon family used to treat the relapsing-remitting form of multiple sclerosis (MS). Interferon beta-1b is a natural human protein (molecular weight ~18,500 Da) that is produced in the body in response to viral infection and has antiviral activity. It has been shown to slow the advance of MS and reduce the frequency of attacks. It is believed that interferon-beta achieves this effect on MS progress via its anti-inflammatory properties. interferon beta-1b drugs have been approved for over 20 years to treat the symptoms of MS. interferon beta-1b is produced as a recombinant protein in the bacterium
E. coli
by fermentation and subsequent purification to the active drug. The
E. coli
bacteria produce the interferon beta-1b molecule at low yield and as an insoluble and inactive product. As part of the purification process, the molecule must be restored to its active state, a process known as
refolding
. Refolding a protein molecule is a difficult, inefficient, and...
The use of 0.1-µm rated sterilizing grade filters has been increasing in cell culture media filtration due to mycoplasma contamination concerns. Currently, no standards exist for conducting mycoplasma retention testing on these 0.1-µm labeled filters. A task force has been established at PDA to publish a technical report to standardize testing. Until such guidelines are published, conducting side-by-side tests under identical conditions is the only fair way to compare different 0.1-µm rated filters. Sartorius Stedim Biotech has conducted such tests on its Sartopore® 2 0.2/0.1 PES 10” cartridge filters at a third party lab using a modified ASTM F838-05 method to show
A. Laidlawii
removal at LRV = 7/cm
2
.
Such mycoplasma-retentive filters usually have tight final membrane layers, and a high-performance prefilter is usually required to optimize the filter train. SSB has recently launched a new line of PES prefilters: Sartoguard®. These Prefilters are available in double layer PES as well as triple layer c...
Major drivers in biopharmaceutical development and manufacturing include improved performance in bioprocess cell culture through increased cell viability, product quality, and yield. Success has been achieved in addressing these drivers using Thermo Scientific HyClone Cell Boost by providing solutions that include strategic supplementation of nutrients based on metabolic profiling of cells and media at various stages of the bioprocessing cell culture campaign. One of the greatest improvements is derived from increased viable cell concentration and volumetric productivity. Today’s experienced fed-batch bioreactor operators can expect more than 10 times the efficiencies possible as compared to a few years ago (
1
).
Metabolic Pathway Design
High performance with Thermo Scientific HyClone Serum-Free Media for specific cell culture platforms is achieved through our Metabolic Pathway Design technology. Our approach to media formulation development ensures cell productivity during growth and production phases o...
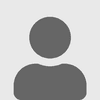
+1Whether evaluating conventional stainless steel or single-use bioreactors, every system must accomplish the same thing: control a bioprocess for an intended result. The result may be biomass, product titer, substrate conversion, or any number of complex, process-specific productivity measures.
Each system shares the same basic elements, including a bioreactor vessel and a gas addition subsystem. The vessel uses an agitation subassembly, gas sparger, and in some cases, gas overlay elements. These must be properly engineered to work in concert to deliver acceptable process performance. However, the presence of these features does not in itself ensure the growth of a culture, nor does it indicate the level of effort required to achieve the desired productivity.
Other factors — such as sound process engineering, a solid understanding of the bioprocess, and an understanding of critical system responses — play an equally important role. This paper examines a combination of unique capabilities designed into the ...
IDBS provides a flexible data management solution that meets the diverse demands of biologic drug development based on our extensive experience working with global biopharmaceutical and contract manufacturing organizations. the IDBS Bioprocess data Management solution enables streamlined execution of process workflows, improved data access, sharing and reporting, and the process insight needed to successfully reduce the time and cost required to deliver new biologics to market.
Managing Diverse Data
Biopharmaceutical companies generate a vast amount of high-value data that is then locked in paper records, enterprise databases or Microsoft® office file formats. This makes it problematic to realize the full value of these important assets and maintain a holistic view of the processes being developed.
The IDBS Solution creates a fully electronic development history record across the development lifecycle, helping process engineers to develop robust, scalable and transferable bioprocesses. By integrating and ...
As the pharmaceutical industry focuses on developing biological drugs derived using cell culture processes, the ability to optimize the growth, health, and potential yield of the cell line becomes increasingly important. Finding the optimal cell culture media is a daunting and time-consuming process due to the amount of potential media components and the unique requirements of the cell line being researched. Osmolality information is a crucial component to this research because of its close relationship between cells and media.
Background
Most current osmometers use freezing point depression technology to measure the total solute concentration of a liquid solution. Freezing point is considered the gold standard method in the pharmaceutical industry due to its accuracy and its broad applicability for almost any liquid sample type including complex media mixtures. Historically, high-throughput osmolality determinations have been limited due to the ability of the systems to process only one sample at a time ...
Bioengineering AG has been planning and constructing biotechnological plants for over 35 years. Holistic solutions have become the status quo: from inoculation to harvest, from feed line to CIP-system, and from automation to validation. The know-how acquired over years should not be limited to customers fermenting with Bioengineering equipment. Therefore all Bioengineering components are available as single parts. These custom-made components for a variety of special applications facilitate progress in culture technology.
Operational Safety
Crevices, deadlegs, and leaks are potential sources of microbial contamination or environmental hazards. Diaphragm valves and sterile couplings are necessary for process control and maintenance and often constitute the transition from unsterile to sterile plant segments. Bioengineering manufactures sterile couplings with deadleg-free passage and seals flush with the pipe wall. Hygienic diaphragm valves are available from manually operated one-way valves for simple appl...
The bacterial endotoxins test (BET) is unique because of its biases. Several biases in the BET are caused by the variability of standard endotoxin dilutions and the methodologies of the
Limulus
amebocyte lysate (LAL) test. The purpose of this study is to clarify those biases.
Bias from the Standard Endotoxin Dilutions
Operators for the BET often encounter variability of the potency in the standard endotoxin dilutions. To clarify the practical variability of the potency in the reference standard endotoxoin (RSE) dilutions, analysis was performed of the daily potency check in a Charles River laboratory. The operators confirm the potency of the RSE dilutions daily prepared for the kinetic turbidimetric assay (KTA) before use. The averages of the onset times at each endotoxin concentration were calculated. The total number of the measurement was 174 during the period between 10 September 2008 and 5 June 2009. An average standard curve was established using the average onset times and endotoxin concentration...